







Sustainable products and services
Implenia always aims to use sustainable solutions when working on building projects. The company can have the biggest influence on sustainability when developing its own real estate projects. Implenia also requires its suppliers and planners to operate sustainably and is actively committed to sustainable construction standards.
Content
Sustainability standards in building construction
There are a variety of sustainable construction standards within the industry. Labels such as LEED, DGNB, SNBS and Minergie set different requirements and focus on different aspects. Implenia had around 61 major building construction projects with sustainability certificates underway in Switzerland and Germany in 2021. That is approximately 165% more than in 2012.
About 40% of the revenue in 2021 of the division Buildings came from certified building construction projects.
As well as its considerable practical skills in implementing sustainability standards, Implenia has also helped develop and harmonise several of them. In recent years, for example, it has been involved as a founder member in formulating the “Standard Nachhaltiges Bauen Schweiz” (“Swiss Sustainable Construction Standard”, or SNBS), which integrates various existing approaches, such as 2000-Watt Society and Minergie-ECO. Implenia’s objective up to 2025 is to develop and build its projects to the highest sustainability standards and to help develop these standards further.
Implenia signed the Charta Gebäudelabels Schweiz (Swiss Building Label Charter) in 2020. Signatory organisations and companies use the various sustainable building labels to help Switzerland achieve its energy and climate objectives. Their aim is to carry out every construction project in accordance with a high energy or sustainability standard while also delivering high quality. Signatories of the charter also commit to only installing building technology that meets the most stringent energy efficiency requirements.
Sustainability certificates in building construction
in number
Sustainable neighbourhoods
These days, towns, communities and private organisations use sustainable criteria to design whole neighbourhoods. Implenia – which is often involved in such projects – founded the “One Planet Living Neighbourhoods” association in partnership with WWF Switzerland in 2018. The association has since been joined by further members, including construction companies, public authorities and housing cooperatives. The association developed the “SEED-Next Generation Living” certificate for pleasant living environments with a high quality of life.
The SEED approach defines an action plan for each project based on six sustainability principles and suggests ways of turning this plan into reality. The principles cover areas such as energy efficiency, environmentally friendly building materials, availability of local shops, and green mobility.
In addition to the environmental aspects, the approach promotes local business and social mixing. While investors can expect market returns, tenants benefit from fair rents. The SEED concept makes this possible by achieving a balance within the neighbourhood between zones with more and less services.
The first SEED neighbourhood in Switzerland is the Quartier Gruvatiez in Orbe, the first phase of which was completed in 2020. This project in Canton Vaud includes more than 200 homes and shops, a retirement home and a school. Concrete for construction was made using locally available aggregates. 70% of the ground surface remains unbuilt-on. Other SEED-projects are being built on the site of the old paper mill in Marly in Canton Freiburg and in the Geneva neighbourhood of Grand-Saconnex, where Implenia is planning a “Green Village” with a hotel, a residential block and several buildings for international organisations on a plot of land owned by the World Council of Churches.
Partnership with NNBS
The Netzwerk Nachhaltiges Bauen Schweiz (Swiss Sustainable Construction Network, NNBS) promotes the exchange of knowledge and experiences as well as cooperation between construction specialists in the commercial and public sectors, education, politics and science. Implenia is a founding and funding member of the network, and has had a place on its board since 2012. In 2020, the company extended its funding membership by another three years.
NNBS developed the Standard Nachhaltiges Bauen Schweiz (Swiss Sustainable Building Construction Standard, SNBS) in 2013. This has since been updated and can be applied to just about any type of project. Other initiatives, such as the 2000-Watt society and Minergie ECO, have been integrated into the industry standard. In 2020 the NNBS launched a practical tool that can be used to evaluate and compare the sustainability of infrastructure projects.
