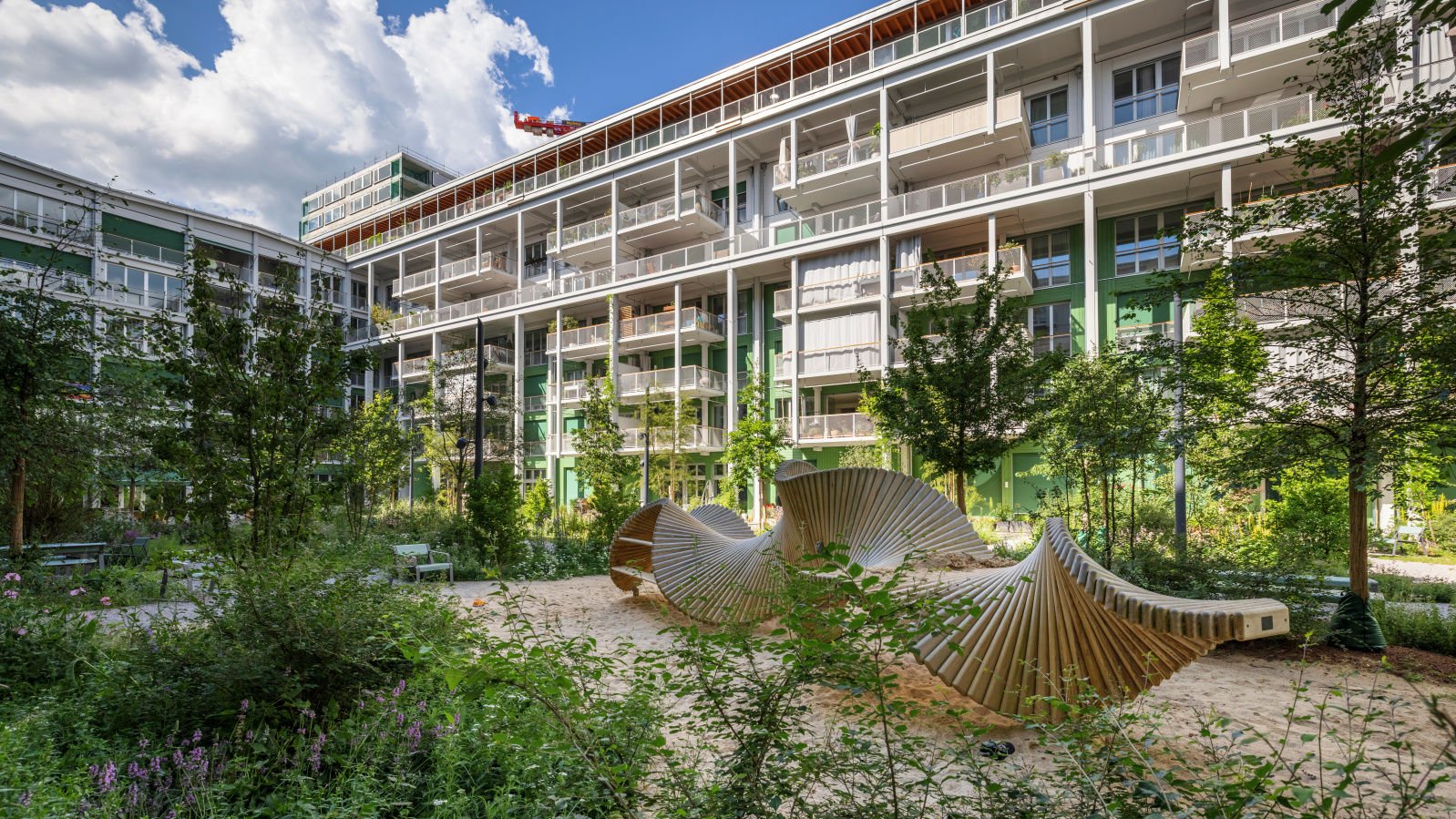
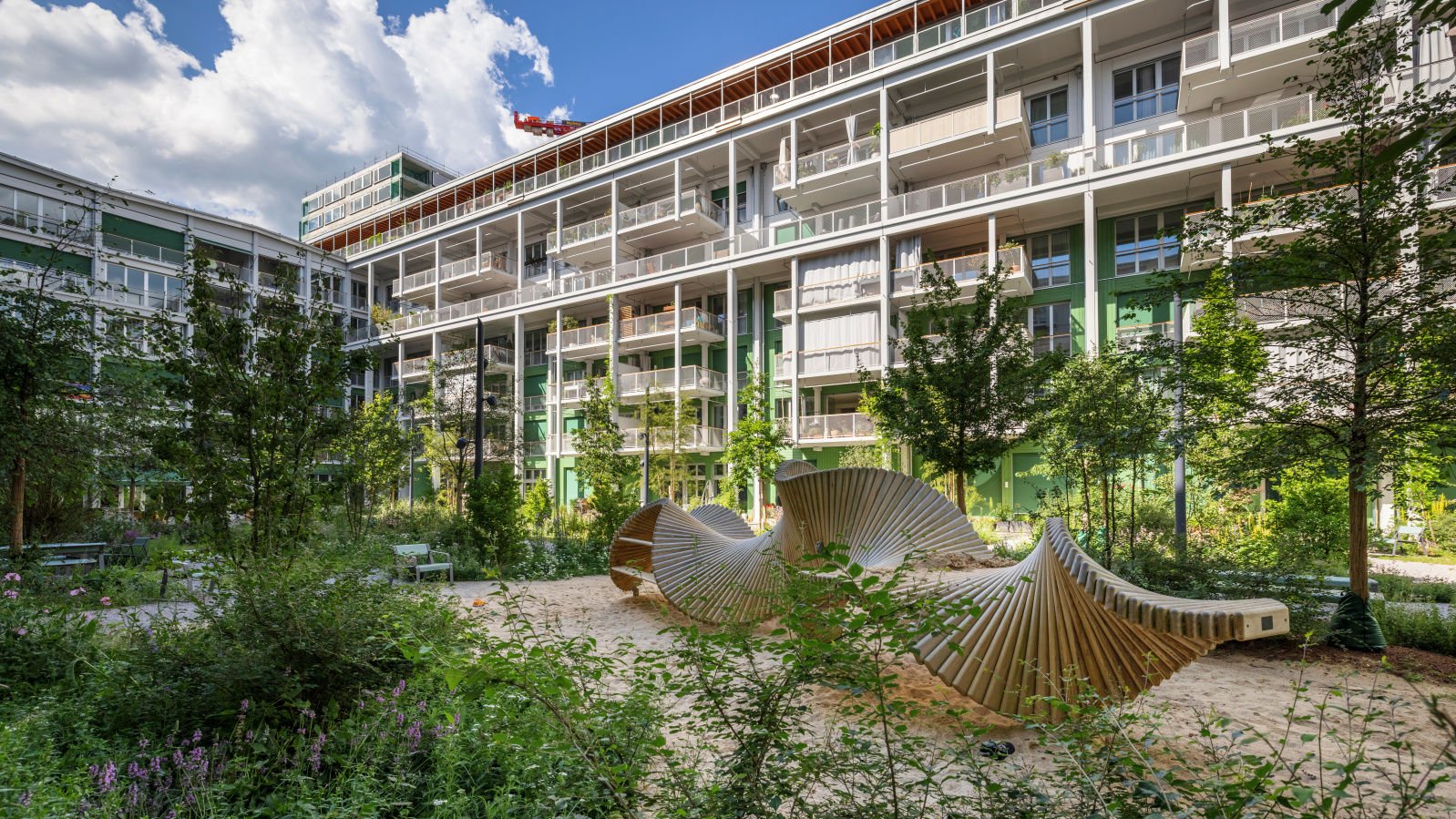
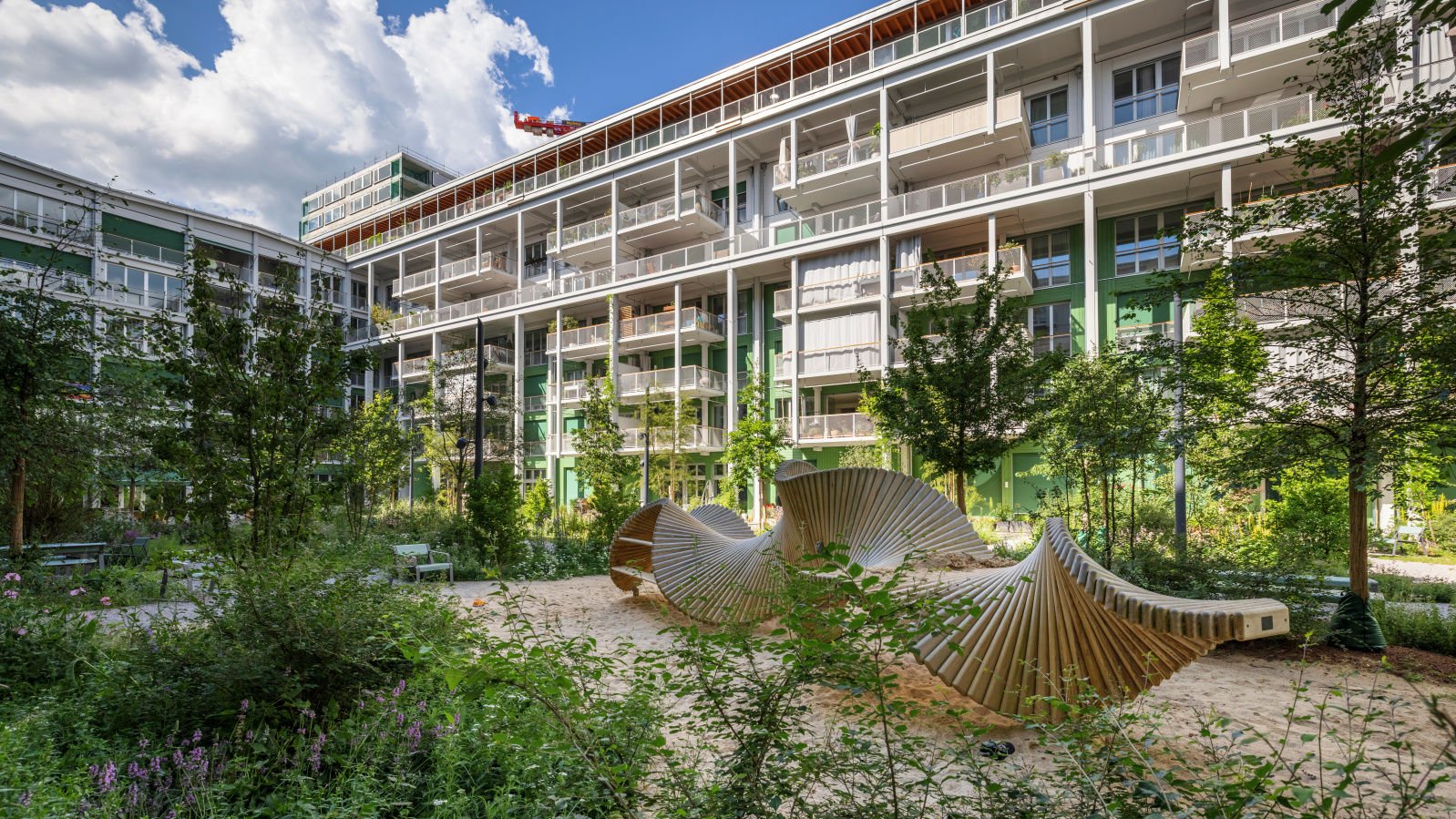
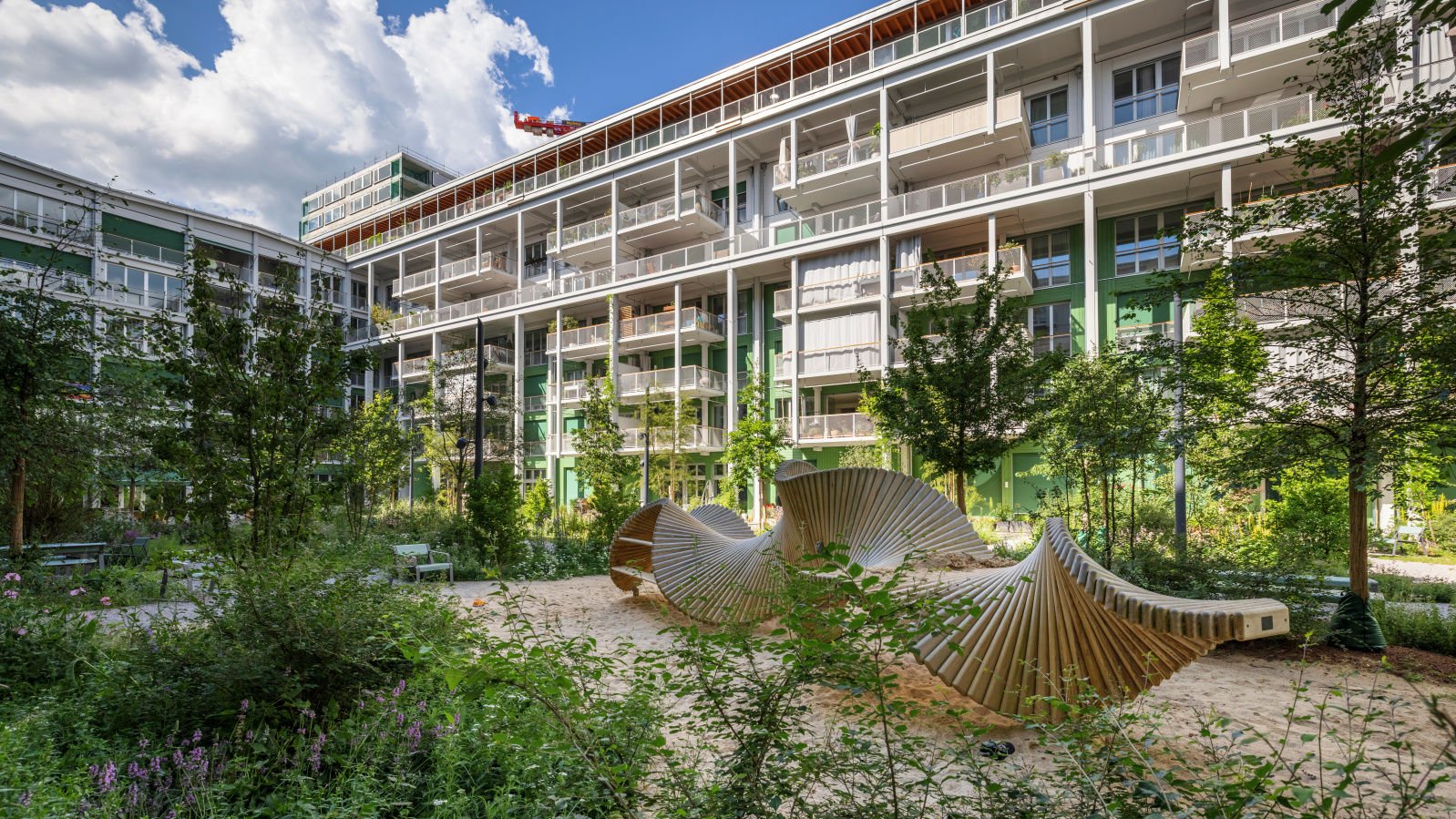
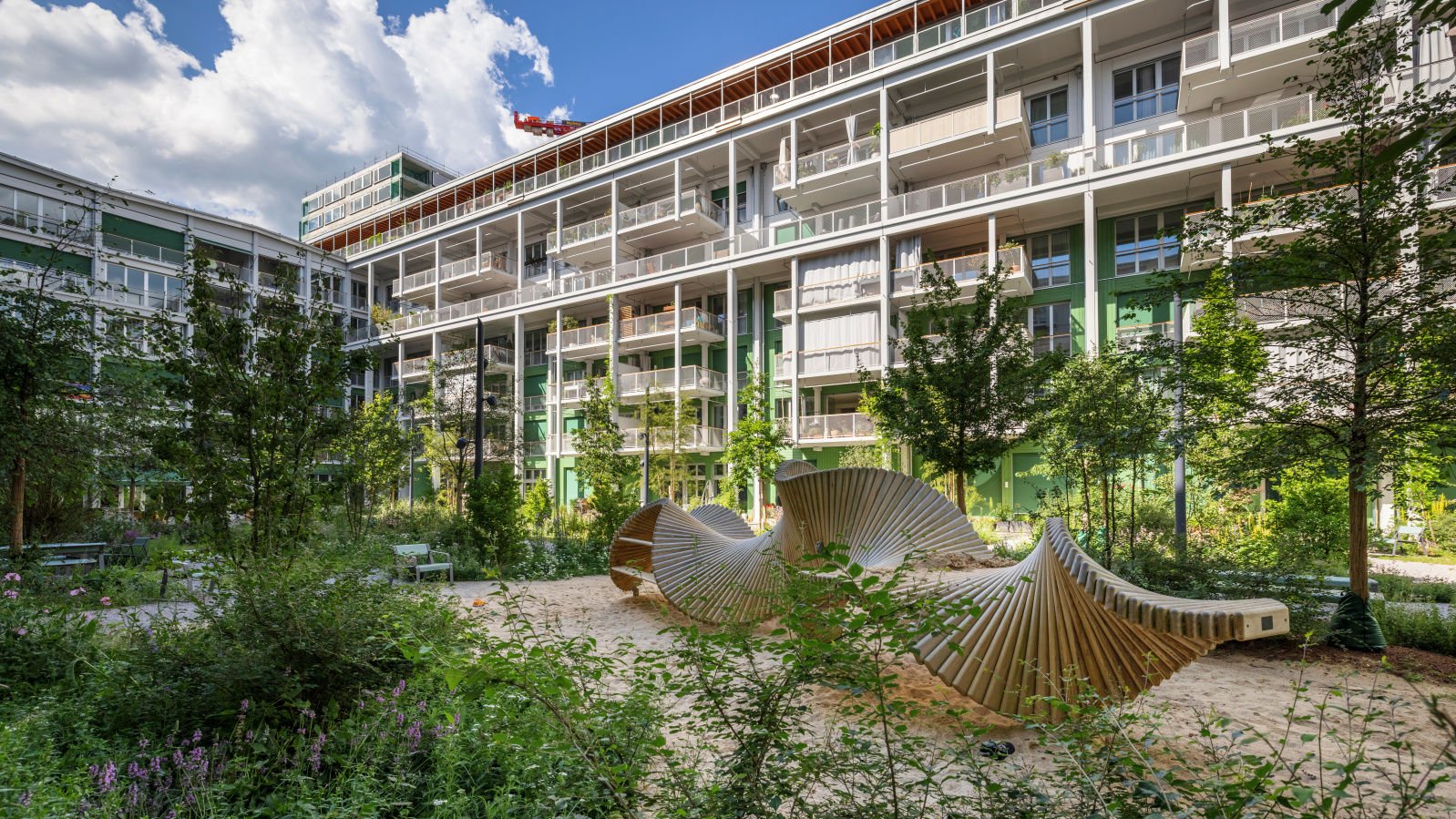
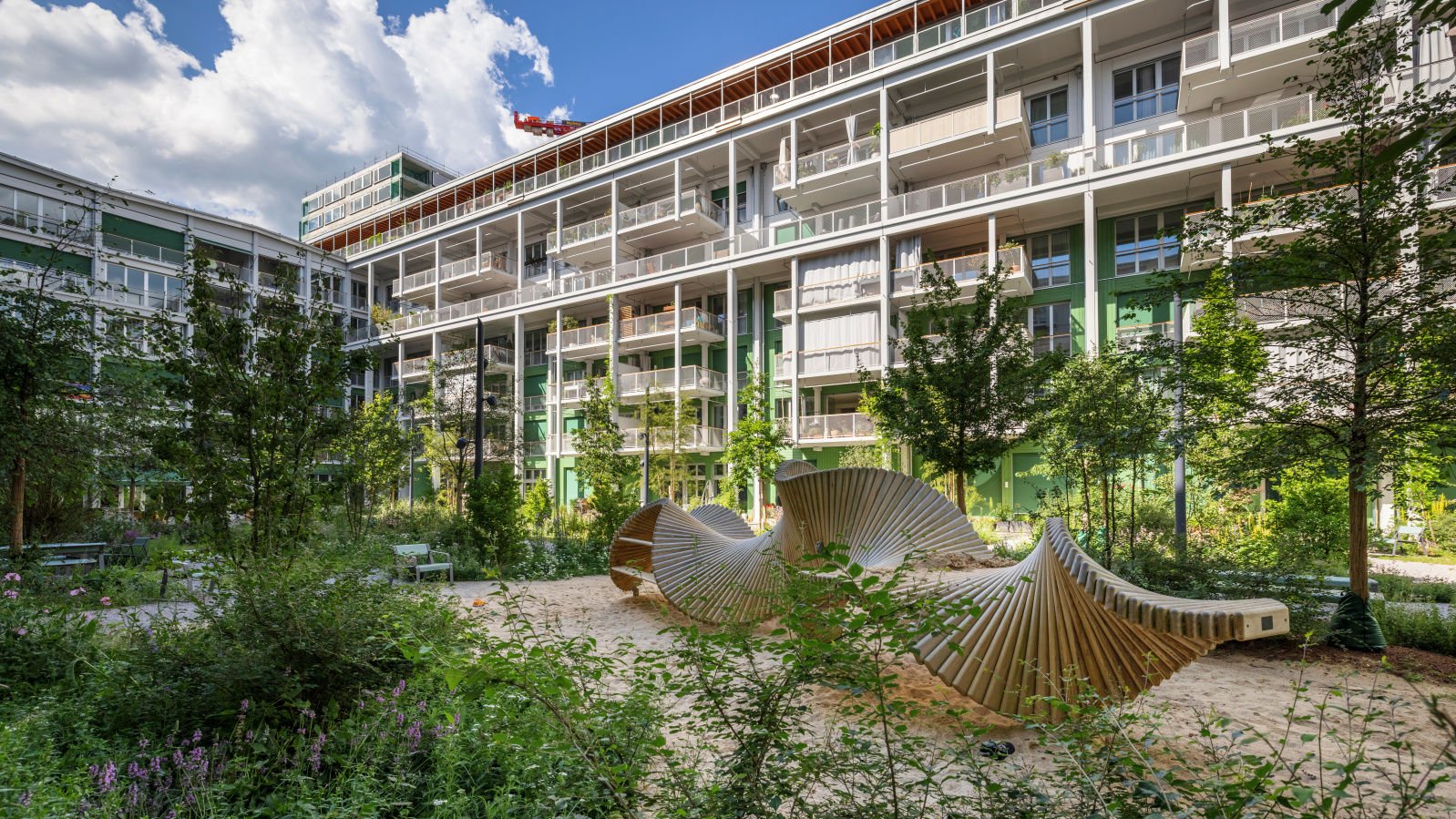
Sustainable construction
Sustainable products and services
Implenia always aims for sustainable solutions when working on building projects. It can do this most effectively when it develops real estate projects on its own land, or when it is commissioned to act as developer. Beyond this, Implenia also requires its business partners to operate sustainably and is actively committed to sustainable construction standards.
Sustainability standards
Many different sustainability standards are applied to building construction. Labels such as LEED, DGNB, SNBS and Minergie set different requirements and focus on different aspects. Implenia Buildings had around 50 building construction projects with sustainability certificates under way in Switzerland and Germany in 2022. This is over two times more than ten years ago. Since 2020, around 15 projects were certified per year. In 2022, Implenia’s Division Buildings generated around 45% of its revenue from certified building construction projects. This percentage has been growing continuously over the past years.
As well as its great experience in implementing sustainability standards, Implenia has also helped develop and harmonise several of them. It worked, for example, as a founding member on the development of the “Swiss Sustainable Construction Standard” (SNBS, see below). One of the goals that Implenia has set itself for 2025 is to develop and build according to the highest sustainability standards, as well as to participate in the further development of these standards.
In 2020 Implenia signed the Swiss Building Label Charter, signalling its support for Switzerland’s efforts to achieve its energy and climate goals. Charter signatories aim to carry out every construction project in accordance with a high energy or sustainability standard while also delivering high quality. These organisations also undertake to install building technology that meets the highest possible energy efficiency standards.
Sustainability standards are still less common in civil engineering than in building construction. In Switzerland, Implenia applies SNBS sustainability criteria when tendering for infrastructure projects. In Norway and Sweden, the company is gaining initial experience with the BREEAM Infrastructure Label (formerly CEEQUAL). The “Hagalund” and “Londonviadukten” projects have achieved very good BREEAM ratings.
Sustainability certificates in building construction
in number of projects in realisation
Sustainable neighbourhoods and urban planning
Towns, communities and private organisations are increasingly designing whole neighbourhoods based on sustainability criteria. Implenia is often involved in the implementation of such projects, and in 2016 it got together with WWF Switzerland to create the “Swiss Association for Sustainable Neighbourhoods”. The association now includes other organisations, including construction companies, public bodies and housing cooperatives. It is responsible for awarding the “SEED next generation living” certificate for pleasant living environments with a high quality of life.
