Turning spoil into concrete
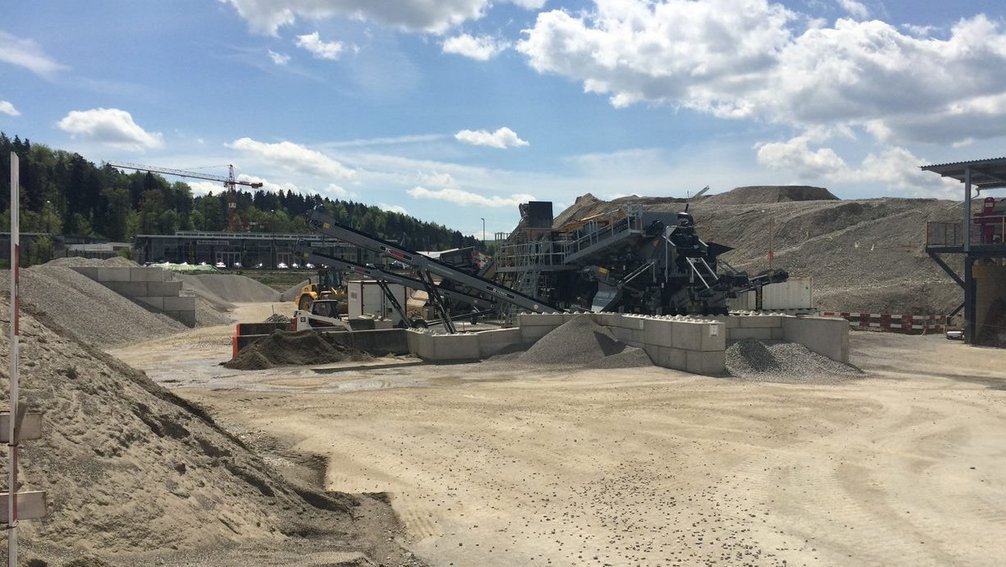
If you walk along the River Eulach in the eastern part of Winterthur, but then turn south away from the cleaned-up waterway you will inevitably come across a piece of Swiss industrial history. During the 19th and 20th century Sulzer, the engineering firm founded in this town, earned a worldwide reputation. It operated vast production sites which at their peak employed up to 30,000 people, making textiles machinery, energy systems, ships’ engines and much more besides. But then came globalisation and with it the demise of Swiss mechanical engineering. In 1990 Sulzer closed the engineering works and left its site in Winterthur to be used for other purposes. What is gradually emerging there now is a fascinating new part of town. Monuments to Winterthur’s industrial heritage, striking new buildings and public spaces are being injected with new life to create a district offering space for living, working, leisure and education.
Four year ago, when it took over Sulzer Immobilien AG, Implenia acquired extensive land and property next to the main railway station and out here in the eastern district of Neuhegi. Since then the company has worked with the town to develop the two abandoned industrial locations – a major benchmark project for Implenia, in which sustainability plays a key role. While one of the central concerns has been to retain existing buildings and reconfigure and enhance these where appropriate with replacement construction, Neuhegi is essentially witnessing the creation of a whole new district almost from the ground up. This is one of the largest development sites in Canton Zurich; eventually it should provide homes for 3500 people and workplaces for 7500.
In Neuhegi there are none of the romantic brick-built buildings or quaint workshops you find in the centre of Winterthur. The only reminders of the area’s industrial heyday are the exposed concrete foundations and ground floors of some of the former company buildings. There are, however, a whole series of new and impressive business and residential buildings, some of which have been built by Implenia. The new district south of the Eulach is slowly taking shape. Casual explorers will still feel a little lost in the middle of the large empty expanses, but their eyes are sure to be drawn to the strange mechanical contraption that growls and rumbles next to a huge pile of excavated material. With its massive metal skeleton and the whirring of its conveyor belt, from a distance it could be one of the amazing installations created by Jean Tinguely or Bernhard Luginbühl.
But the vibrating monster is not the work of an artist. In fact this mobile facility for recycling construction materials is the brainwave of one of Implenia’s project managers (see short interview). A hydraulic excavator works next to it, feeding excavated material into the loading hatch. The machine sieves and sorts the stones and rocks before washing them with water. Clean aggregate is then taken by conveyor belt and front-end loader to the neighbouring depot where it is kept in four different grades ready for further use. Implenia operates its own concrete works on the other side of the road, thus creating a complete materials cycle within a very small area: material excavated from the ground is refined on site and used to make concrete which is then used in construction work on the very same site. Even the water used for washing is recycled and used over and over again.
"Instead of all the transport that would be needed to take the spoil to landfill and bring concrete to the site, we do everything right here”, says Daniel Hardegger. As the Head of Roadworks / Civil Engineering at Implenia Zurich, he has operational responsibility for the recycling project. “It means we have cut the number of lorry trips through the town by more than half compared with a traditional construction site,” he adds. Over the course of the scheduled construction period from 2013 to 2020, this will save a total of 775,000 litres of diesel, and thus reduce CO2 emissions by 2300 tonnes.
Implenia invested around two million francs in the new washing and treatment plant, while the cost of processing the spoil comes to approximately 15 francs per cubic metre. However, the system also saves real money: much of the cost of disposal and transportation is removed, and Implenia needs to buy in barely any new raw gravel for making concrete. The figures add up in financial as well as environmental terms, then, especially when seen over the long term. “I’m sure the price of raw materials and disposal is only going to go up,” says Daniel Hardegger. The same goes for transport costs: fuel and heavy vehicle fees are rising fast. “The main thing though is that urban roads are getting increasingly congested, which causes long and expensive waits.”
Its in-house, on-site materials recycling and concrete-making plant gives Implenia greater flexibility in the operation of its construction site: no delays are caused by traffic jams and other external influences. “If it makes operational sense to pour one last layer in the late afternoon, we can produce the concrete right here, whereas all the concrete works will already have stopped for the day,” Hardegger explains. “This increases our productivity.” Ultimately, the system extends Implenia’s value chain, increasing its control over the production process and adding to its share of value creation.
It remains to be seen exactly how large these benefits turn out to be in practice. The facility in Neuhegi is currently in its test phase. “We are just gaining experience at the moment,” Hardegger admits. Coordinating the different stages in the recycling process, for example, is by no means easy. The grain size of the aggregate recovered from the spoil has to be matched to the needs of concrete production, for example. Timing is important too: excavation work and construction work have to be scheduled in such a way that the spoil excavated for one building can be used for concrete on the next. But the project manager is optimistic. “I’m confident that it will work well,” says Hardegger, emphasising that ultimately it’s the long-term impact that counts. He firmly believes that the experiences gained at Neuhegi will prove invaluable. “Mobile recycling of building materials is the future.”
LIZ, MAX, ROY AND CO.
Implenia is developing a series of major buildings on the large Sulzer site in Neuhegi. The first of these were the two residential and commercial properties liz and max. And then on the site of the former foundry, Implenia is constructing a six-storey, sustainable residential building with a wooden facade. On Sulzerallee, the main road through the new district, it is building a new technology centre for toolmaker Mori Seiki. Opposite this Implenia is working on “roy”, another sustainable residential development (more on roy). Building work on sue and til begins in 2015, followed by kim in 2017 / 18.