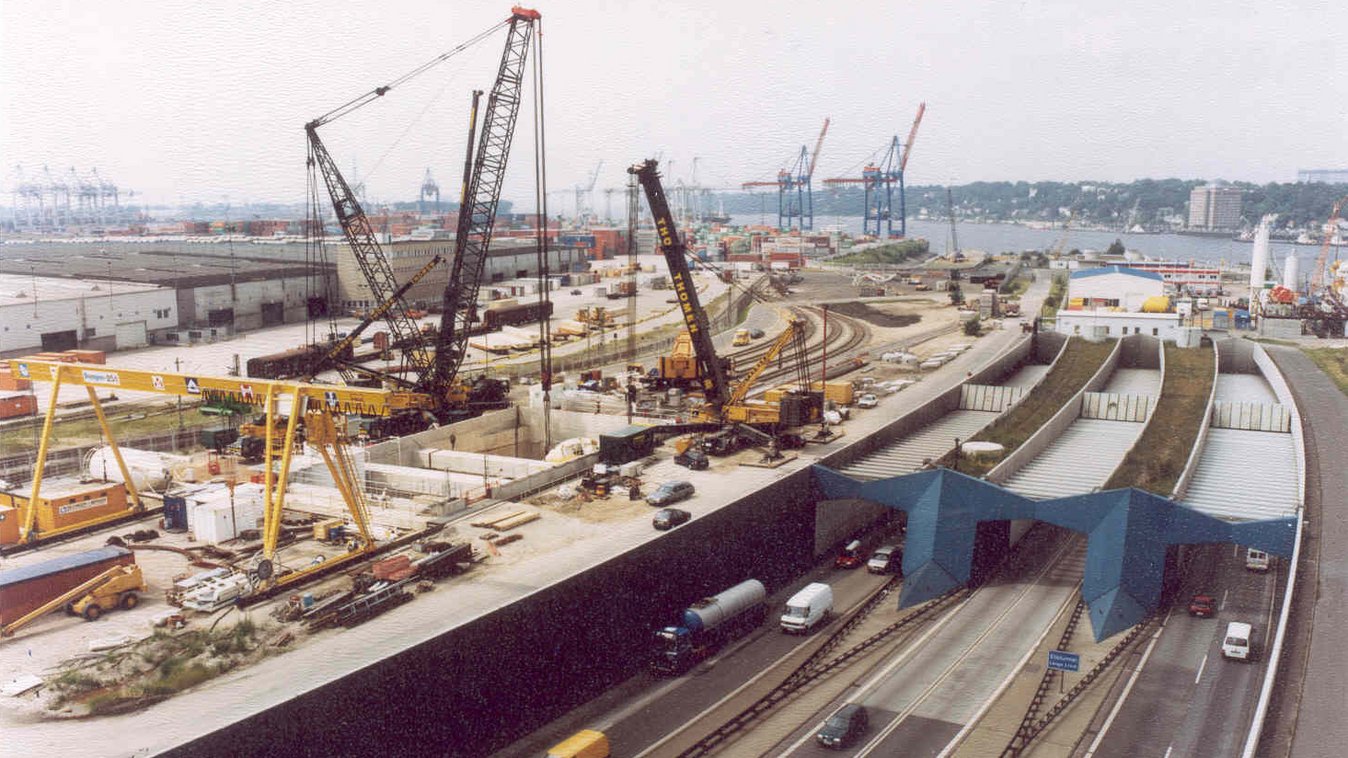
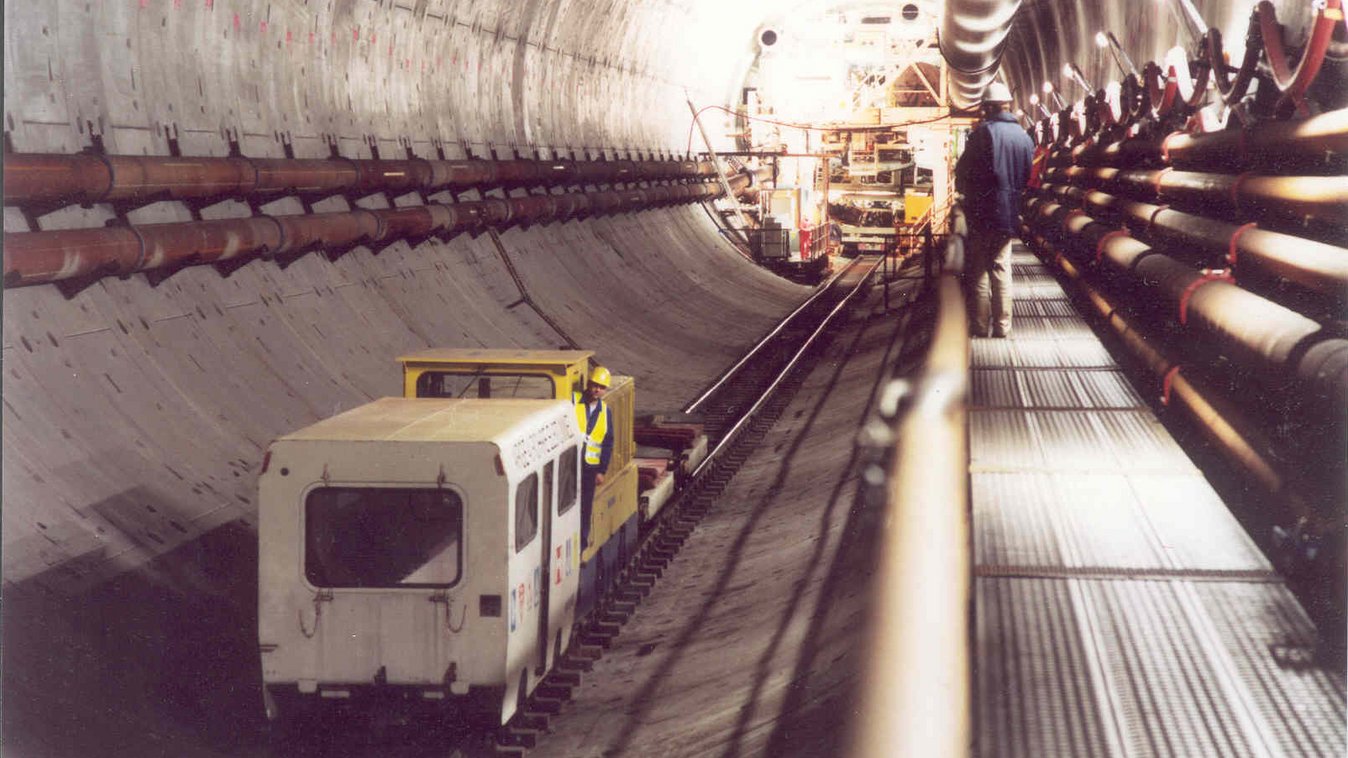
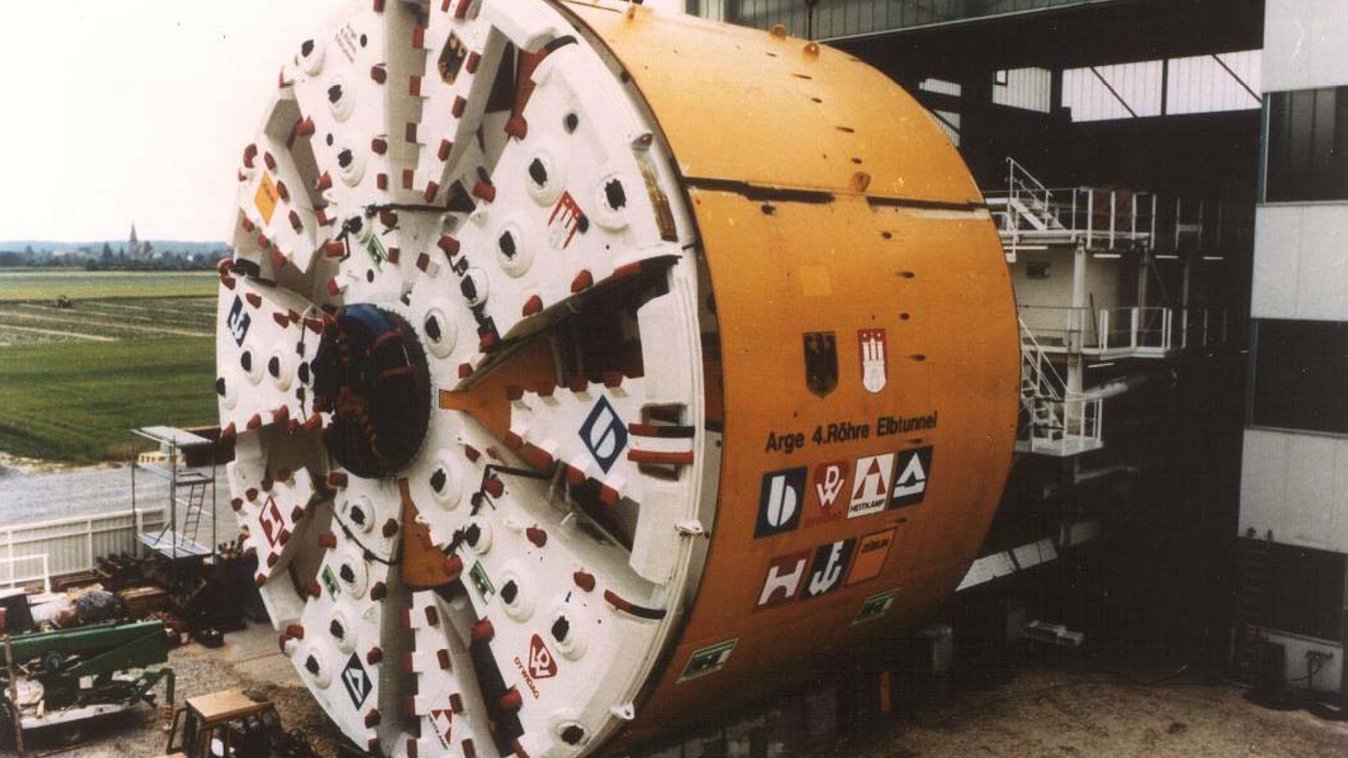
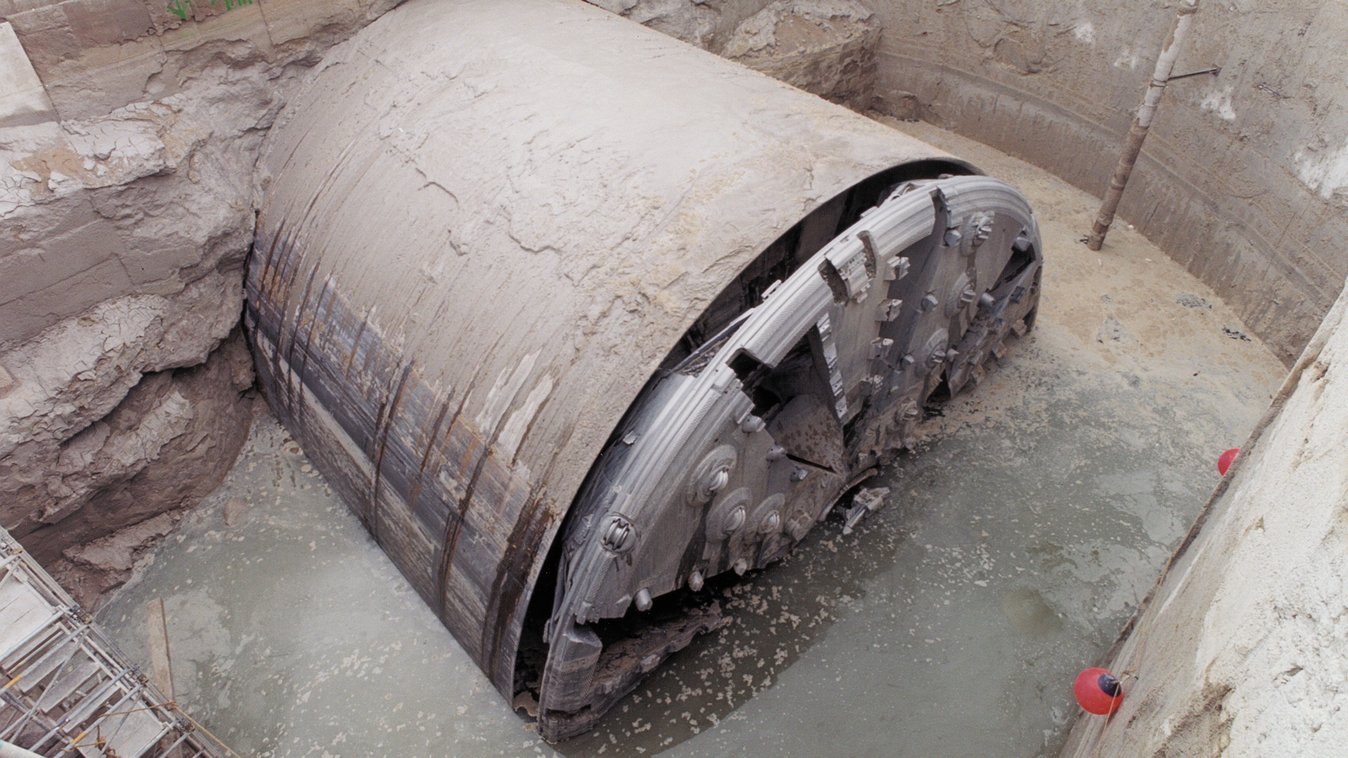
4th tube Elbe tunnel
Short description
A fourth tube was added to the Elbe tunnel in Hamburg due to the increased volume of traffic.
The project
The existing Elbe Tunnel, which opened in 1975 with 3 tubes and 6 lanes, was designed for 70,000 vehicles per day. With up to 140,000 vehicles per day during peak periods, the tunnel’s capacity was exceeded and an extension was required.
In its final operating state, traffic flows exclusively through the 4th Tube from north to south with a very high percentage of heavy load