The SEED approach requires the local community and local stakeholders to develop an action plan together based on six sustainability principles. This broad support facilitates the definition of tailor-made, effective measures. The principles concern energy efficiency, CO2 emissions, environmentally friendly and local building materials, circular economy, biodiversity as a feature of landscape design, resident and stakeholder participation, and environmentally friendly mobility.
Alongside the environmental aspects, SEED promotes local business and social mixing. Investors can expect market returns, while tenants benefit from fair rents. This can be achieved by balancing areas that meet different standards within a neighbourhood.
The first SEED neighbourhoods are located in western Switzerland. Implenia is planning a “Green Village” in Geneva's Grand-Saconnex district, for example, on a site belonging to the World Council of Churches, with a hotel, a block of flats and several buildings for international organisations.
Partnership with NNBS
The Netzwerk Nachhaltiges Bauen Schweiz (Swiss Sustainable Construction Network, NNBS) promotes the exchange of knowledge and experiences as well as cooperation between construction specialists in the commercial and public sectors, education, politics and science. Implenia is a founding and funding member of the network, and has had a place on its board since 2012.
NNBS developed the Swiss Sustainable Building Construction Standard (SNBS), which can be applied to almost any type of project. The industry standard takes into account approaches such as the 2000-Watt society and Minergie-ECO. NNBS has also created a practical tool that can be used to evaluate and compare the sustainability of infrastructure projects.
Implenia contributed its expertise to the development of this standard, and uses it regularly on its own construction projects. The energy refurbishment project on the Rue de Lausanne in Geneva received the SNBS Gold certificate in 2022, for example.
Sustainable added value in tenders
If Implenia is mandated to build something for a customer as general or total contractor, the sustainability standards are set by them, not by us. Nevertheless, our experts try wherever possible to introduce sustainability concepts that exceed the original project specifications – and to do so right from the tendering phase.
To this end, Implenia first evaluates the customer’s sustainability strategy and objectives. Our specialists then develop a targeted, customer-oriented sustainability concept and weave this into the construction planning. By applying this approach, Implenia sometimes manages to incorporate sustainability aspects even if the client has not thought about them. A successful example of this was a project we carried out for an international organisation in Geneva. We would like to extend this active approach systematically across the Group by 2025.
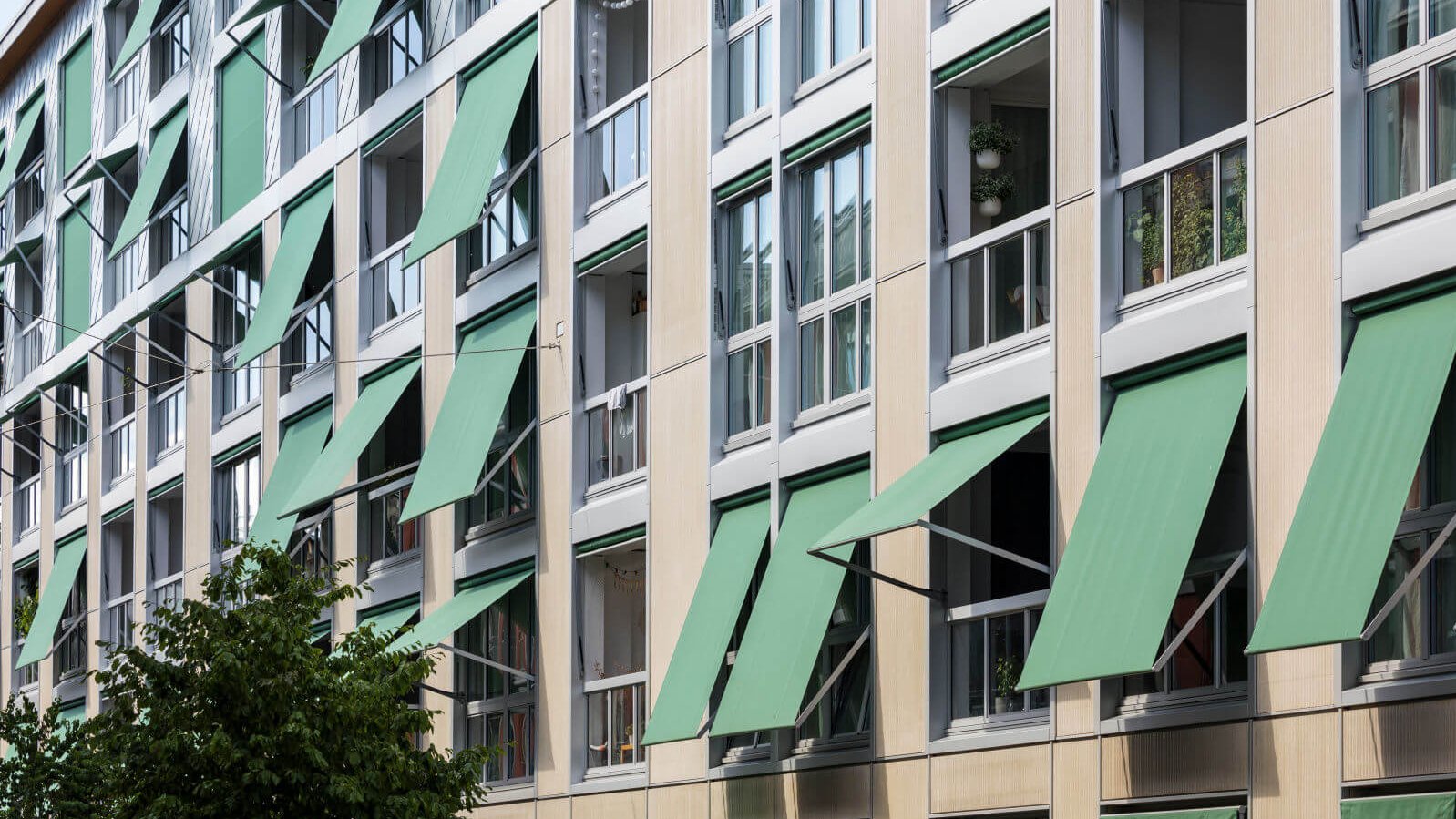
Developing our own projects
Portfolio analysis of development projects of the division Real Estate, Switzerland
Implenia Real Estate analysed the entire portfolio of its more than 40 development projects in Switzerland in 2022 and calculated the carbon footprint. The analysis was carried out on the basis of the “SIA-Effizienzpfad Energie“ (SIA Energy Efficiency Path 2040). With one exception, all the buildings are new-builds, and half of them are wooden or wood-hybrid constructions. There was a particular focus on the use of non-renewable energies and on CO2 emissions. SIA 2040 covers three areas – construction, operation and mobility – taking into account the entire life cycle of a property from its creation to its use, including possible replacement investments during operation, and right through to the end of its life.
