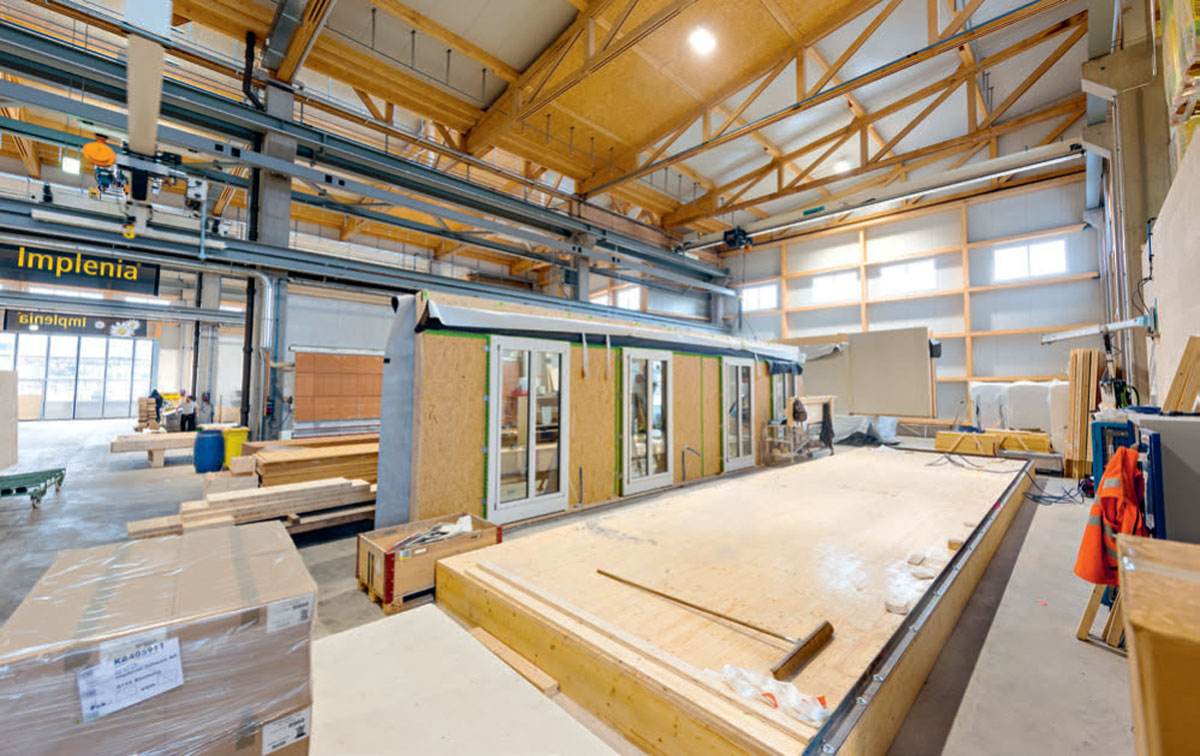
Bigger, brighter, faster
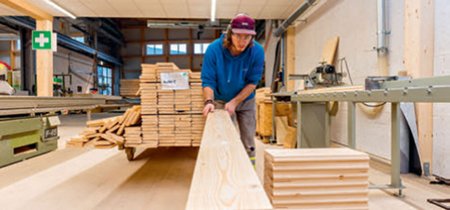
Implenia's new production hall in Rümlang makes full use of the advantages of modern timber construction: planning, material delivery, processing and delivery of the finished elements are optimally coordinated in terms of space. State-of-the-art technologies are used in production and the entire process chain is digitally networked.
Three projects in parallel
The high and bright building is divided into two logistics halls and three production halls. This means that work can either be done on three projects at the same time or a demanding project with many different elements can be managed in parallel.
No torsion thanks to turning tables
Seven bridge cranes for loads up to 5,000 kilograms and six bracket cranes for loads up to 1,600 kilograms ensure fast transport between the individual work steps. The elements are produced on a total of eight large assembly tables. Two of them are so-called turning tables that can independently turn wooden elements up to 14 metres long. This means that no torsion can occur in the element. The physical strain on the employees is reduced to a minimum with this infrastructure.
3D visualisation in assembly
Productivity is also increased by the seamless digitalisation of processes from planning to the construction site. Every assembly workstation is now equipped with a computer. Work plans and 3D visualisations showing all details are displayed on this computer. "This means that many questions about production can be answered right at the workstation," explains production manager Silvio Neumann. In addition, digital networking supports quality management: you always know who produced what, when and how.
Short paths, fast solutions
It is not only the manufacturing processes that are efficient in the new hall. The distances between production and planning have also become much shorter, as Neumann points out: "Because the offices are right above the production halls, we can now discuss changes with the planners in ad hoc meetings and quickly find the best possible solution."
The pipeline is full
The new infrastructure can prove its efficiency right from the start. Among others, school pavilions in Dietlikon and the large-scale project "Werk 1" in Winterthur are in the pipeline. Interest in wood as a material is growing unabated. Implenia is excellently equipped to meet the growing demand.
Interview with Silvio Neumann, construction manager timber construction / production manager element construction
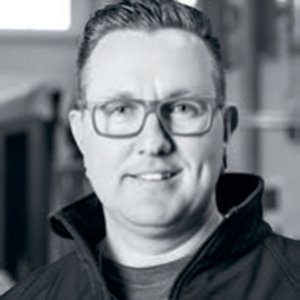
Mr Neumann, how do customers benefit from the new production hall?
Above all, from the significantly higher efficiency. The location is optimally designed for our processes and the transport connections are excellent. This makes everything much faster and saves costs accordingly.
Are projects possible today that were not feasible before?
Yes. In our larger halls we work with more staff, modern infrastructure and faster processes. This increases our capacity by about a third and enables us to complete even more complex projects on time and in the best quality.
More complex in what way?
In terms of size, weight and logistics. We have more space and a powerful crane infrastructure. This allows us to increase the degree of prefabrication and, for example, to realise complete modules with floor, walls and ceiling.
What do the employees say about the new hall?
They are enthusiastic all round. For example, they appreciate the many cranes that make the work easier. Before we had three, now we have thirteen.
And what do you particularly like?
For me, the most important thing is that I now work with the whole team under one roof. That makes coordination easier and promotes team spirit.