Implenia contributed its expertise to the development of this standard, and uses it regularly on its own construction projects. A good example of this is the new administration centre built for Canton Grisons in the city of Chur. The building, which was completed in 2020 and has space for 440 employees, sets a benchmark for energy use and fulfils the Minergie-P-ECO® standard. It has also gained “2000-Watt Site” certification for its sustainable use of resources, reduced emissions and encouragement of sustainable everyday mobility. The project has also won SNBS Platinum certification with a score of 5.7 – the highest awarded so far.
Sustainable services
If Implenia builds something for a customer as general or total contractor, the sustainability requirements are set by them, not by us. Right from the tendering stage, however, we systematically try to integrate sustainability concepts that exceed the actual project requirements into our services. This allows us to address wider sustainability issues even if this is not explicitly requested by the customer. We want to expand this approach by 2025 and apply it across the whole Group.
In the first stage, Implenia evaluates the potential customer’s sustainability strategy and objectives. Based on this we develop a targeted sustainability concept tailored to the customer’s needs and integrate it into the construction project. A successful example of this was a project we did for the United Nations in Geneva.
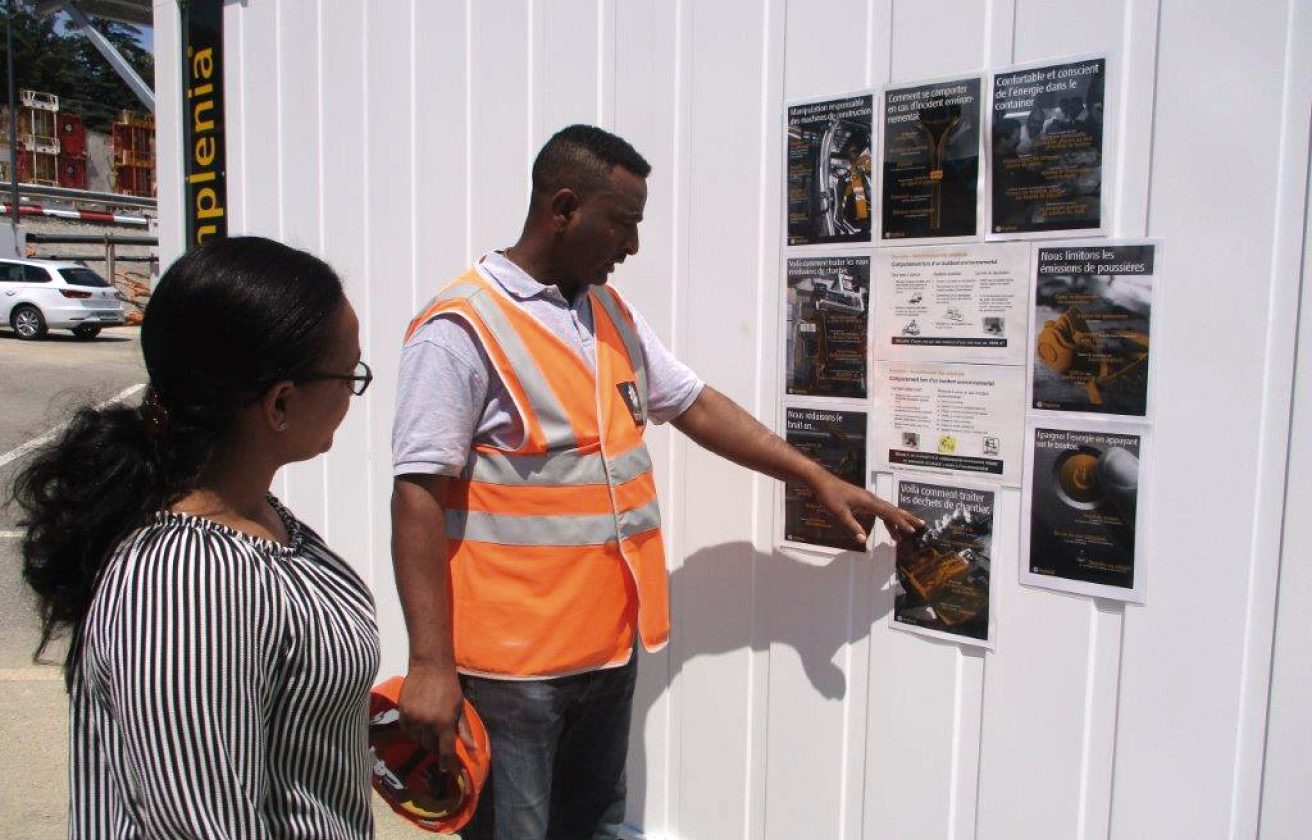
A new flower blooms in Geneva
Implenia is piloting its new sustainability concept, “Chantier Marguerite” at the construction site for a new United Nations office building. Refugees have been hired to work on site for the first time.