Extensive analysis showed that the planned office buildings in the portfolio would meet the SIA 2040 target on average. There is still room for improvement in the residential buildings, however, particularly in terms of the actual structures. The whole portfolio’s CO2 footprint from construction and operation comes to 14.3 kilograms of CO2 per square metre per year. This is 15% higher than the supplementary requirement set out in the SIA efficiency path. Optimisations have been initiated in specific projects in order to reduce greenhouse gas emissions.
Decarbonisation strategy of the division Real Estate, Switzerland
The portfolio analysis has enabled Divsion Real Estate to identify the key levers for decarbonisation and define an ambitious decarbonisation strategy, taking into account the 1.5 degree target of the Paris Climate Agreement.
For all new buildings in Implenia Real Estate's development portfolio, the target is net-zero emissions by 2030. The target for existing buildings is 2050. Emissions from the construction process and materials will be gradually reduced in all new building development projects by 2040. From 2040 at the latest, emissions over the entire life cycle of new construction projects will therefore be at net zero.
According to the defined decarbonisation path, each project is assigned a "carbon budget" at the start of SIA Phase 2, which serves as a limit for further development, construction and operation. This process is accompanied by appropriate monitoring so that relevant optimisation measures can be identified and implemented at an early stage (see example for residential buildings below).
The decarbonisation strategy will present Implenia Real Estate with challenges in terms of design, choice of materials and technical systems. The following applies here: the earlier and more consistently the specifications regarding CO2 emissions are incorporated into the development, the lower the possible additional costs of the project. In the long term, Implenia Real Estate is aiming for regenerative properties that not only produce fewer emissions, but also make a positive ecological and social contribution.
Implenia Real Estate: CO2 limit values for development buildings using the example of residential buildings (new buildings, Switzerland)
in kgCO2/m2a
Sustainable real estate portfolio, Ina Invest
In 2020, Implenia brought approximately half its real estate portfolio to the Swiss stock exchange through property company Ina Invest. Ina Invest’s aim is to have the most sustainable property portfolio in Switzerland (read more). It continues to develop the portfolio in close partnership with Implenia, focusing on the long term and adding new acquisitions.
Minimum environmental standards for materials
Implenia uses a “materials exclusion list” when selecting construction materials to ensure that minimum environmental standards are met. The list is based on the same exclusion criteria as the Swiss Minergie-ECO standard, so if Implenia develops and builds its own projects it can be sure it is not using any materials that are damaging to the environment or people’s health. This list is regularly updated and adapted as new information comes to light.
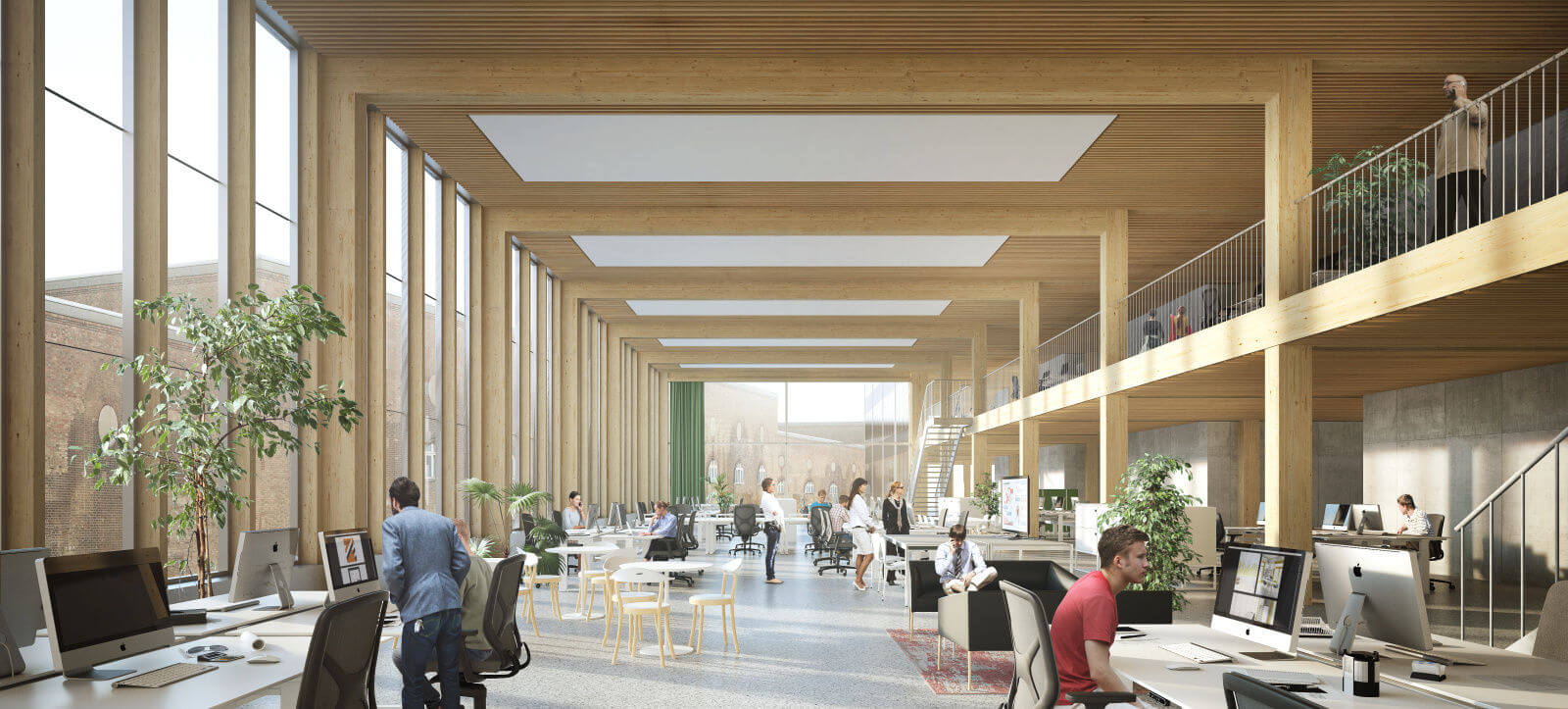
Building with timber
Alongside its conceptual tools, over recent years Implenia has developed extensive expertise in the use of sustainable techniques and materials – especially wooden construction. Thanks to new building methods and its low grey energy content, wood is enjoying a renaissance as a natural construction material.
Government authorities have also recognised the trend. In Switzerland, for example, revised fire protection regulations allow the construction of wooden buildings up to 100 metres high. If the raw material is purchased locally, buildings made of wood cause significantly less greenhouse gas emissions than conventional buildings made of concrete or brick.
As well as being climate-friendly, wood is also an ideal material for prefabricating construction elements. One of the advantages of modular construction is that these elements can be used flexibly and are easy to replace and recycle. All of these benefits make wood an ideal building material within a closed cycle.
In the projects it develops itself, Implenia only uses wood and wooden materials that carry an FSC, PEFC or equivalent label. The company has also helped FSC Switzerland in the past with the implementation of important projects. The FSC standard is still not as widespread in construction as it is in the paper and printing industries.
In order to cope with growing demand in Switzerland, Implenia runs a wooden construction facility in Rümlang, Canton Zurich. Its large production hall can accommodate challenging and complex projects. Each year, around 40,000 square metres of wooden elements and 8,000 cubic metres of construction timber are processed. Implenia uses the offcuts to fuel a central heating system, which also supplies heat to the adjacent yard.
Its execution of pioneering projects has made Implenia one of the leading players in the wooden construction segment in Switzerland.
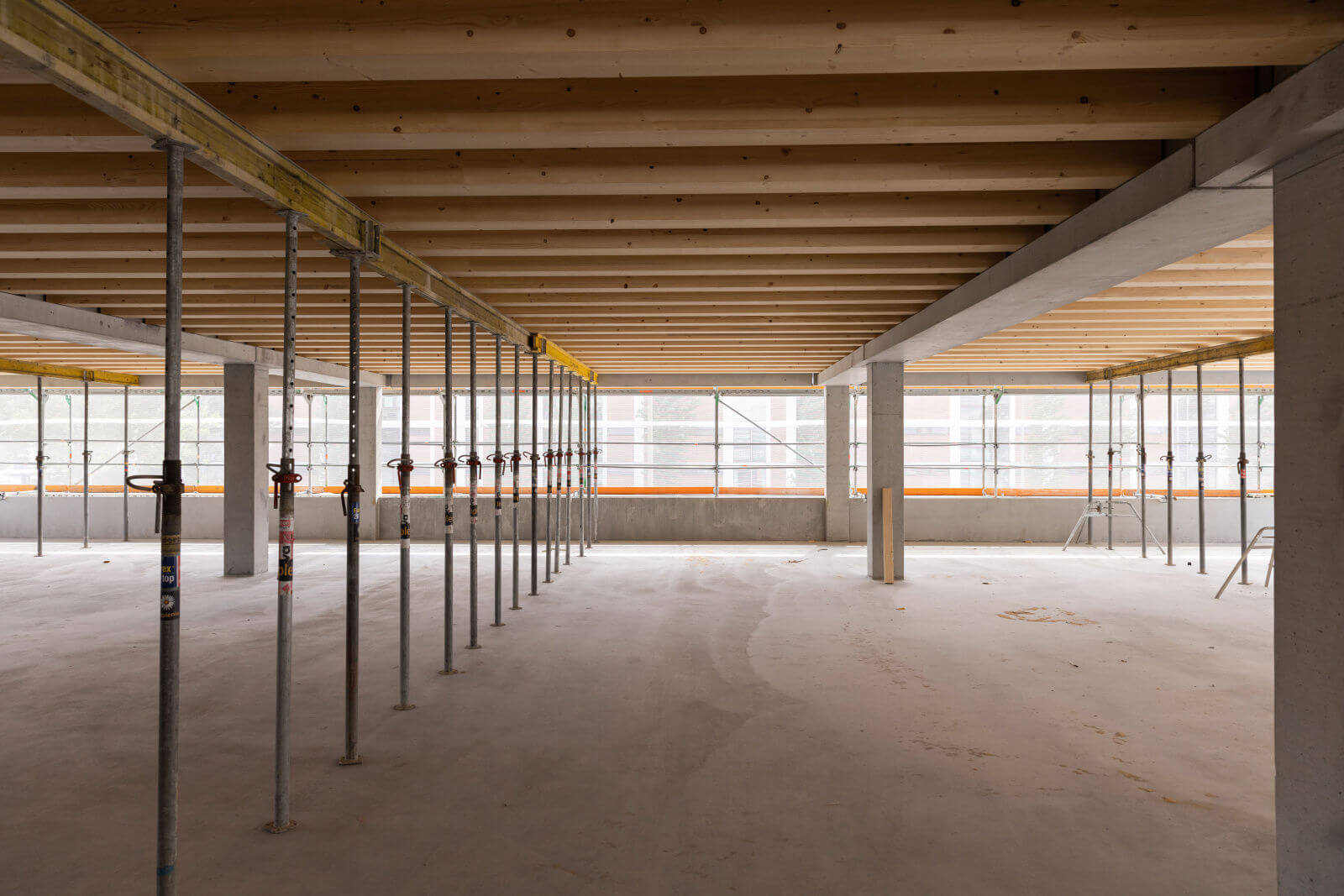
Empa
Implenia is currently building the new Empa campus in Dübendorf, with laboratories, offices, catering facilities and a parking garage. The new buildings are being built to Minergie-P-Eco standards, and a new type of wood-hybrid method is being used for the car park’s supporting structure.
Read more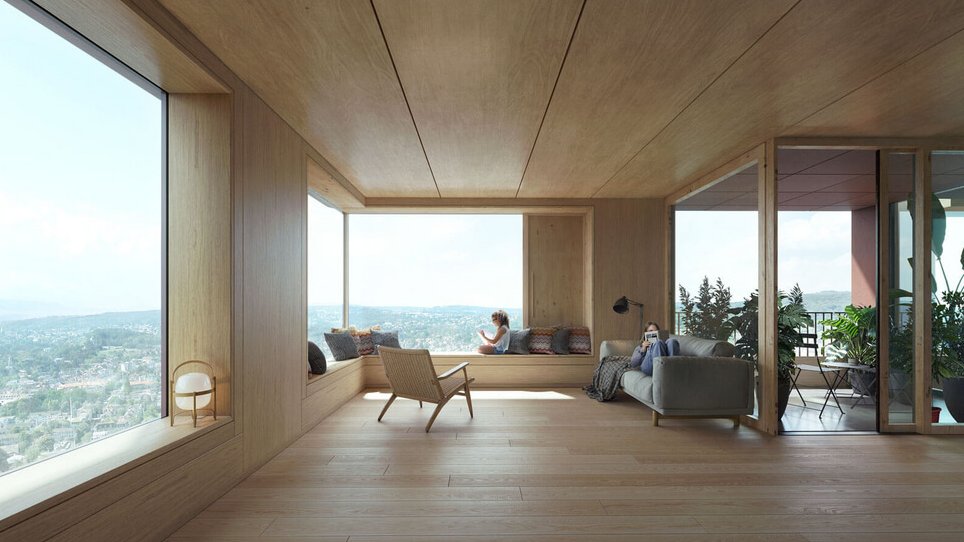
Rocket
The “Rocket” project is another of Implenia’s own developments on the former Sulzer site in the heart of Winterthur. This 100-metre-high skyscraper is being built using a hybrid wood-and-concrete method. When completed in 2026, it will be the world’s tallest hybrid wood building.
Read more
Krokodil
At the Lokstadt development in Winterthur, Implenia has built a wooden high-rise residential building known as “Krokodil”. With 254 apartments, this building, completed at the end of 2020, contains 7,700 cubic metres of wood.
