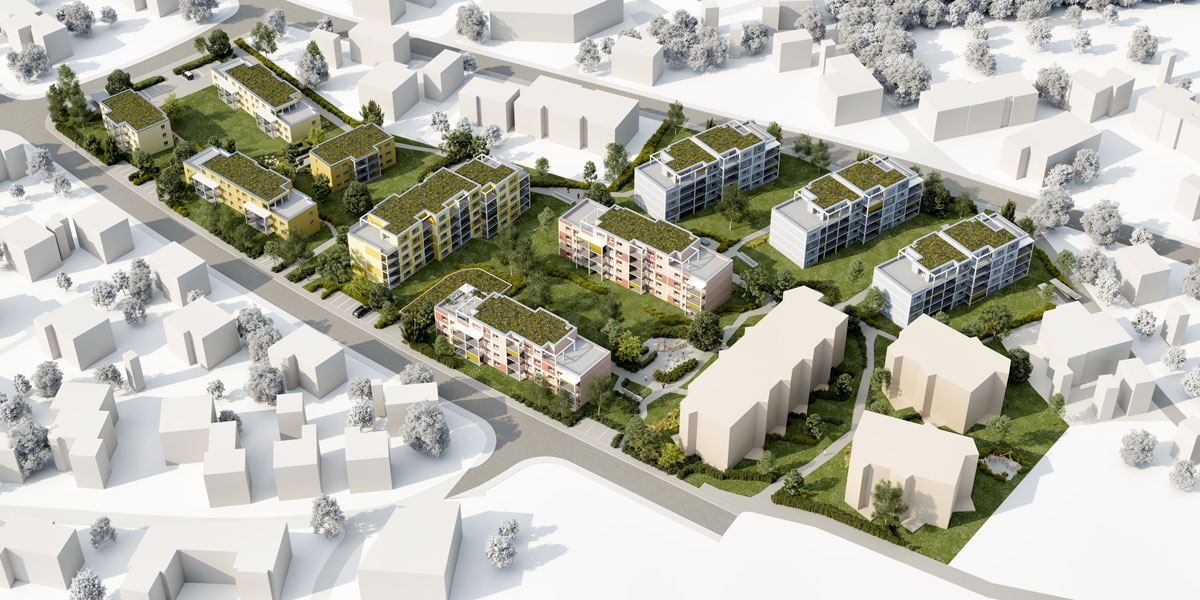
"Vogelsang"
Legendary "Göhner Settlement" interpreted in a modern way
Nestled between the idyllic Kemptnertobel recreational area, the centre of Wetzikon and Lake Pfäffikon is the Vogelsang housing estate. The area was developed in two stages in the 1970s and 1980s. The first construction phase - and thus the majority of the development – can be traced back to the legendary Zurich building tycoon Ernst Göhner, the Swiss pioneer of element construction. Using his prefabricated concrete slab construction method, he built around 9,000 flats from 1965 onwards, mainly in the greater Zurich area, with spacious layouts and affordable rents for the then rapidly growing young middle class.
Upgrading for "Göhnerswil"
Now the Vogelsang estate is being modernised in several stages by Implenia on behalf of the client Credit Suisse, and its simple style is being reinterpreted. Ten of the existing twelve buildings are undergoing a complete interior and exterior refurbishment. At the same time, these buildings are being raised in timber construction from 110 to 146 residential units. As a project development by Implenia, three apartment buildings with a total of 52 condominiums are to replace two other Göhner buildings in a further construction phase under the name "purNatur". At the same time, the entire site will be given a more uniform design, which is intended to emphasise the cohesion of the individual buildings in terms of design. This will turn the former "Göhnerswil" into a modern housing estate for people who want to live in the countryside without having to miss the proximity to the city.
Solutions from a single source
Implenia is offering its own services from various business areas for this project - from development and general contracting to timber construction, engineering and execution. "Our client benefits greatly from this group-wide collaboration," says Manuel Angst, Team Leader Execution on the Vogelsang project, and continues: "Because the project is at the centre and not the individual departments involved, everyone is pursuing the same goal. In addition, there are fewer contracts and submission procedures, and reaction times are shorter. This flexibility brings enormous scheduling advantages for the entire construction."
Accordingly, the project is progressing quickly: since the start of construction in July 2017, more than half of the work has been completed, according to Manuel Angst, and 32 rental flats are already occupied. In the next few weeks, more units will be handed over to the client, Credit Suisse.
Additional speed through wood and lean management
According to Manuel Angst, the comparatively short construction time can be attributed to other reasons as well: "The addition of timber not only benefits sustainability, but also saves an enormous amount of time due to the high degree of prefabrication and planning accuracy compared to traditional construction methods." Additional speed in the project is provided by proven lean management methods, with which construction processes are timed and standardised in such a way as to ensure the most efficient and reliable execution possible. All rental flats are scheduled to be completed and handed over to the developer by spring 2019. Occupation of the condominiums in the three new apartment buildings is planned for winter 2020.
Your new home in Wetzikon-Kempten?
There are still vacant rental and owner-occupied flats:
www.vogelsang-wetzikon.ch / www.purnatur-wetzikon.ch
Short paths and flat hierarchies
Adrian Ulrich (picture, right), Project Manager Timber Construction / Carpentry, and Marcel Fink (picture, left), Construction Manager Carpentry, explain how Implenia can offer its portfolio of services from a single source.
How do your departments work together?
Adrian Ulrich: Timber construction and carpentry have numerous interfaces, so our cooperation is very close.
Marcel Fink: As a joinery, we are heavily dependent on timber construction. So we have to be able to rely exactly on the delivered dimensions. Experience has shown that this works better internally than when we work with third-party companies. In addition, we can ask directly and unbureaucratically at the construction site if anything is unclear and we also have access to all the planning documents. This is particularly important for projects with a large volume for the carpentry workshop, such as the Vogelsang housing estate, where we did all the interior woodwork with the exception of the kitchen construction.
Implenia offers a wide range of different construction services. Is it often the case that you only deal with internal partners?
Ulrich: Internal collaboration has indeed intensified considerably, for example with engineering and the master builder. In projects that are created almost exclusively by Implenia units, details can be optimised at an early stage, which brings benefits for the entire construction process.
Does this simplify the daily work?
Fink: The shorter distances save us a lot of time. We know each other and the responsibilities are clear. In addition, we are usually on a first-name basis according to the Scandinavian principle. That makes for flatter hierarchies and makes a lot of things easier.
And how is impassability dealt with?
Fink: Smaller challenges are dealt with quickly and directly or we meet briefly at the round table.
Ulrich: We tackle major impasses via the Implenia Management System (IMS). Here we can assign tasks to the various departments or responsible parties and set corresponding deadlines, just like in a ticket system.