Read more
Recognition from rating agencies
In the most recent rating in 2022, Implenia achieved 67 out of 100 possible points from EcoVadis, the world’s largest provider of sustainability ratings (Scorecard). This result pushes our company up from last year’s silver status to gold, making it one of the top 5 percent of the over 90,000 companies rated by EcoVadis.

GeNaB® sustainability assessment
Implenia has a lot of scope to make its own real estate projects as sustainable as possible, because these are the projects it plans, designs – and usually builds – itself. When Implenia is the project developer, it can determine the location, the architecture, and the construction and energy concept at an early stage. These factors then affect all the subsequent phases of construction and, in particular, have a decisive impact on the sustainability of the building’s operation once complete.
As a project developer, since 2008 Implenia has been using its own proprietary tool to evaluate the sustainability of construction projects: GeNaB®, which in German stands for “Total Evaluation Of Sustainable Construction”. The tool allows Implenia to assess the sustainability of a building from planning right through to a final review of objectives, by applying 18 criteria in three dimensions – environmental, social and commercial. The company will only go ahead with its own development projects if they score at least 8 of the 12 points awarded under the system.
Implenia has continued to develop the tool ever since it was launched. This applies to the form of tool itself, which has evolved from a simple Excel file to a modern intranet application, but also to its content – the actual sustainability criteria that are measured. Our specialists in the Sustainability Department regularly update these and benchmark them against newly developed standards. During the latest review in January 2019, for example, they integrated the criteria from the Swiss Sustainable Construction Standard (SNBS).
The SNBS Building standard was developed under the lead of the Federal Office for Energy (BFE) and is part of the BFE’s family of building labels. Together with the other certificates in the family, the aim of this standard is to help implement Switzerland’s 2050 energy strategy within the construction sector. By adapting GeNaB® to the SNBS, Implenia can use GeNaB® as a kind of stepping stone to the SNBS itself.
With the expansion of development business in the German market, our internal sustainability specialists also defined internal requirements for sustainable building in Germany, and harmonised the GeNaB® criteria with the “Deutsche Gütesiegel Nachhaltiges Bauen DGNB”. GeNaB® Deutschland has been online since summer 2020.
Implenia uses a “materials exclusion list” when selecting construction materials so it can be sure that minimum environmental standards are met. The list include all the Minergie-ECO exclusion criteria, so if Implenia develops and builds its own projects it can be sure it is not using any materials that are damaging to the environment or health. This list is regularly updated and adapted as new information comes to light.

Ina Invest – a sustainable real estate portfolio
Ina Invest was spun off from Implenia and floated on the stock market in June 2020 in a move that should make the firm’s real estate division even more sustainable. Ina Invest’s aim is to have the most sustainable property portfolio in Switzerland. Around half of Implenia’s development portfolio was transferred to the new independent real estate company.
Ina Invest continues to develop the property portfolio in close long-term partnership with Implenia, expanding it with new acquisitions. The spun-off company is able to count on Implenia’s development and construction expertise as well as benefiting from its proximity to the market.