Read more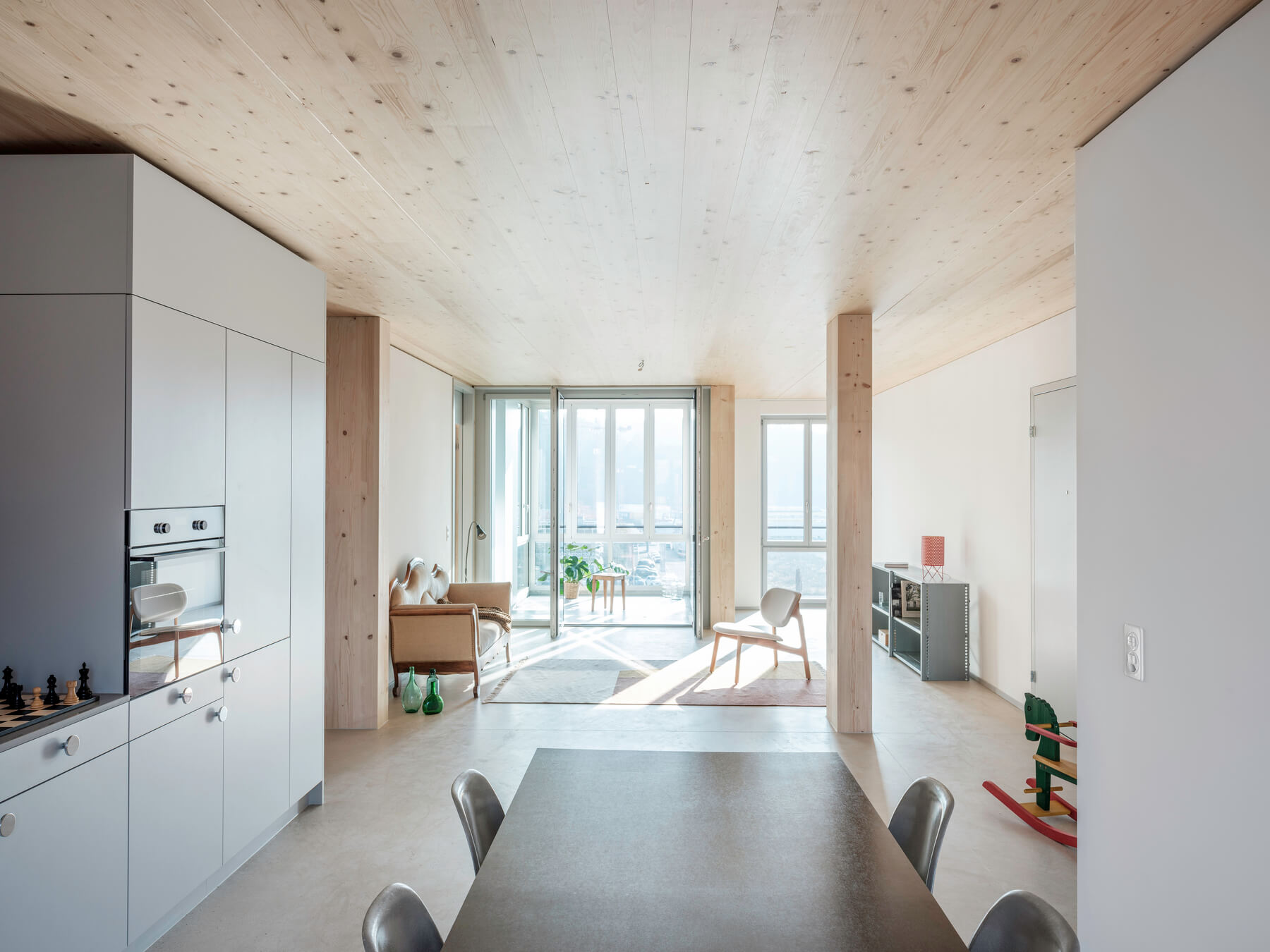
KIM
In April 2022, Implenia completed the residential and commercial building “KIM” which offers a total of 208 apartments. Located in Oberwinterthur, this used 5,500 cubic metres of wood.
Read more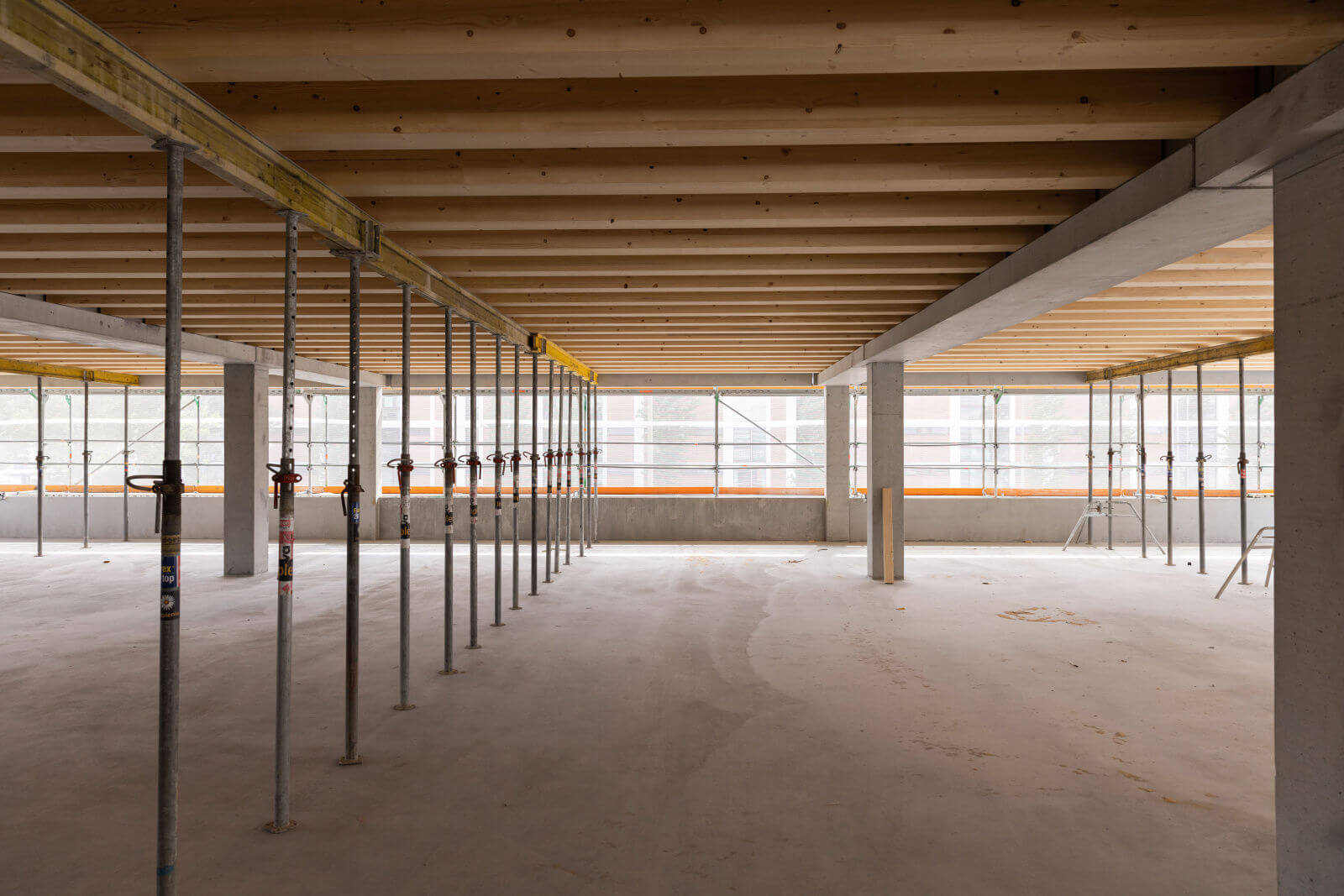
Empa
Implenia is currently building the new Empa campus in Dübendorf, with laboratories, offices, catering facilities and a parking garage. The new buildings are being built to Minergie-P-Eco standards, and a new type of wood-hybrid method is being used for the car park’s supporting structure.
Read more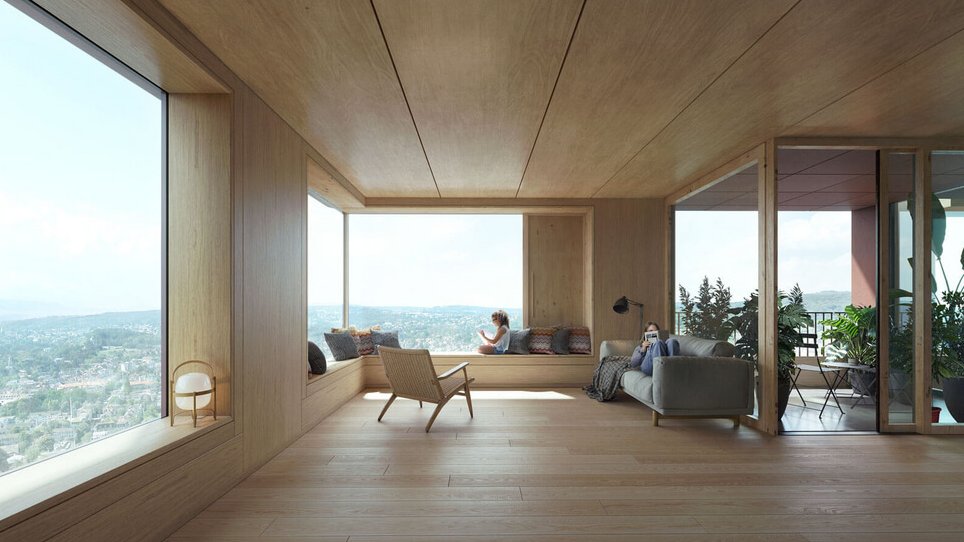
Rocket
The “Rocket” project is another of Implenia’s own developments on the former Sulzer site in the heart of Winterthur. This 100-metre-high skyscraper is being built using a hybrid wood-and-concrete method. When completed in 2026, it will be the world’s tallest hybrid wood building.
Read more
Krokodil
At the Lokstadt development in Winterthur, Implenia has built a wooden high-rise residential building known as “Krokodil”. With 254 apartments, this building, completed at the end of 2020, contains 7,700 cubic metres of wood.
Read more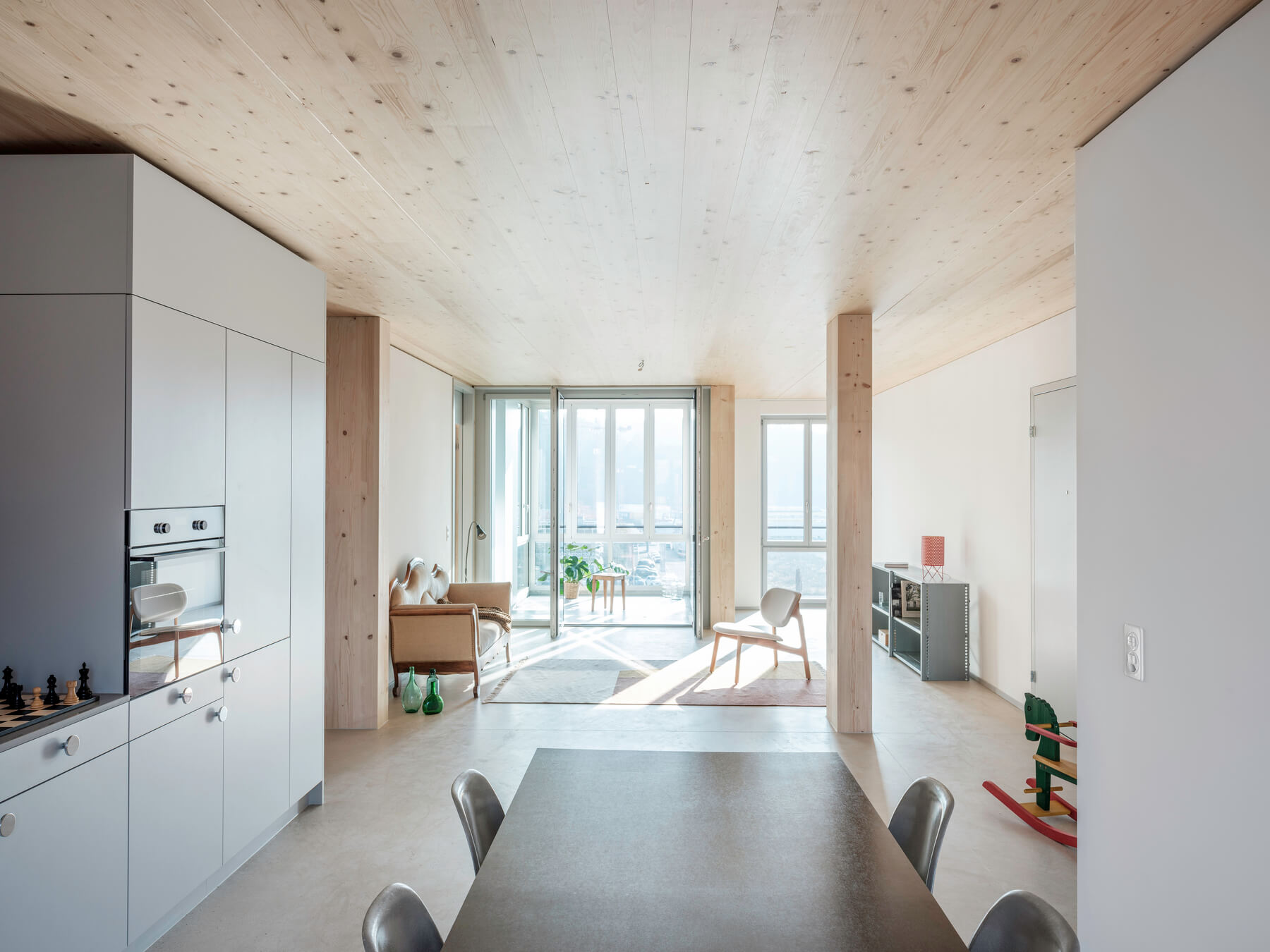
KIM
In April 2022, Implenia completed the residential and commercial building “KIM” which offers a total of 208 apartments. Located in Oberwinterthur, this used 5,500 cubic metres of wood.
Read more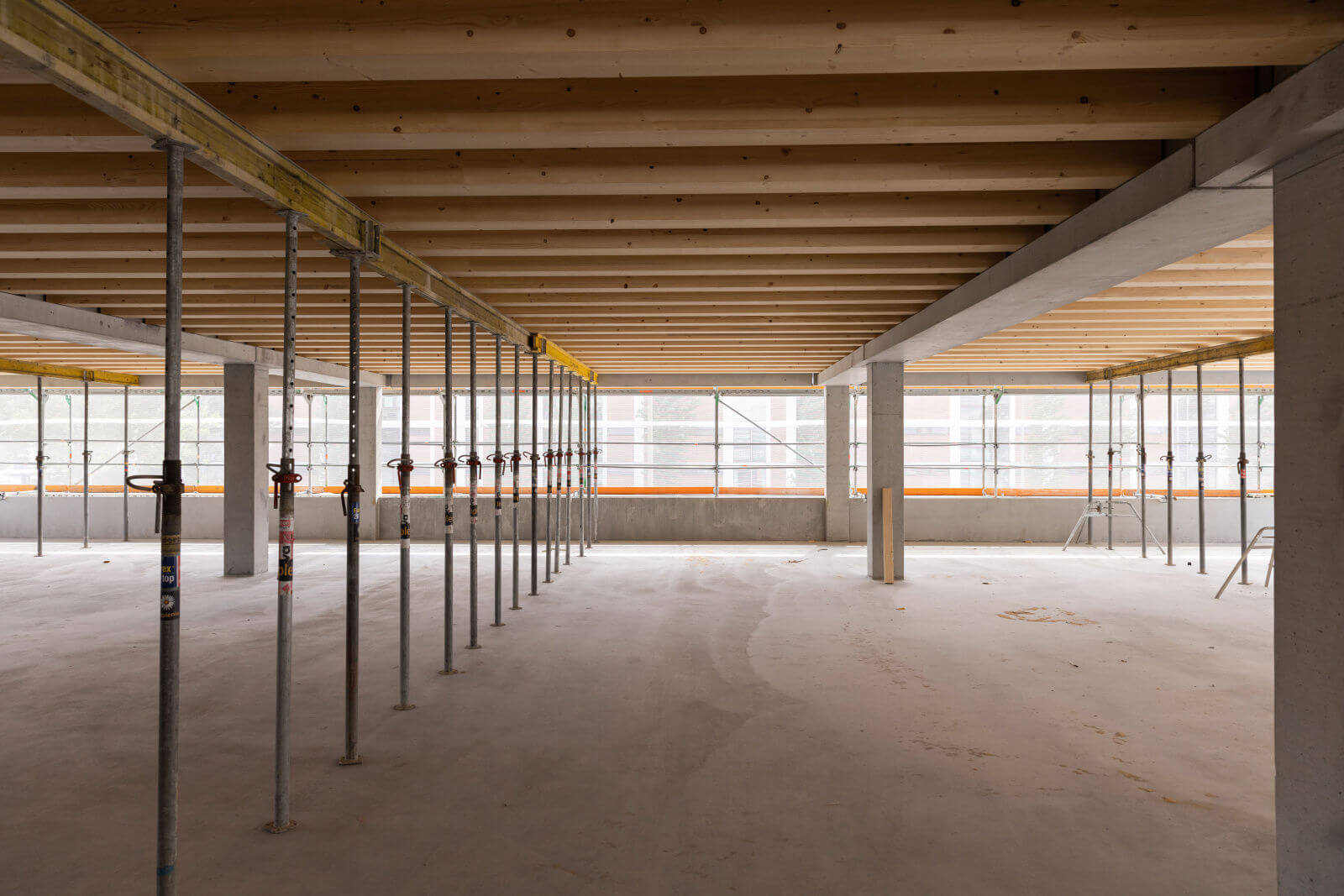
Empa
Implenia is currently building the new Empa campus in Dübendorf, with laboratories, offices, catering facilities and a parking garage. The new buildings are being built to Minergie-P-Eco standards, and a new type of wood-hybrid method is being used for the car park’s supporting structure.
