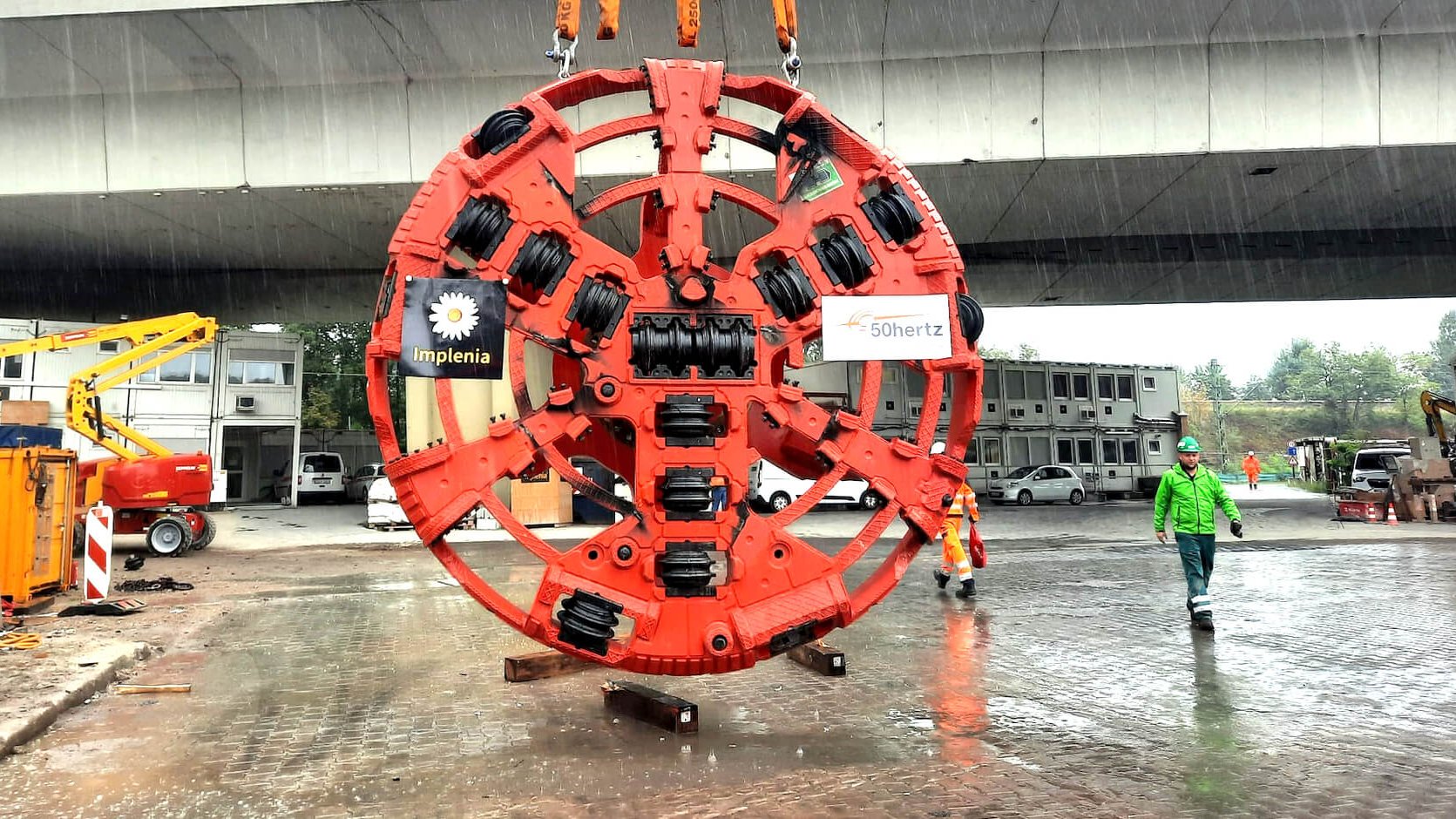
Underground power supply
Power supply of the future
The cable diagonal in Berlin is setting new standards: Thanks to the special drilling technology, the power supply is laid underground despite the complex geological conditions.
Become part of our VISION UNDERGROUND Community!
Cable diagonal in Berlin
The Kabeldiagonale Berlin plays a key role in the capital's power supply.