Meanwhile, Ina Invest augments Implenia’s value chain and opens up additional growth opportunities for the Group. Ina Invest has the financial capacity to develop its real estate plans more quickly and retain some of the projects within its portfolio even after completion.
Ina Invest uses the international GRESB sustainability benchmark to measure its sustainability performance. This set of indicators documents annual progress with regard to internal sustainability guidelines and stakeholder engagement. Energy and water consumption and waste generation within our own projects is measured and compared with that of similar portfolios.
Circular economy
To become sustainable, the economy as a whole has to move away from linear business models and start thinking in cycles. In practice this means that when products come to the end of their lives, the raw materials they contain are not destroyed or sent to land-fill, but are separated, treated and returned to the production cycle as secondary raw materials.
Such circular business models are vital in all sectors of the economy if we are not to exhaust our planet’s natural resources. Every year the Global Footprint Network announces “Earth Overshoot Day”: the day on which humanity has used up all the natural resources and services that the earth can regenerate that year. In recent years this has always arrived in July.
Implenia is committed to the circular economic model and by 2025 aims to develop circular business models and use innovative methods to close material cycles. It is crucial here not only to recycle materials, but to actually use the resulting secondary raw materials as well. Wherever possible, Implenia uses at least 50% recycled concrete for its own projects, made in a concrete works situated no more than 25 kilometres from the construction site.
Gravel produced by excavation work is sorted and processed on site where possible. The raw material is then used to make concrete or for backfilling within the same project. This reduces waste and saves on transport. The same approach is taken in tunnelling, where Implenia uses the rock it drills out to make concrete locally.
In the longer term, closing the materials cycle also requires integrated product design. New products have to be manufactured in such a way that the materials used can be separated out and sorted without excessive use of mechanical processes, energy or chemicals. Dry composite systems, for example, mean that individual construction modules can be easily replaced. Once they have come to the end of their useful life the different types of materials within the module can be sorted, separated and returned to the cycle as secondary raw materials.
Division Real Estate has followed this approach since 2020 under the guidance of its new REPOS unit (Real Estate Products & Off-site Solutions). REPOS addresses the need for flexible, cost-efficient and environmentally friendly solutions and uses standardised real estate products to help meet this need. The aim is to use off-site production and circular approaches to increase both quality and sustainability compared to more traditional construction methods, as well as to shorten delivery times and reduce cost uncertainties.
Building with timber
Alongside its conceptual tools, over recent years Implenia has developed extensive expertise in the use of sustainable techniques and materials – especially wooden construction. Thanks to new building methods and its low grey energy content, wood has regained its importance as a natural construction material.
In 2015 the Swiss federal government revised its fire safety regulations and allowed the construction of multi-storey timber buildings up to 100 metres high in Switzerland. Switzerland is blessed with large forested areas from which local wood can be obtained. If the raw material is purchased locally, the construction of timber buildings generates 30% less greenhouse gas emissions than conventional solid wall structures, so Implenia always considers and promotes local forest resources whenever possible.
Wood is highly suitable for making prefabricated construction elements. Another advantage of modular construction is that these elements can be used flexibly and are easy to replace. All of these benefits make wood an ideal building material within a closed cycle.
In the projects it develops itself, Implenia only uses wood and wooden materials that carry an FSC, PEFC or equivalent label. The company also supports FSC Switzerland in the implementation of important projects. The FSC standard is still not as widespread in construction as it is in the paper and printing industries. Implenia has made a financial contribution to help implement the Swiss forestry standard and develop an online tool to improve the marketing of certified wood within the construction sector.
In order to cope with growing demand, Implenia opened a new wooden construction production plant in Rümlang, Canton Zurich, in 2017. The 3,300 square metre plant allows Implenia to carry out more complex projects to the highest quality, and has increased the company’s production capacity by a third. Around 50,000 square metres of wood per year are now processed at the eight production benches in Rümlang. The production plant also helps reduce greenhouse gas emissions by using left-over wood to fuel the heating system for the main hall and neighbouring yard.