Read more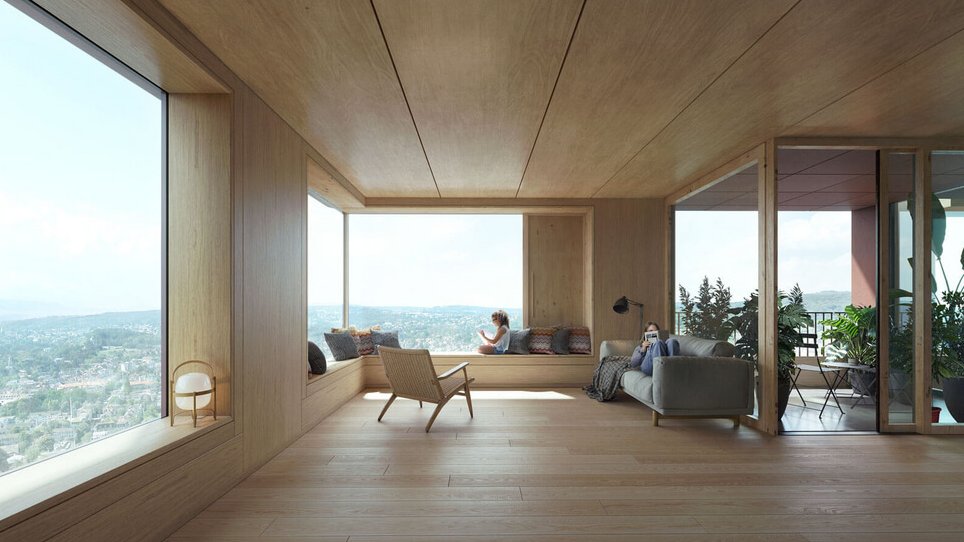
Rocket
The “Rocket” project is another of Implenia’s own developments on the former Sulzer site in the heart of Winterthur. This 100-metre-high skyscraper is being built using a hybrid wood-and-concrete method. When completed in 2026, it will be the world’s tallest hybrid wood building.
Read moreInnovative solutions
GRI 308-2
The construction and real estate industry is changing rapidly and profoundly as a result of ground-breaking insights, new materials, digitalization and technical advances. Implenia is harnessing these changes to the benefit of its customers, employees and shareholders. “Innovation” is therefore one of the company’s four strategic priorities.
Implenia focuses specifically on the following three aspects of innovation:
- Intrapreneurship: Implenia enables its employees and teams to design, test and implement new ideas as part of their work at the company. This is done through a structured process and training.
- Open Innovation: Implenia scouts and tests relevant new technologies and potential solutions that emerge from the innovative environment of start-ups, universities, technology and IT companies. Viable concepts are adopted and applied to Implenia’s projects and business teams.
- Innovation M&A: Implenia invests in, or acquires, innovative SMEs, start-ups and scale-ups that create new business models and sustainable strategic added value.
The company is at the forefront of developing and deploying future technologies in all its core markets, as demonstrated by its wide range of projects – some recently started, some fully complete – and market-ready products. As a rule, these innovations not only offer economic advantages over conventional approaches, but also tend to improve the ecological footprint of construction activities. The slideshow below gives a number of examples.
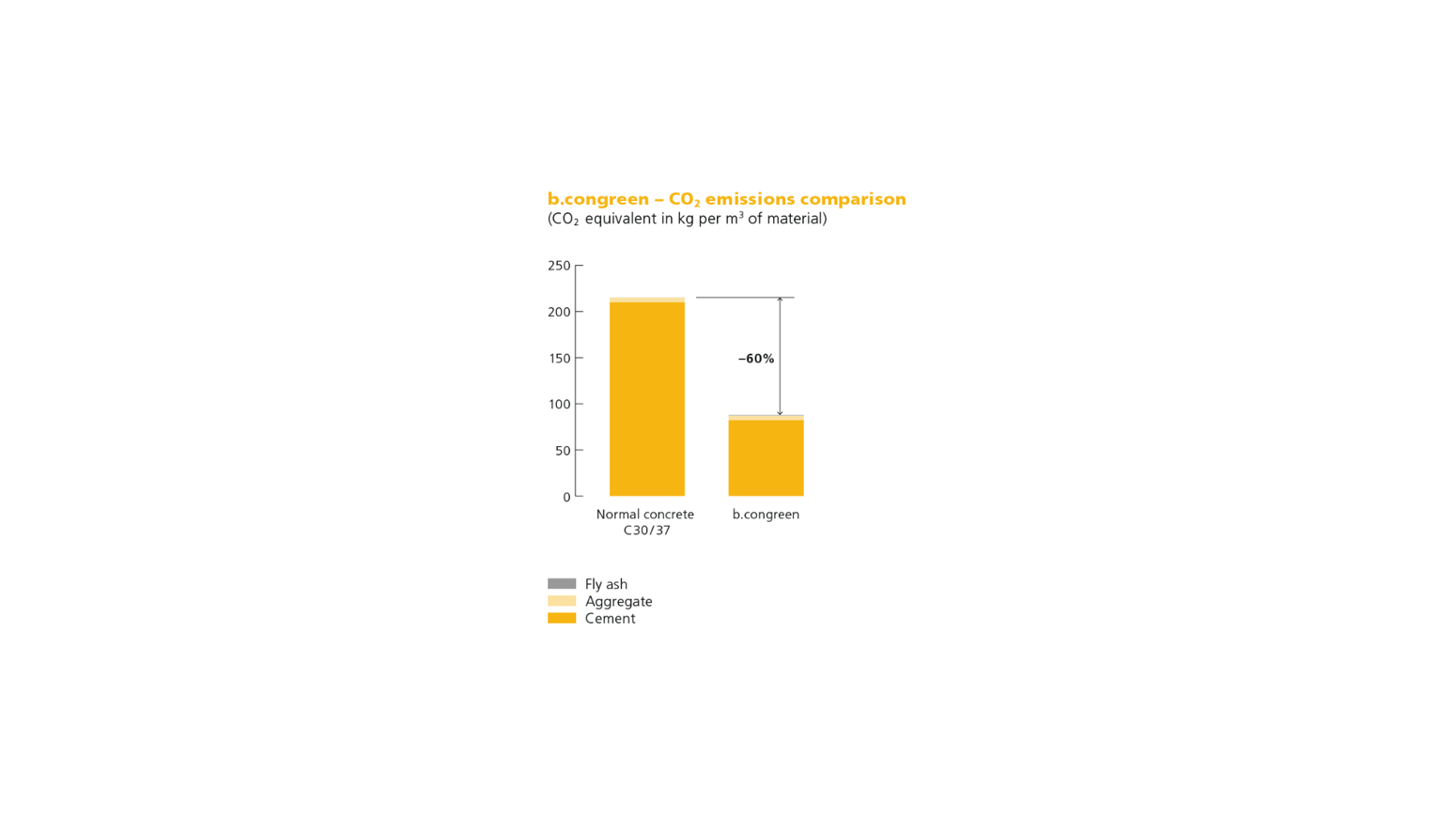
Climate-friendly concrete
The main ingredient of concrete is cement, which is made using a very energy and CO2 intensive process. In recent years, Implenia’s Materials Engineering Department has been developing more sustainable recipes for concrete. One of these is “b.congreen”, in which fly ash sourced from power stations replaces some of the cement. Up to 50% less greenhouse gases are produced during production.
Read more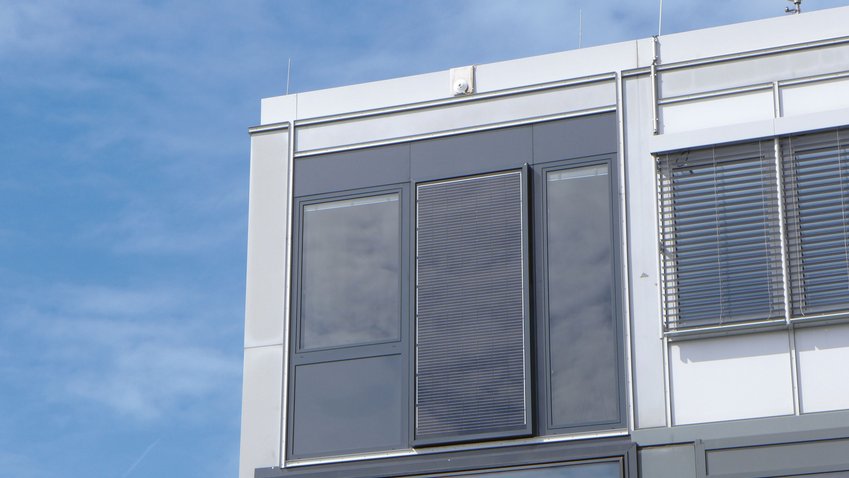
Facades as power generators
In Germany, Implenia Facade Technology is working with the Fraunhofer Institute for Building Physics (IBP) to develop modular facade elements that can supply buildings with energy. As well as electricity-generating photovoltaic modules, these elements include components such as micro-heat pumps, and ventilation systems with heat recovery technology.
Read more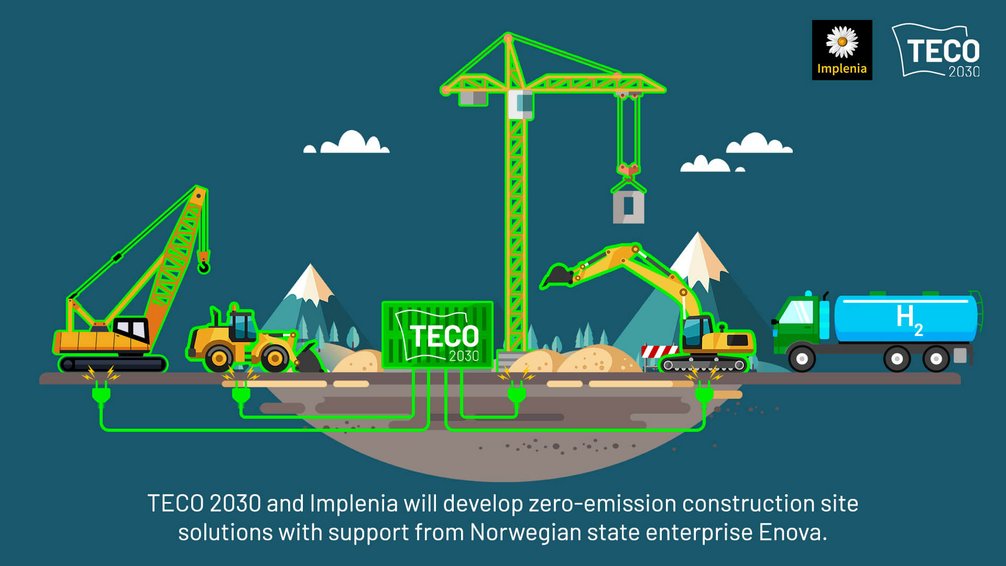
Hydrogen generator
On remote construction sites for roads, tunnels, bridges and other infrastructure, electricity often has to come from diesel generators. As part of a government-backed pilot project, Implenia Norway is currently working with a partner company to find a fossil-free alternative way of providing construction sites with electricity. The company TECO 2030 has developed a fuel cell generator with an output of 0.8 megawatts.
Read more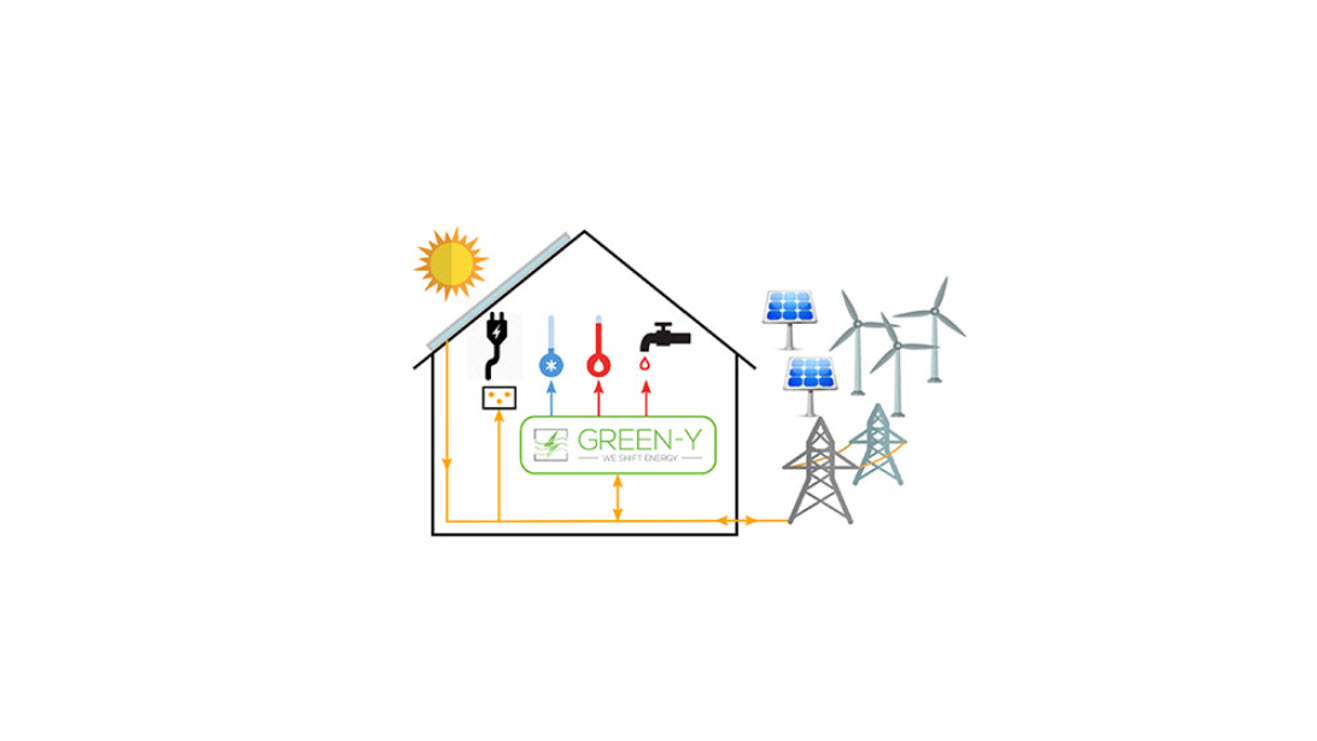
Storing solar power with compressed air
The principle of compressed air storage has been known for some time, but until now there have been no practical systems that would allow it to be used in properties. Implenia was keen to help this sustainable storage technology achieve its breakthrough, so in 2021 it entered into a partnership with Green-Y Energy, which had developed a compressed air storage system for buildings.