This innovative project not only advances the goal of the energy transition, but also masters the complexity resulting from the geological conditions. Thanks to the revolutionary technology, the tunnel remains accessible for future cable replacements, which significantly increases the flexibility and efficiency of the project.
Here we cover the following aspects:
- Power supply to the capital
- Challenging tunnel construction
- Shaft passage under Charlottenburg
- Sustainable innovation from Mannheim
- Repairing the cutting wheel
- Use of green electricity
Powering the capital on a grand scale
How do you actually supply a city of millions with electricity efficiently? This question poses many a challenge in times of the energy transition and growing population figures. The basic answer to this question was established back in the 1970s and has since been continuously expanded, modernized and strengthened in order to meet Berlin's growing supply requirements.
Challenging tunnel construction
The 380kV cable diagonal is not only one of the capital's most important power lines, but also a structural masterpiece: the 19.8 km extra-high-voltage line runs from the north-west of Berlin through the city center towards the east, rivaling the longest power lines in London and Vienna. The extraordinary technical challenge of the cable diagonal was Berlin's sandy, waterlogged subsoil and the pressure of 2.5 bar at a depth of 25 meters.
The cable diagonal grows with its tasks - and it does so in depth. Thanks to numerous innovations in the construction industry, the originally underground power line can now be renewed using tunnel construction to significantly increase its current-carrying capacity. This is as innovative as it is costly: On the one hand, tunnel construction creates the space that the 380kV cable diagonal needs to ensure a sustainable energy supply for Berlin. On the other hand, the construction work is particularly complex due to the changing geological conditions and requires well thought-out concepts in the areas of safety and sustainability.
Construction project with a deep shaft passage under Charlottenburg
When the tunnel drive reached a length of around two kilometers and the tunnelling machine approached an intermediate shaft in Charlottenburg, an idea emerged on the Implenia construction site that was to become a masterpiece of tunnel construction engineering: The plan was to drive through the Charlottenburg intermediate shaft with a Hydroshield tunnel boring machine (TBM) under atmospheric conditions. If successful, this would result in a time, quality and financial advantage for the construction project. In addition, a sustainable power supply would benefit the population of Berlin and Implenia would make a significant contribution to the energy transition in Germany.
This project was by no means going to be easy: Because in the immediate vicinity of the Spree, Implenia's project managers had to face the challenges of the high water pressure (approx. 2 bar in the ridge) and the work in the curve area (radius R=300m).
Sustainable innovation from Mannheim for Berlin's tunnels
In order to successfully withstand the challenging conditions underground in Berlin, Implenia's ETS in Mannheim manufactured a movable adjusting ring complete with steel structure, which was then transported to Berlin and assembled on site. Another test run was followed by installation, which heralded the hot phase of the project. The intermediate shaft in Charlottenburg was flooded so that the TBM could be driven in without any difference in water pressure.
In this way, Implenia's employees were able to reduce the risk of bypasses during the machine's entry into the shaft and enable a more sustainable steel construction. The successful entry was followed by the cleaning of the exit pot by divers and the TBM itself in order to achieve the necessary watertightness for the subsequent exit.
Repair of the cutting wheel under atmospheric conditions
Next, the adjusting ring seal was activated, the outer groundwater was separated from the inner shaft water and the shaft was drained in several steps. Finally, the cover of the exit head was dismantled and the cutting wheel was checked and repaired under atmospheric conditions in daylight. To continue the tunnel construction work, the TBM is pushed through the shaft via a concreted shield cradle to the opposite shaft wall while maintaining the seal in the adjusting ring.
Thanks to the excellent cooperation of all the units involved (TDO Mannheim, AV Munich, MT with ETS) and the construction site team, Implenia was able to achieve a flawless masterpiece from a single source with this project. Our energetic employees were able to demonstrate their extensive know-how and set a milestone in the history of tunnel construction on Berlin's cable diagonal. Implenia is thus making an important contribution to the expansion of Berlin's network.
Implenia relies on green electricity
- Implenia is working with Zeppelin Rental to supply all construction sites and properties with green electricity.
- The cable diagonal consumes as much electricity as 50 other Implenia projects put together.
- Despite the high electricity consumption, the entire project will be powered by green electricity.
- The Kabeldiagonale is the first project in Germany to make targeted use of green electricity for tunnel driving.
- The Kabeldiagonale thus promotes the expansion of renewable energy.

Subscribe to newsletter
Get thought-provoking, in-depth information now.