Its pioneering projects have made Implenia one of the leading players in the wooden construction segment in Switzerland.
- The company built the country’s biggest ever largest timber-built housing project in Winterthur: 8,100 cubic metres of wood were used to make the 307 apartments in the “sue&til” development, and around 80% of this wood came from Swiss forests.
- At the Lokstadt development, also in Winterthur, Implenia has built a wooden high-rise residential building known as “Krokodil”. Containing 254 apartments, some of them cooperatively owned, this building used 7,700 cubic meters of wood.
- The next big Implenia timber project is the new “KIM” neighbourhood in Oberwinterthur. Construction of this mixed-use residential and commercial building, with a total of 208 apartments, requires 5,500 cubic meters of wood.
- Project Pi in the Zug Tech Cluster, where Implenia is working as total contractor, will be the tallest timber-built high-rise in Switzerland. Around 80 metres tall, the building will be a beacon of environmental and social sustainability. The 10 “vertical neighbourhoods” within the building, each with 22 residential units on three floors, have been designed for new forms of living together.
Sustainable building materials
“b.congreen”
GRI 308-2
The main ingredient of concrete is cement, which is made using a very energy- and CO2 intensive process. In recent years, Implenia’s Materials Engineering Department has developed more sustainable recipes for concrete. One of these is a mixture in which fly ash sourced from power stations replaces some of the cement. Called “b.congreen”, it cuts greenhouse gases during production by up to 50%. The recipe is particularly suitable for bulky elements such as floor slabs, diaphragm walls and foundation piles.


“C3 – Carbon Concrete Composite”
Implenia’s materials engineering laboratory is also actively involved in the “C3 - Carbon Concrete Composite” research project. Experts are examining whether bundled carbon fibres can be used instead of steel to reinforce concrete. The carbon concrete they have developed is lighter than conventional steel-reinforced concrete, as well as more tensile and corrosion-resistant. The technology is also being used to retrofit structures for added strength. Carbon concrete saves resources in production and is easier to transport. All this has a positive effect on its CO2 balance.

“Ahadur”
More and more cars and trucks are using Switzerland’s roads. As a result, road surfaces and other structures have to be repaired at ever shorter intervals. In response, a new ultra-high-performance fibre-reinforced material has been developed that is designed to make roads more durable.
Implenia developed this road surfacing, called “Ahadur” in collaboration with KIBAG Management AG. The new material is characterised by very high mechanical strength and durability. Its high cement content makes it extremely resistant to mechanical abrasion, acid, sulphate and frost. Ahadur is also waterproof and vapour inhibiting. Thanks to all these properties, a single surface layer can replace several layers of a traditionally-built road. It is no longer necessary, for example, to seal cable sheaths against water or build in extra reinforcement.
Ahadur is easy to deform and hardens quickly even in wet weather. This can save clients around six to eight weeks of construction time. Being able to work faster saves on materials, reduces costs and means that lanes can open to traffic more quickly.
Innovative solutions
New materials, technical progress and ground-breaking insights are changing the construction industry quickly and profoundly. Implenia is harnessing these changes to the benefit of its customers, employees and shareholders. “Innovation” has been one of the company’s four strategic pillars since 2019.
Implenia focuses specifically on the following five fields of innovation:
- New services go beyond our current service portfolio, change traditional customer relationships and generate new revenue and business models along the value chain.
- New products offer integrated and scalable solutions for our customers at project level and beyond.
- New production refers to new materials, construction methods, value and supply chains, forms of management and process that facilitate economies of scale and volume, and improve quality.
- New sustainable solutions offer a high level of customer benefit, reduce environmental emissions, meet higher social standards and/or create long-term profitability.
- New simplicity refers to solutions that reduce complexity or remove bureaucratic obstacles by simplifying internal and external services, products and processes.
