Sustainable wooden construction
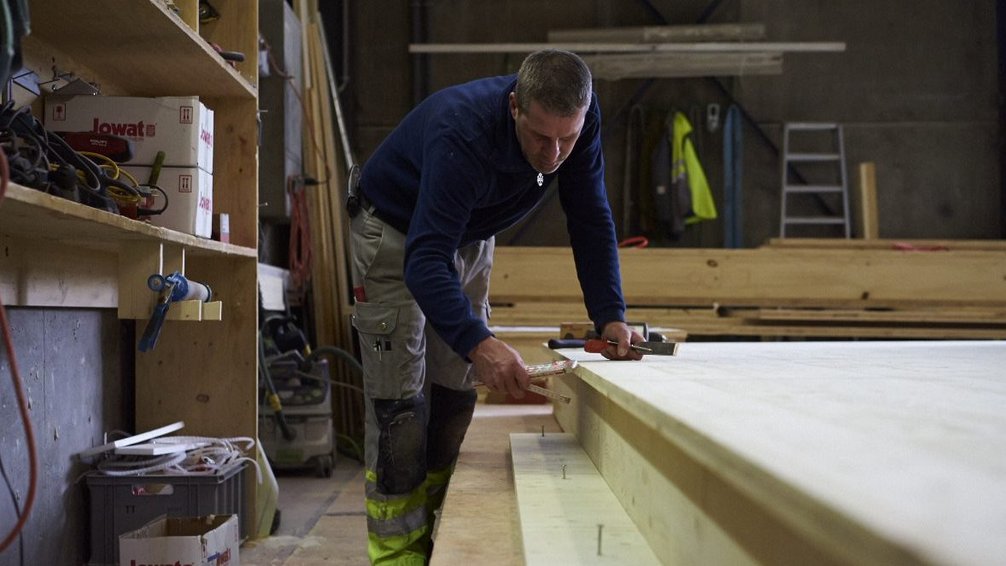
What do the spectacular new elephant house at Zurich Zoo and Switzerland’s largest green residential development in Mellingen have in common? That’s right: wood, which plays a major role in both of these architectural milestone projects. The self-supporting roof of the elephant house is 86 meters in diameter and seems to float above the habitat. It’s made of a huge framework of wooden panels consisting of thousands of individual components. Meanwhile, the sustainable residential complex in Mellingen, commissioned by an investment group within the Credit Suisse Investment Foundation, uses timber for the facade structures and for the laminated boards in the ceilings. The striking facades are made of pre-aged spruce shingles.
The other thing that the two projects have in common is that they were both very demanding to build, but that Implenia nevertheless managed to complete them both on schedule. The first terraced house in Mellingen was finished in October 2012 and now the entire development is ready, offering homes for 400 people. The freshly laid lawns and new shrubs are beginning to sprout in the open spaces, and the first tenants have moved in. On this three hectare site Implenia has created a natural living environment with a peaceful, almost village-like feel. In doing so the company has set new standards of sustainability in several respects (see right column). For example, the development generates all of its own heating. Electricity for the heat pumps comes from 1800 solar panels fitted on 15 rooftops.
As well as environmental aspects, the creators of Neugrüen put a lot of thought into social matters. The buildings are set out in a way that allows residents to live together harmoniously. The layout of the terraces and apartment blocks creates a dense network of lanes, private gardens, places to meet and public squares. It’s an ideal place for walking and cycling. Cars have a place, but they don’t dominate. “It wasn’t always easy to meet all of the demanding requirements relating to the different aspects of sustainability,” says Implenia’s project manager Alexander Arnold. Mastering the construction techniques and logistics proved particularly challenging. “But as a total services provider, Implenia was in a position to coordinate everything efficiently, provide integrated solutions and work cost-effectively.”