Read more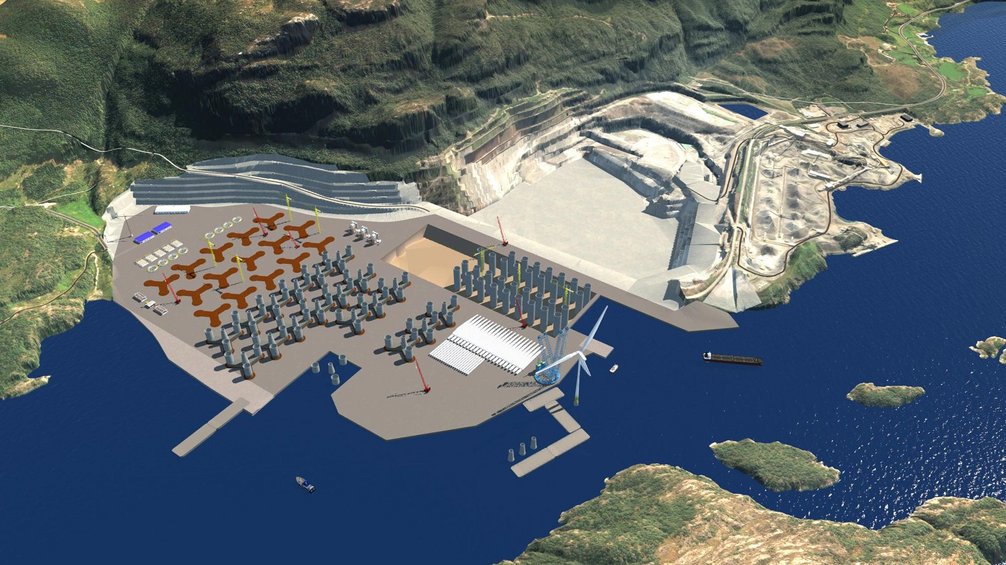
Foundations for floating wind turbines
On the west coast of Norway, Implenia and WindWorks Jelsa, a wind turbine manufacturer, are establishing a joint production facility for floating wind turbines. The construction company is using its expertise to help with the demanding production of various concrete substructures for offshore wind farms.
Read more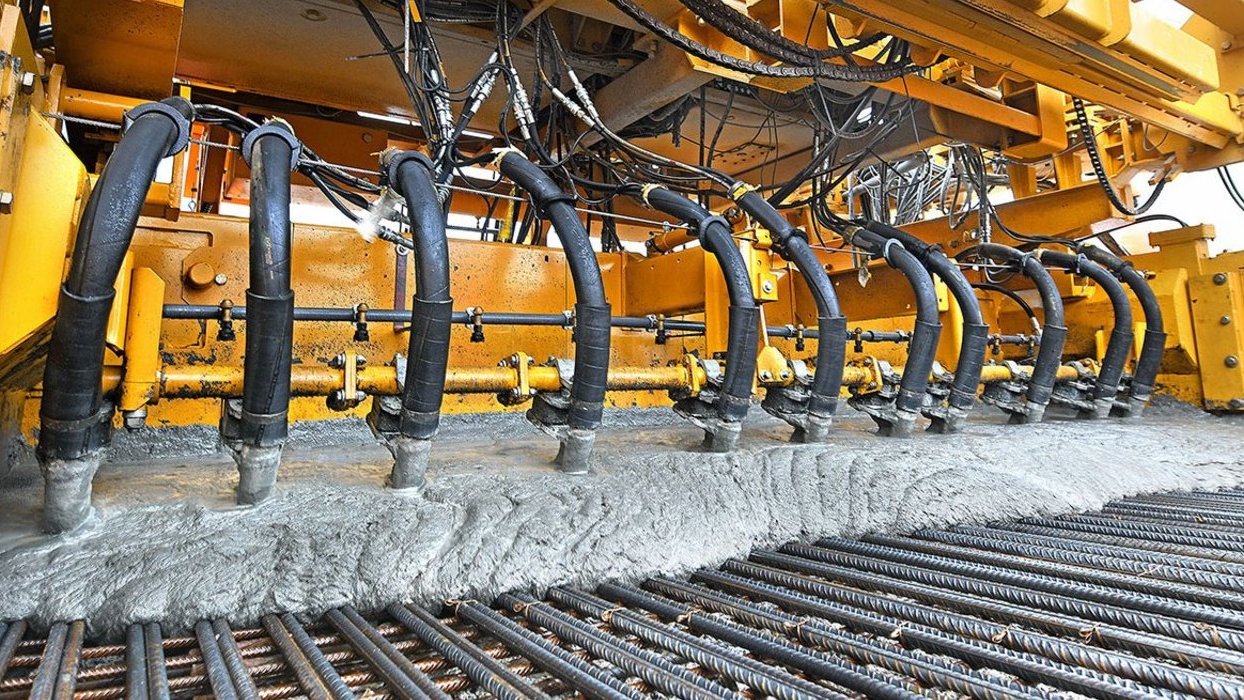
Durable bridges and roads
More and heavier vehicles are using the roads these days, which means that road surfaces have to be repaired at ever shorter intervals. In order to slow the degradation of road surfaces, Implenia and its partners in Switzerland are developing an ultra-high-performance fibre building material (UHFB). This is notable for its enormous longevity.
Read more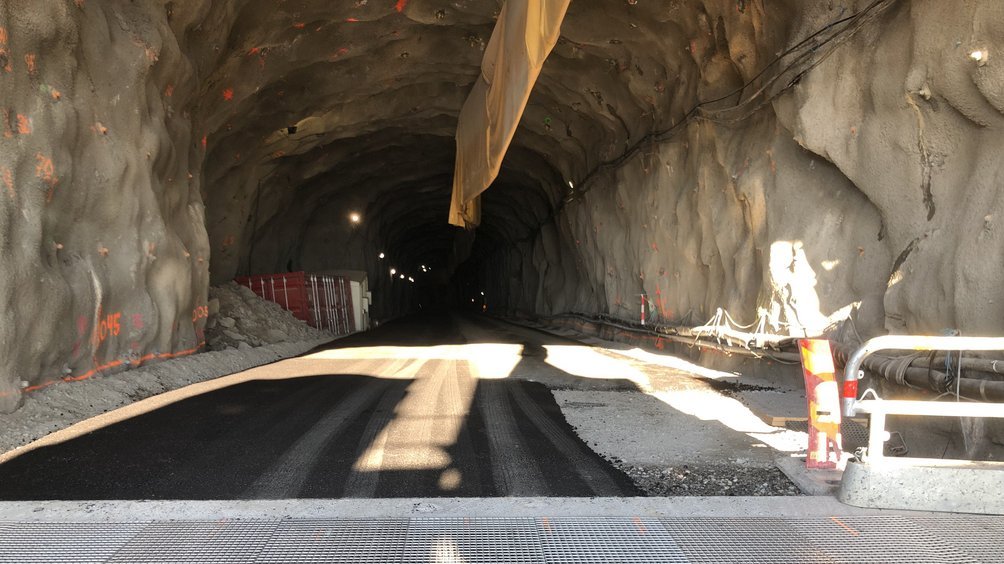
Green asphalt
Implenia Sweden used a special asphalt for its “Londonviadukten” and “Hagalund” projects, reducing the carbon dioxide emissions and energy consumption generated by laying asphalt by almost 70%. This new type of road surface contains a large proportion of recycled materials and a more environmentally friendly binder. It is also produced in a plant powered by fossil-free fuels.
Read more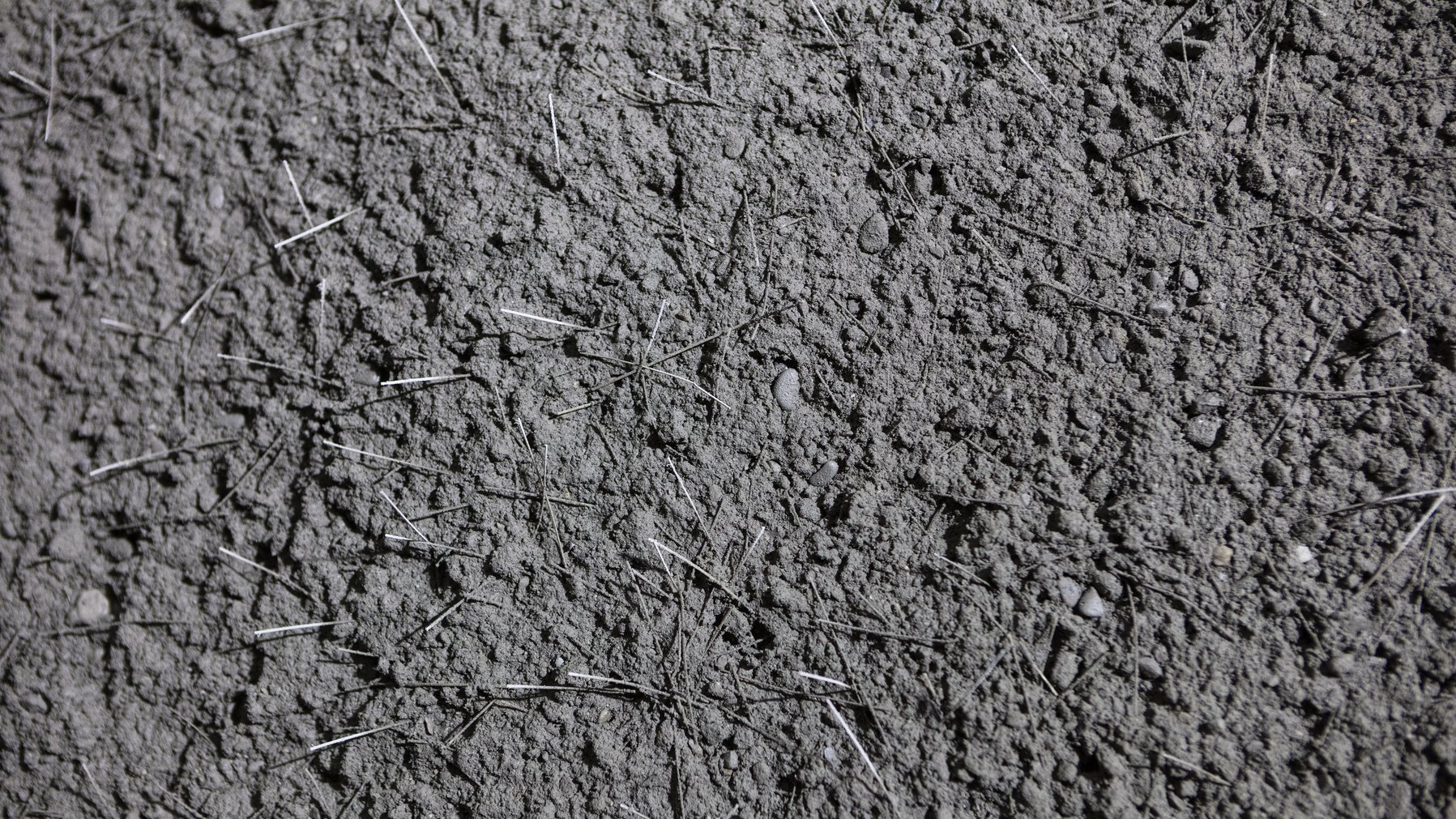
Fibre-reinforced concrete
Building materials scientists are finding more and more ways to reinforce concrete. For example, the Implenia Building Materials Laboratory took part in the “C3 – Carbon Concrete Composite” research project, which tested how bundled carbon fibres could be used to reinforce concrete instead of steel. Carbon fibre concrete is lighter than conventional steel-reinforced concrete, as well as being more tensile and corrosion-resistant.
Read more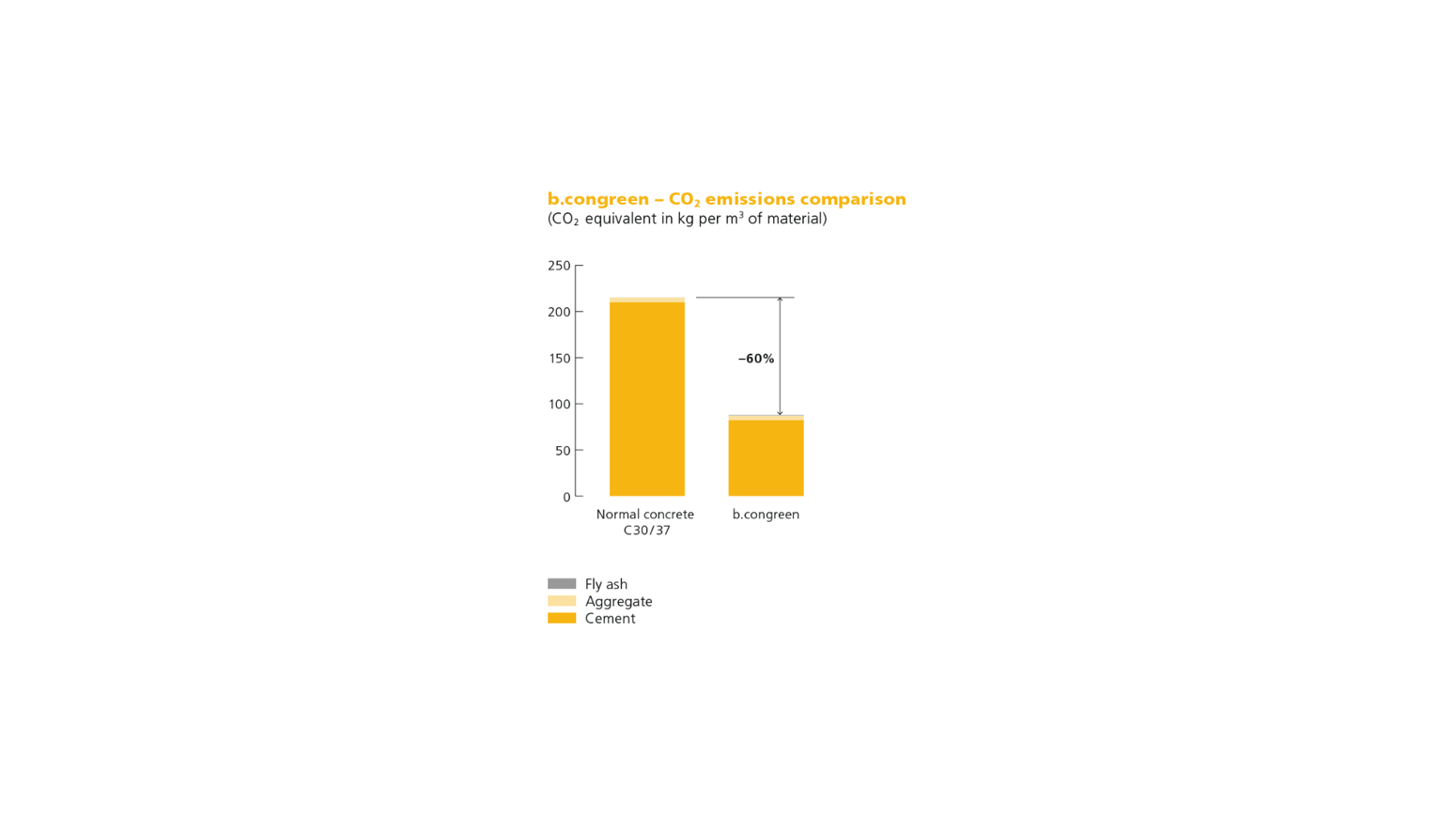
Climate-friendly concrete
The main ingredient of concrete is cement, which is made using a very energy and CO2 intensive process. In recent years, Implenia’s Materials Engineering Department has been developing more sustainable recipes for concrete. One of these is “b.congreen”, in which fly ash sourced from power stations replaces some of the cement. Up to 50% less greenhouse gases are produced during production.
