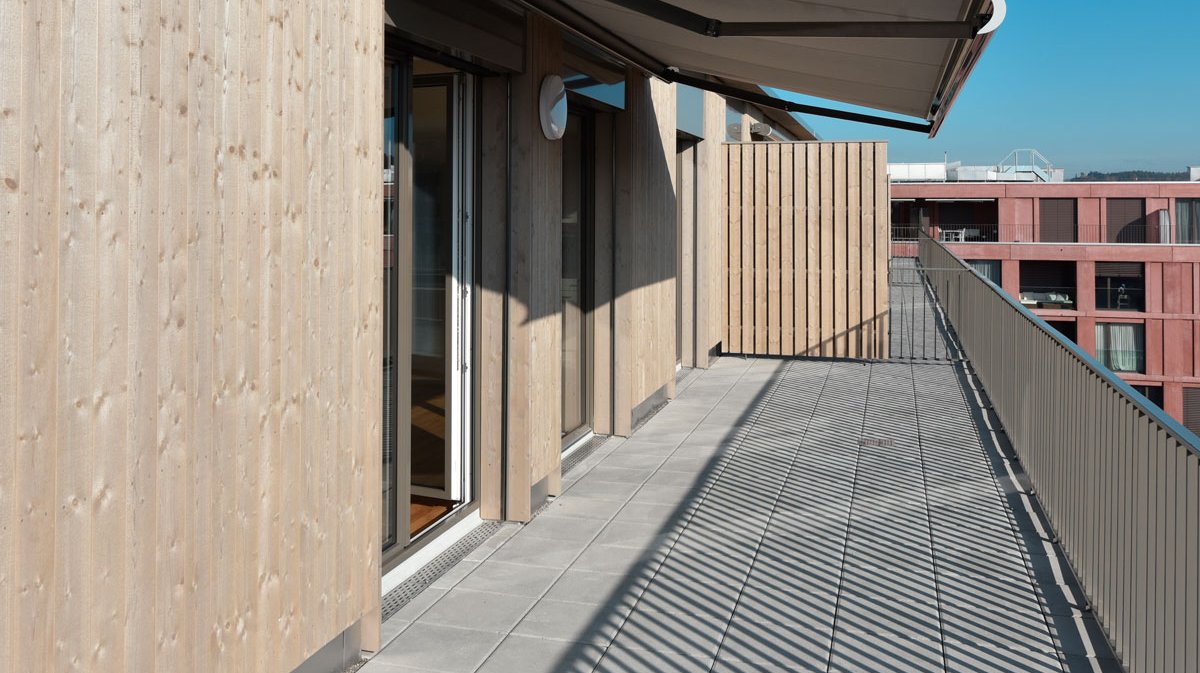
A sustainable village in the middle of the city
The TownVillage in Winterthur Neuhegi is a village in the middle of the city. The development is aimed at mixed-generation living and will offer seniors, families, single parents and assisted living groups for people with mental limitations a common home. The building owner is the Quellenhof Foundation, which is committed to the reintegration of addicts or mentally ill people and provides, for example, IV jobs in its workshops or places to live.
For the realisation of TownVillage, the foundation engaged Marti Gesamtleistungen AG. As a total contractor, it is currently constructing three new five-storey buildings on the compact 10,000 m2 site on Barbara-Reinhart-Strasse, which harmoniously connect the existing buildings – a congress centre and an old industrial building.
Millimetre work required
The buildings themselves are being constructed using traditional solid construction methods, but the outer wall elements and the facade are being built with wood. For this work, Marti Gesamtleistungen AG brought Implenia's timber construction specialists on board. "We are producing the external wall elements for all three TownVillage buildings, with the entire construction being carried out as a frame structure," explains Adrian Ulrich, project manager for timber construction at Implenia. The facade is built using a mixed construction method with durable, standing timber formwork and lightweight Alucobond aluminium composite panels. This calls for the utmost precision, as Ulrich explains: "Whereas with wooden formwork you always have a certain amount of leeway, with Alucobond every millimetre counts. The facade panels are manufactured on the basis of the plans and can only be minimally corrected on the construction site."
Perfect organisation required
Ulrich describes the space conditions on the site as a further challenge: "As a timber constructor, we process an enormous amount of material on the construction site within a short period of time." In addition, space is needed to erect the prefabricated elements. "On the one hand, this requires almost perfect organisation, but on the other hand, it also requires a certain flexibility - for example, to be able to cope with bad weather conditions. "Thanks to the close cooperation, open communication and weekly execution meetings with Marti Gesamtleistungen, as well as the professional planning on both sides, the ambitious schedules of the first construction stage could be met," says Ulrich.
The TownVillage South building with workshops and offices of the foundation as well as eight flats, which was completed in the first construction phase, has already been occupied. The entire development is due to be handed over to the client in August 2020 and will then house a total of 61 flats, a restaurant, a café, a care area and various event and meeting rooms. When the project is completed, Implenia will have installed around 2,500 m2 of wall elements, 1,500 m2 of wooden facade and around 1,800 m2 of Alucobond facade.
Interview with Oliver Gruenberg, Head of Zurich Branch Marti Gesamtleistungen AG
Mr Gruenberg, why were the exterior walls and façades of TownVillage built using timber construction?
On the one hand, the Quellenhof Foundation has prescribed a good ecological balance for its building project. The entire site planning is based on the SIA Energy 2040 efficiency path. And with a timber construction, these goals can be achieved much more efficiently. On the other hand, the wooden façade fits in ideally with the surrounding neighbouring buildings.
Why did you bring Implenia on board for the woodwork?
In terms of price and know-how, other timber constructors simply couldn't compete. Together with Implenia, we were able to optimise the project and adapt it to the client's ambitious budget plans.
What characterises the collaboration with Implenia for you?
We have contacts at eye level who listen and provide valuable input. We also appreciate the excellent execution planning and the open and cooperative communication. All employees are enthusiastic about what they do and have a real passion for wood as a material. And for me, a not insignificant point: there is always meticulous order on the construction site. It is extremely rare to find even a single piece of wood lying around.
Why is this so important?
That may sound pedantic at first, but for me this order reflects Implenia's many years of experience: the fitters know exactly how much and which material they need. Ultimately, this not only saves waste and thus costs, but also has a positive effect on fire protection and occupational safety.