The Implenia Innovation Map provides an overview of trends, of existing and new areas of innovation, and of promising spheres of activity (“opportunity spaces”), as well as technological catalysts for the future of construction.
Innovation Hub
Implenia launched its Innovation Hub in September 2019, laying the foundations for a future-oriented innovation culture. The Innovation Hub taps into an important resource: the creativity of our approximately 10,000 employees. Many of them have good ideas about the work they do every day, and also have the experience and energy to implement these ideas in their own work environment.
Employees can submit their ideas via an online platform called Kickbox. This initiates a three-stage process that systematically assesses the suggested innovation’s suitability for everyday use. The person who submits the idea remains involved at every stage and is encouraged to develop it further with the support of innovation coaches.
In the first step, the “RedBox” phase, employees are given 20% of their work hours and a starting budget to validate their idea with the help of internal and external experts. If things go well, the second, “BlueBox” phase begins, where the idea is piloted with customers and users. If the pilot is successful and it seems that the idea has genuine commercial potential, we enter the “GoldBox” phase: the innovation is implemented with the support of Implenia’s management.
The core team at Implenia Sustainability helped develop the Innovation Hub and played a central role in the strategy. One of its contributions was to introduce “New Sustainable Solutions” as a separate innovation category. It also provides innovators with advisory services and helps them carry out a critical assessment of their idea from the sustainability perspective, improving it where necessary.
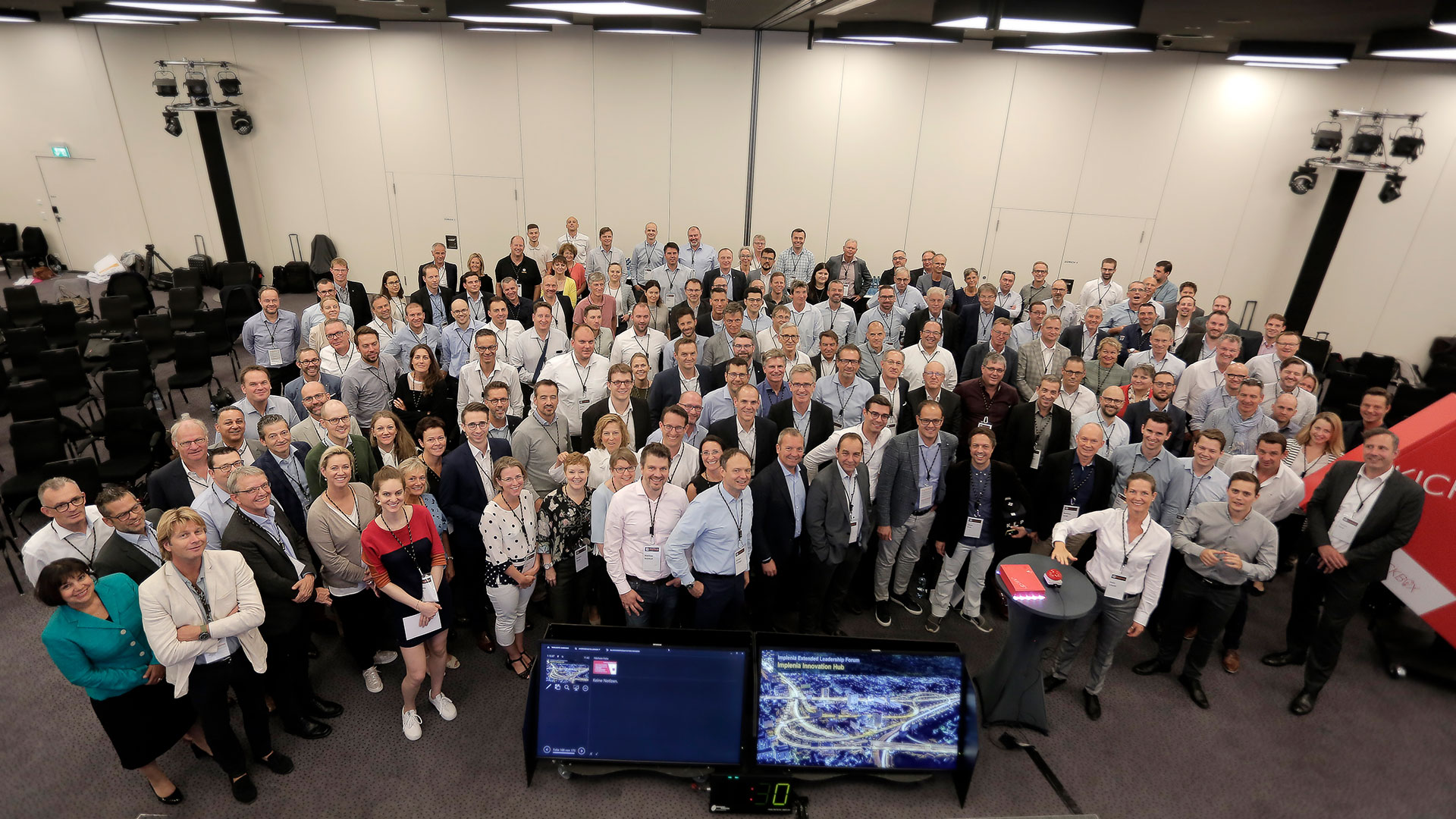
Facades as power generators
Since 2018, Implenia Facade Technology has been working on a way to supply buildings with energy generated by their facades. Working with the Fraunhofer Institute of Energy Economics and Energy System Technology, the engineers have developed facade elements that can provide the offices behind them with all the power they need.
As well as electricity-generating photovoltaic modules, these integrated components include micro-heat pumps, and ventilation systems with heat recovery technology. In the ideal case, as well as providing insulation the building envelope can therefore take over all the key building technology functions. The premises will not then need any additional heating, cooling or ventilation systems. With less cabling and pipework required, there is greater flexibility in the way the space within can be used.