Read more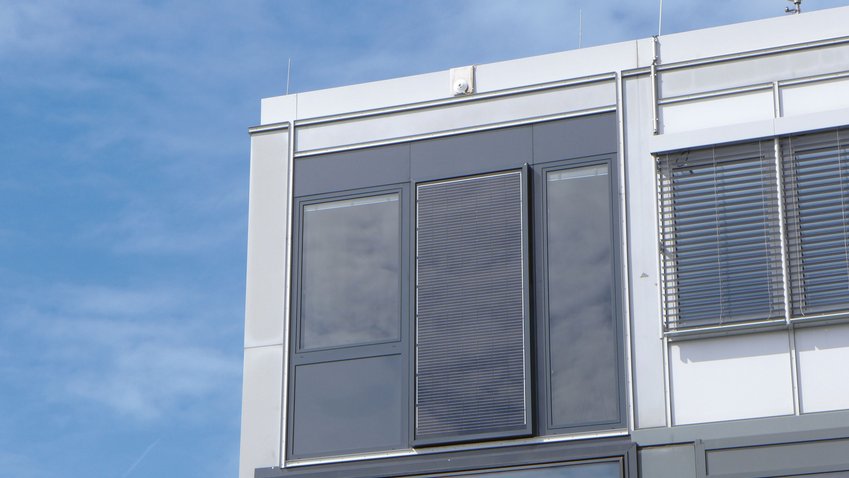
Facades as power generators
In Germany, Implenia Facade Technology is working with the Fraunhofer Institute for Building Physics (IBP) to develop modular facade elements that can supply buildings with energy. As well as electricity-generating photovoltaic modules, these elements include components such as micro-heat pumps, and ventilation systems with heat recovery technology.
Read more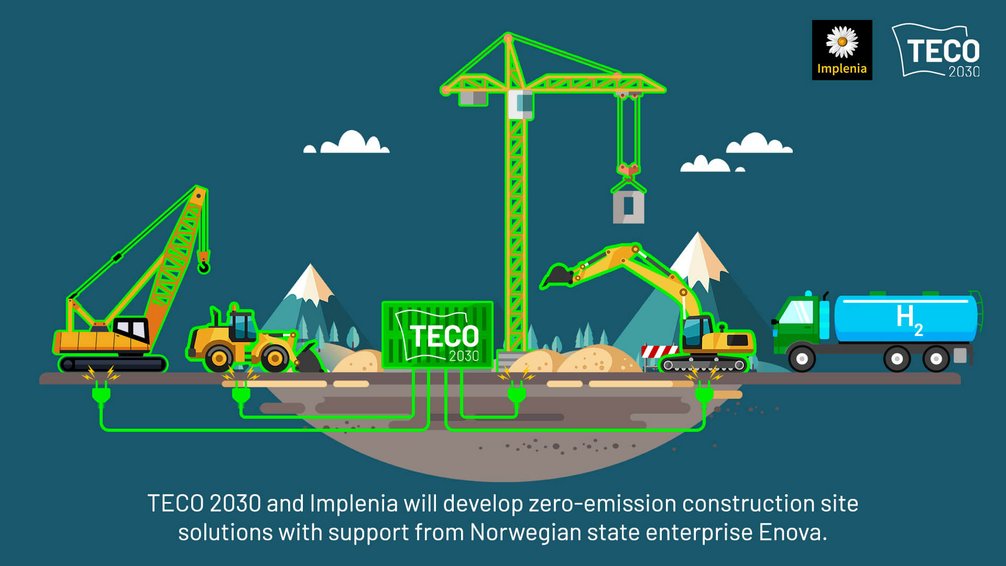
Hydrogen generator
On remote construction sites for roads, tunnels, bridges and other infrastructure, electricity often has to come from diesel generators. As part of a government-backed pilot project, Implenia Norway is currently working with a partner company to find a fossil-free alternative way of providing construction sites with electricity. The company TECO 2030 has developed a fuel cell generator with an output of 0.8 megawatts.
Read more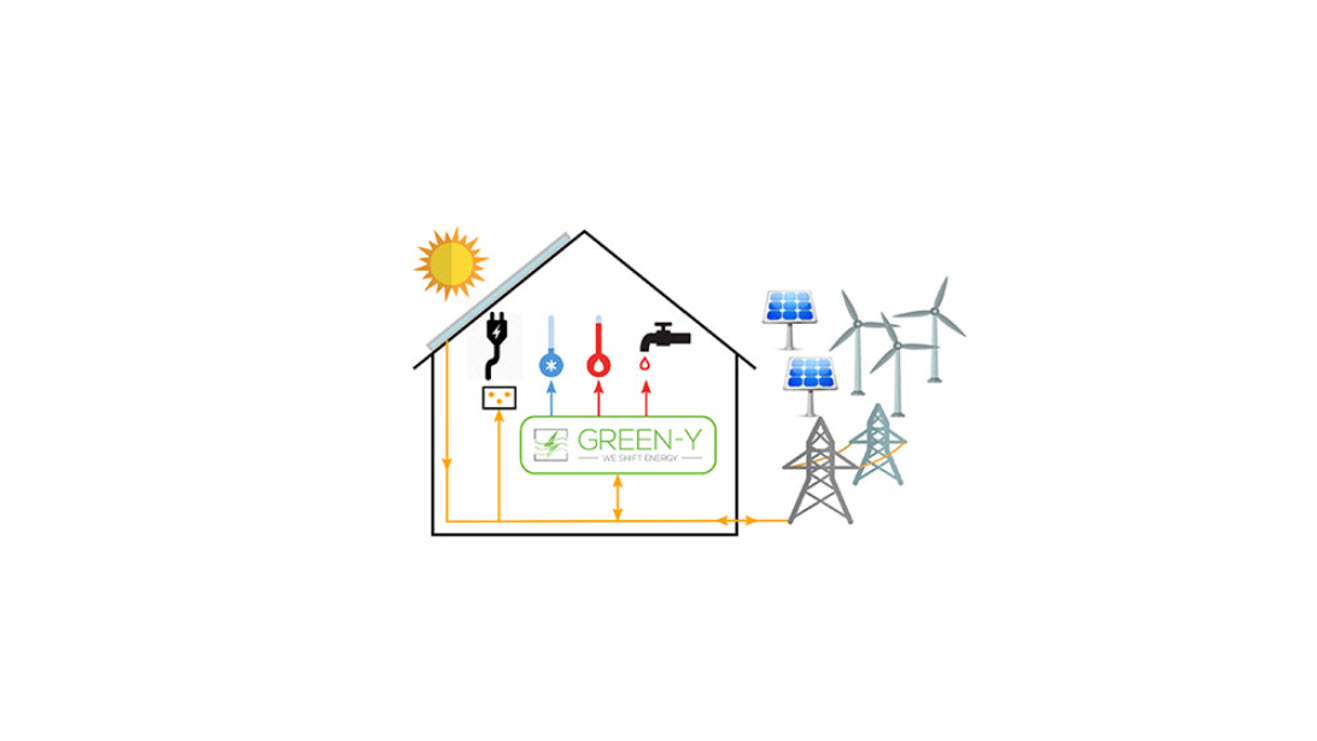
Storing solar power with compressed air
The principle of compressed air storage has been known for some time, but until now there have been no practical systems that would allow it to be used in properties. Implenia was keen to help this sustainable storage technology achieve its breakthrough, so in 2021 it entered into a partnership with Green-Y Energy, which had developed a compressed air storage system for buildings.
Read more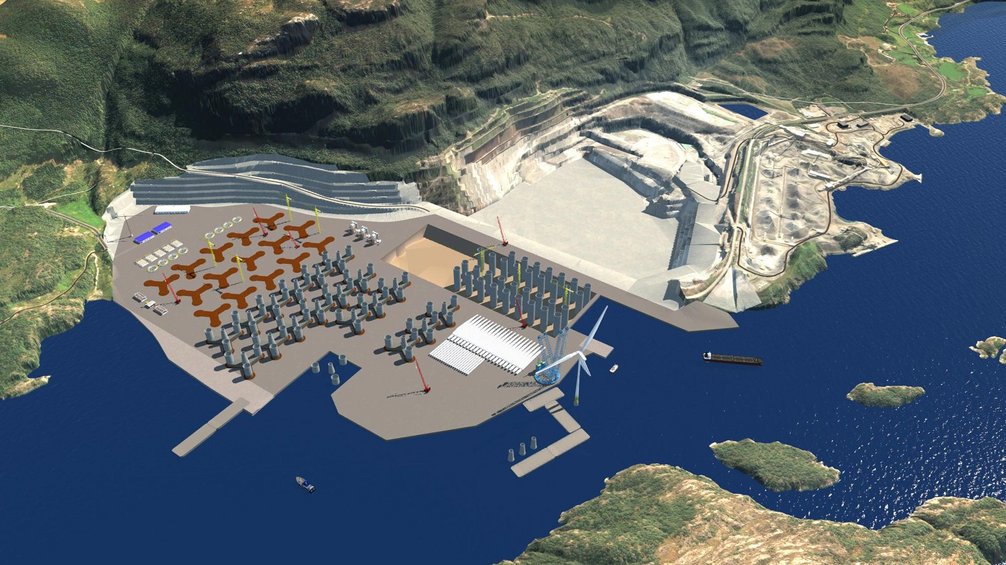
Foundations for floating wind turbines
On the west coast of Norway, Implenia and WindWorks Jelsa, a wind turbine manufacturer, are establishing a joint production facility for floating wind turbines. The construction company is using its expertise to help with the demanding production of various concrete substructures for offshore wind farms.
Read more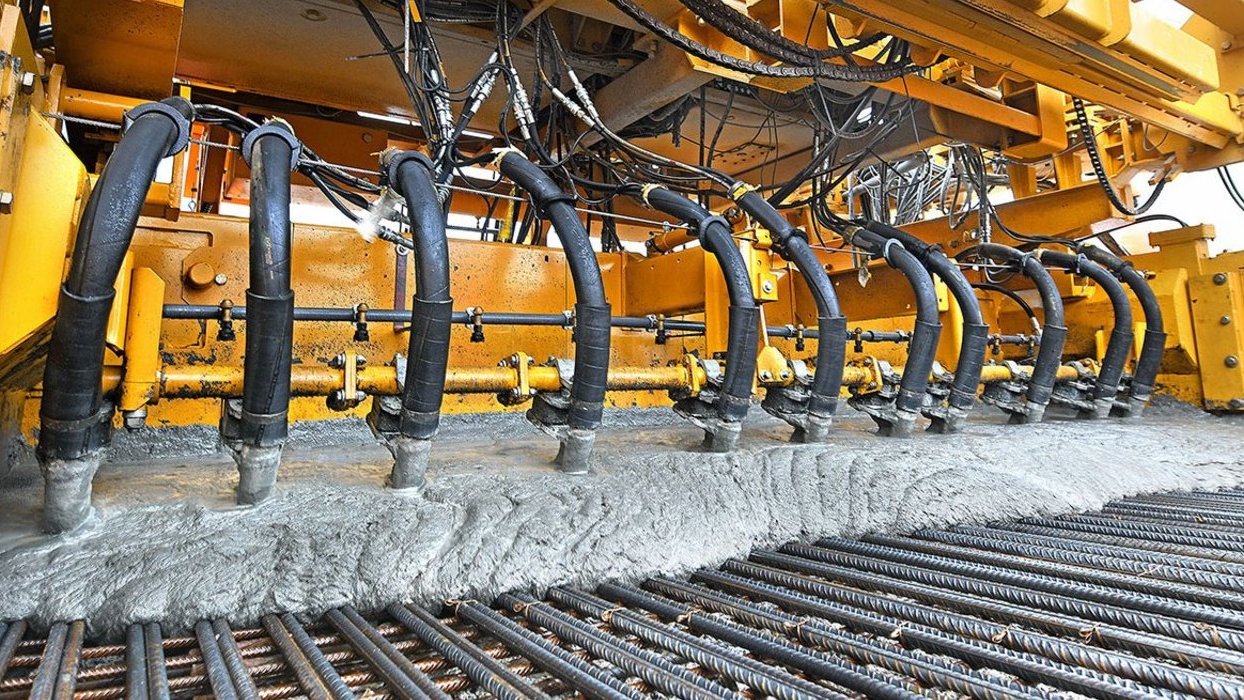
Durable bridges and roads
More and heavier vehicles are using the roads these days, which means that road surfaces have to be repaired at ever shorter intervals. In order to slow the degradation of road surfaces, Implenia and its partners in Switzerland are developing an ultra-high-performance fibre building material (UHFB). This is notable for its enormous longevity.
Read more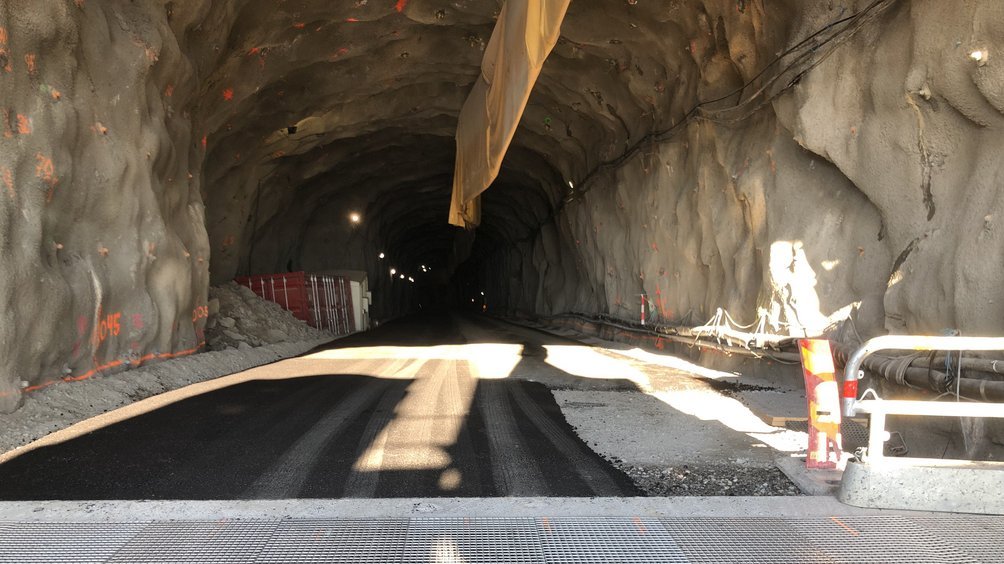
Green asphalt
Implenia Sweden used a special asphalt for its “Londonviadukten” and “Hagalund” projects, reducing the carbon dioxide emissions and energy consumption generated by laying asphalt by almost 70%. This new type of road surface contains a large proportion of recycled materials and a more environmentally friendly binder. It is also produced in a plant powered by fossil-free fuels.