vehicles. For this purpose the traffic envelope allows for two 3.75 m wide lanes, a 2 m wide shoulder and two 0.50 m wide walkways.
Services in detail
ARGE
- Implenia (formerly Bilfinger Berger AG) 15.38 %
- Dyckerhoff and Widmann
- Heitkamp
- Hochtief
- Philipp Holzmann
- Wayss & Freytag
- Züblin
Challenges
The 4th Tube passes under the Elbe with a water depth of about 15 m. For emergency exits, the 4th Tube is connected to the existing tunnel by three 15 to 70 m long emergency tunnels with an inside diameter of 3.50 m. The tunnel lining consists of single-layer reinforced concrete segments with a thickness of 70 cm, an internal diameter of 10.50 m and a length of 2 m. The diameter of the TBM was 14.20 m, making it, at that time, the world's largest tunneling shield machine used in soft ground conditions. Due to the increased weight of the backup construction, the gantries were equipped with walking chassis to reduce the segment loads.
The shield machine was designed for water pressures of up to 5 bar. The cutterhead design allowed boulders of up to 1 m to pass into the cutterhead chamber before being crushed by a hydraulic crusher. Cutterhead tools could be changed from within the spokes of the cutterhead. To reduce torque and contact pressure, the TBM was equipped with a 3 m diameter centre cutter. In order to identify obstacles lying ahead of the face, the TBM allowed for seismic pre-investigation which was integrated in the cutting wheel and visualised in the operator’s control cabin.
Sustainability
The production and storage of the segments required the provision of a larger area. For this purpose, a production area of around 20,000 m², 9,000 m² of which was covered, was leased near the tunnel access shaft. From here, the finished segments could be loaded onto rail wagons and transported directly to the shaft via the existing siding. This location was ideal, as the concrete aggregates, for example, could also be transported by ship.
Further information
The 4th Elbe Tunnel tube - from the first Elbe ferries to the high-tech tunnel