And because the facade modules can be almost entirely prefabricated, construction time is reduced. The first module is currently being tested at the Fraunhofer Institute for Building Physics in Holzkirchen, Germany. The one-year test phase will show how well the module performs over the long term in different temperatures.
Supplier management
GRI 102-9, 308-1
As a construction and real estate services company, Implenia buys in building materials such as cement, steel, wood, plaster and paint from external suppliers, as well as sourcing construction services from external carpenters, plumbers, gardeners, etc. In total, the Group spends about 60% of its revenue on suppliers and subcontractors.
To avoid risks in this extended value chain, the company has used a systematic supplier management system since 2014. Suppliers and subcontractors go through a qualification process that forms the basis for a long-term working relationship. This requires them to disclose their social, environmental and economic profile. Of its approximately 5,000 subcontractors and suppliers in Switzerland, Implenia had evaluated 1,798 by the end of 2021.
All business partners must fulfil clearly defined minimum requirements relating to the environment, working conditions, health and safety at work, quality, purchasing and finance. If Implenia finds that a company is not meeting these minimum standards, the problem areas are discussed; no new contracts will be awarded to the company until the issues are sorted out.
By contrast, if a business partner goes beyond the minimum sustainability requirements, it is given additional points in Implenia’s evaluation system. For example, if a supplier can provide proof of the origin and recycling content of its products, it will receive a higher score. This allows partners who are committed to sustainability to improve their chances of winning contracts.
Implenia wants to work exclusively with sustainable partners. It has set itself a goal for 2025 of awarding at least 75% of its contracts by value to subcontractors and suppliers that have been evaluated according to sustainability criteria and that meet a higher standard. In addition, group-wide procurement policy should include sustainability criteria and all procurement specialists and project managers should receive appropriate training. Greater transparency in the supply chain should ensure there are no breaches of environmental or employment law.
Evaluated suppliers
in number of subcontractors and suppliers audited and evaluated according to environmental criteria