Read more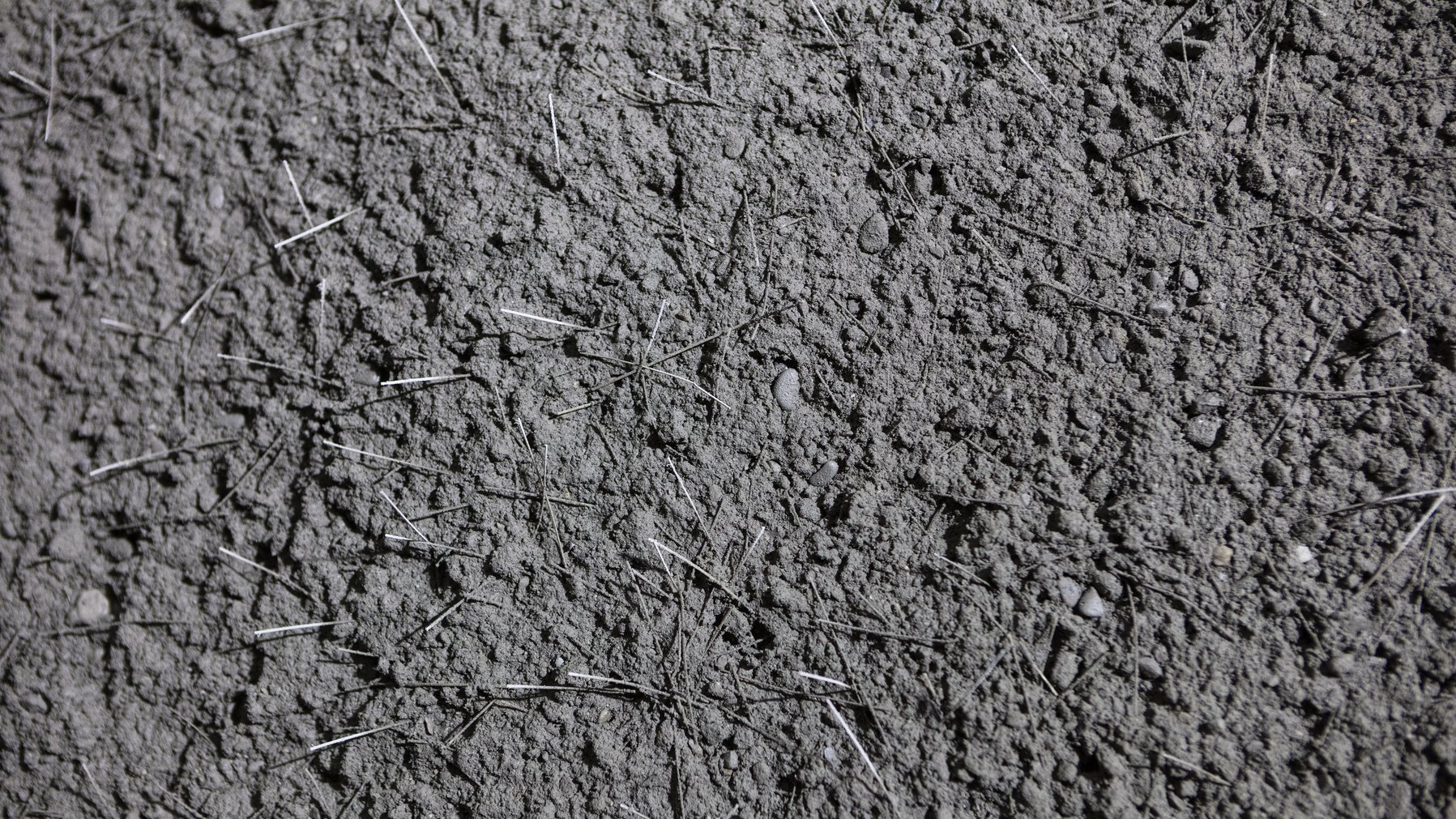
Fibre-reinforced concrete
Building materials scientists are finding more and more ways to reinforce concrete. For example, the Implenia Building Materials Laboratory took part in the “C3 – Carbon Concrete Composite” research project, which tested how bundled carbon fibres could be used to reinforce concrete instead of steel. Carbon fibre concrete is lighter than conventional steel-reinforced concrete, as well as being more tensile and corrosion-resistant.
Read more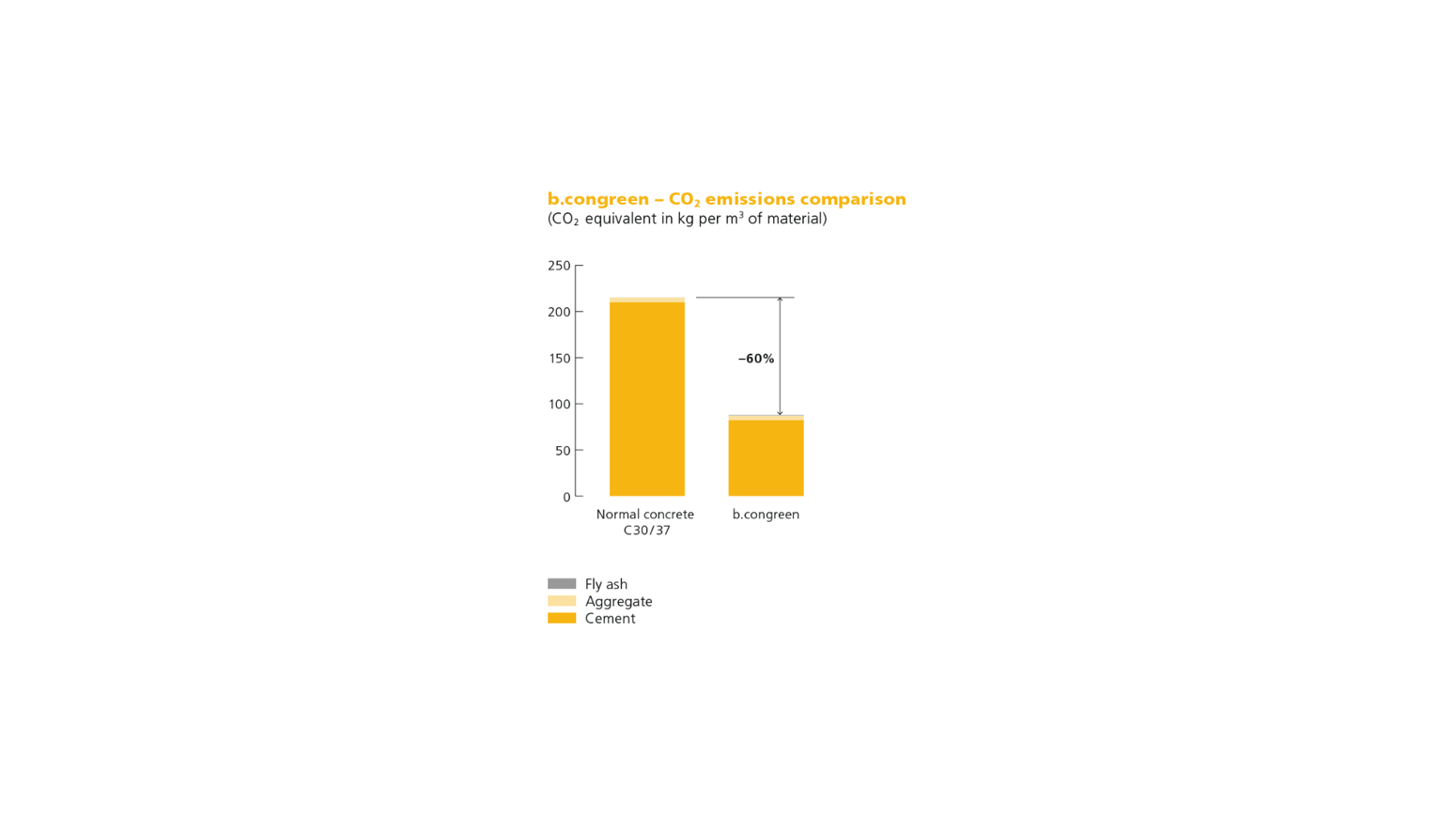
Climate-friendly concrete
The main ingredient of concrete is cement, which is made using a very energy and CO2 intensive process. In recent years, Implenia’s Materials Engineering Department has been developing more sustainable recipes for concrete. One of these is “b.congreen”, in which fly ash sourced from power stations replaces some of the cement. Up to 50% less greenhouse gases are produced during production.
Read more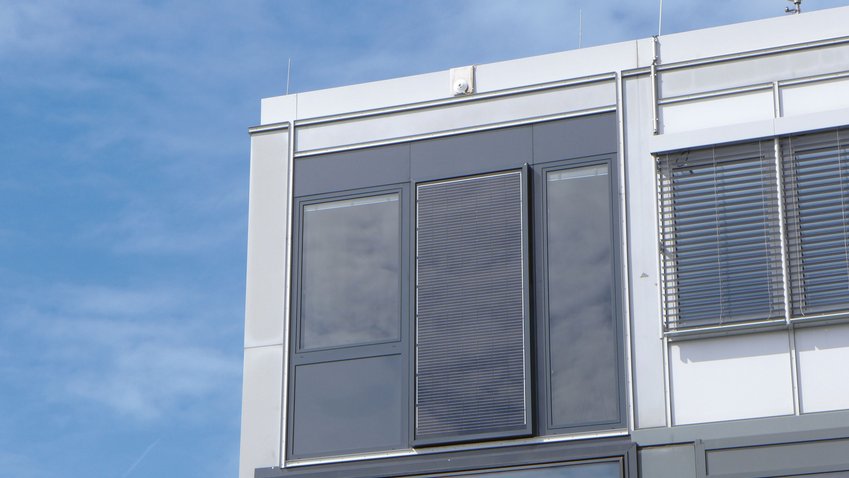
Facades as power generators
In Germany, Implenia Facade Technology is working with the Fraunhofer Institute for Building Physics (IBP) to develop modular facade elements that can supply buildings with energy. As well as electricity-generating photovoltaic modules, these elements include components such as micro-heat pumps, and ventilation systems with heat recovery technology.
Read moreInnovation Hub
In order to promote an innovation culture and initiate new solutions and business models, Implenia has been operating the Innovation Hub since 2019. The Hub harnesses the creativity of the company’s approximately 8,000 employees, who can submit their ideas via an online platform called Kickbox. This business innovation concept is used in many organisations around the world. In a three-step process, employees develop their proposal and test its suitability for everyday use. They are given a portion of their working hours and a start-up budget to work on the idea – as well as coaching from experts.
Implenia’s Global Sustainability team was deeply involved in the Innovation Hub concept. The Sustainability Department also offers advice to innovators and helps them optimise their ideas in terms of sustainability.
Since the programme started at the end of 2019, a total of 92 ideas have been submitted via the Kickbox. In mid-2022, a team reached the “Goldbox” stage for the first time – the final phase when the idea is ready to go to market. A site manager at the tunnel construction site in Semmering, Austria, developed a new type of thrust element that is lighter, cheaper and safer than previous products. After extensive testing, this innovative element is now being used in other tunnel projects tool. You can find more information here.
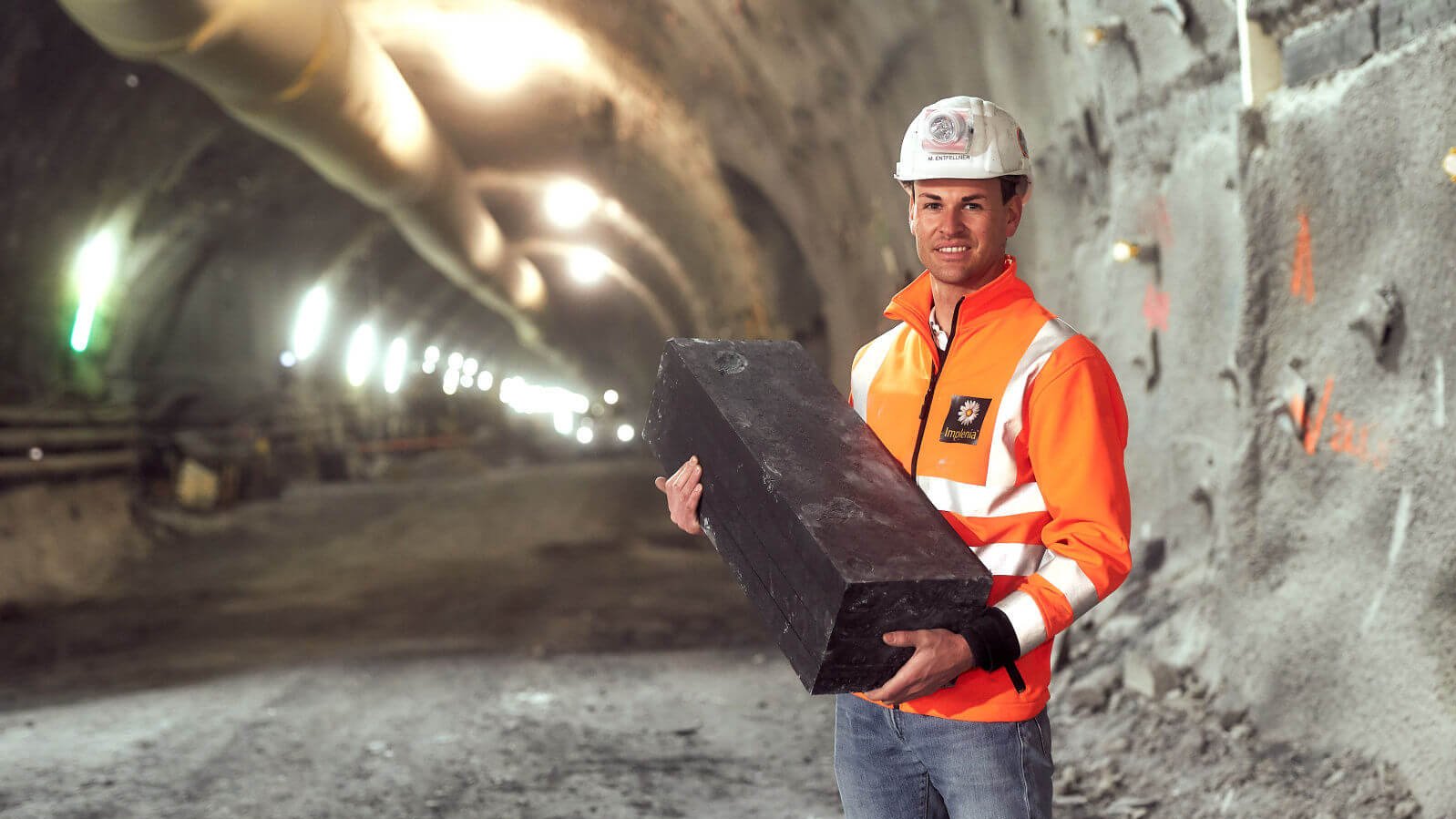
Supplier management
GRI 2-6, 2-23, 2-24, 2-25, 3-3, 308-1, 308-2, 414-1, 414-2
As a construction and real estate services company, Implenia buys in building materials such as cement, steel, wood, plaster and paint from external suppliers, as well as sourcing services from external carpenters, plumbers, gardeners, etc. In total, the Group spends about 60% of its revenue on suppliers and subcontractors.
To avoid risks in this extended value chain, the company uses a systematic supplier management system. Suppliers and subcontractors go through a multi-step qualification process that forms the basis for a long-term working relationship.
All business partners working on Implenia construction sites must comply with clearly defined minimum requirements based on the Code of Conduct (more information) in the areas of environment, working conditions, health and safety at work, quality, purchasing and finances. If Implenia finds that a company is not meeting these standards, no new contracts will be awarded to this company until the issues are sorted out. Implenia also follows the equality guidelines issued by the International Labour Organisation (ILO).
In addition, an increasing number of business partners are judged on their social, environmental and economic performance. For example, if a supplier can provide proof of the origin and recycling content of its products, it will receive a higher score. Partners who work sustainably can thus improve their chances of winning contracts.
Such opportunities for improvement are also discussed with subcontractors and service providers during audits. 70 audits took place in Switzerland in 2021 and 2022. Implenia concentrated on the largest business partners (in terms of purchasing volume) with which it implements joint projects.
In the long term, Implenia wants to work exclusively with sustainability-oriented companies. It has set itself a goal for 2025 of awarding at least 75% of contracts by value to business partners that have been evaluated according to sustainability criteria and that meet higher standards. In addition, it wants to adopt Group-wide procurement guidelines and train all purchasing managers in sustainability matters by 2025. By cooperating closely with business partners, it aims to eradicate any possibility of environmental or labour law breaches in its supply chains.
In accordance with foreseeable regulations in its markets, Implenia wants to make its future sustainability and business reporting even more transparent about supply chains; the company particularly wants to disclose the risk assessments and measures it takes with regard to human rights, conflict minerals and the prevention of child labour.