In Mellingen concrete and wood are combined cleverly. “Stairwells and lift shafts are made of concrete,” Arnold explains. This ensures protection from fire and earthquake. The ceilings are mainly made of laminated panels, which are then covered with poured concrete to prevent noise disturbance from upstairs neighbours. Although the walls are made of wood, they are boarded and coated with white plaster so the residents don’t feel like they’re living in a clapboard hut. The wood can only be seen from the outside.
Although the wooden shingle facades may make the Neugrüen development look like a mountain village from a distance, modern wooden construction has little in common with the traditional chalet style. Production, based on a digitalised manufacturing chain, was highly rationalised. The wooden frames were built by Implenia’s carpentry shop near Zurich, where they were also fitted with insulation, cable piping, plugholes and plasterboard as required. All that remained to be done on site in Mellingen was to fit the frames together and fix them in place. “Thanks to this modular system, we could put up an apartment block within 14 days,” says Alexander Arnold.
The wood was originally sourced from the Klettgau region on the Swiss-German border. A computer-controlled CNC machine was used to mill and saw raw planks and boards into the desired shapes at Implenia Wooden Construction’s facility in Rümlang. The pieces were put together like a huge jigsaw puzzle at its workshop in Schwerzenbach. Some of the elements were 14 metres long and 3.5 metres wide, and each was individually assembled according to the plan. A team of two carpenters took about half a day to finish a wall or ceiling element. They had to work at speed but with precision, because once the pieces reached the construction site, anything that turned out not to fit would have to be adjusted manually, which would waste time.
Efficient, rationalised production is one of the key reasons for the boom in wooden construction in Switzerland. For a few years now it has been possible to construct wooden buildings up to six storeys high, and wooden facades up to eight storeys. The new 2015 fire safety regulations will further extend the possible applications of wooden construction. Thanks to these improved conditions, this renewable construction material has made a real breakthrough in the construction of residential and office buildings. In just a few years the market share of new apartment blocks made of wood in Switzerland has gone from practically 0 to 5 percent – that’s approximately 300 buildings a year.
“If you’re trying to meet high environmental standards, it’s hard to avoid wood these days,” says Christian Kündig, Head of Implenia Wooden Construction. Wood is a renewable material that can be produced and disposed of without emitting much greenhouse gas. As a rule, therefore, entirely or partly wooden constructions generate 15 to 30 percent less greenhouse gas than conventional brick and concrete structures. Wood is also free from harmful substances and is available locally in sufficient quantities. For all these reasons it plays an important role in meeting the ECO standard. In addition, once wooden elements have reached the end of their useful lives, they can be destroyed and disposed of easily.
With all these advantages it is hardly surprising that the future is looking so bright for wood in the construction industry. “We believe that wooden construction will continue to expand over the coming years,” says Kündig. There is nothing to suggest that costs will get in the way of this trend: “By deciding on the construction technique early on, there are minimal additional costs compared with brick and concrete construction.” If the wood is used properly and prepared carefully, this natural material is also very resistant to the weather. This love affair with wood is likely to last.
IMPLENIA WOODEN CONSTRUCTION
A company with many years of experience. A total of 75 employees and 10 apprentices at two locations near Zurich: Rümlang and Schwerzenbach
Strengths:
- Modular construction
- Free forms
- Conventional wooden construction
- Special formwork
- Exposed shuttering
- Joinery
THE ADVANTAGES OF WOOD
- Renewable and climate friendly
- Locally available with large reserves
- Long-lasting, easy to dispose of
- Short construction time thanks to prefabrication
- Warm appearance and creates pleasant indoor climate
SUSTAINABILITY IN NEUGRÜEN
- Minergie-A: This label shows that over the course of a year, operating the building
requires no energy, a standard that can only be reached using on-site solar energy. - Minergie-ECO: This label guarantees environmentally friendly material. It also
imposes requirements relating to daylight and noise insulation. - Minergie-P: This label indicates low energy consumption. This can be achieved through good thermal insulation and the use of solar energy from intelligent window arrangements.
- Green Property Gold is Credit Suisse’s quality seal for sustainable properties
- Aesthetically pleasing, socially useful architecture