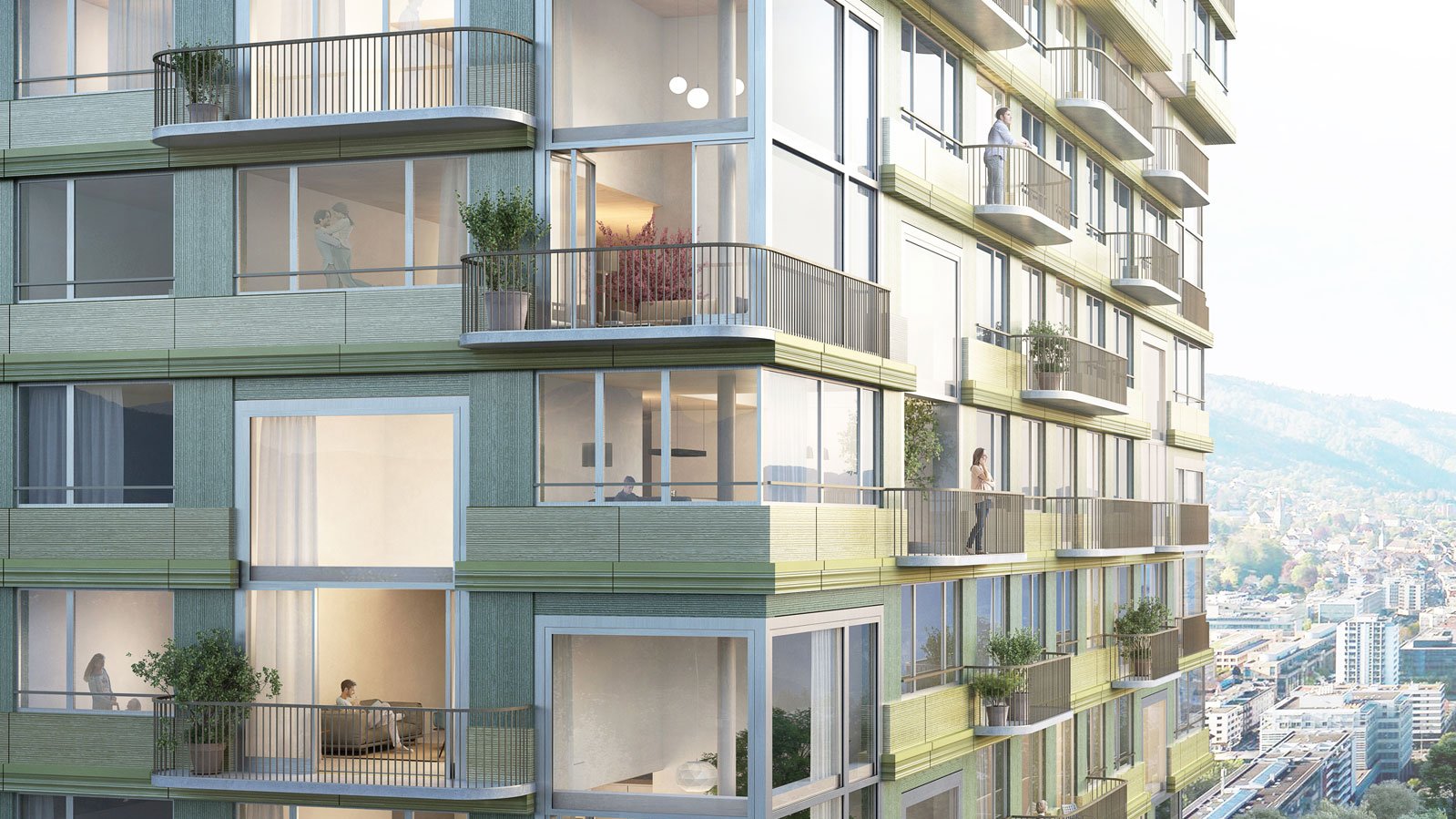
Wood up to the clouds
A few years ago, they were still a utopia. In the meantime, they have become reality in many places: skyscrapers built of wood. The record is currently still held by the Mjos Tower in Brumunddal, Norway, at 85 metres. However, buildings are already being planned that will rise 300 metres and higher into the sky. In Switzerland, Urban Assets Zug AG is tackling the first high-rise building on its factory premises in Zug, where all the supporting structures will also be made of wood.
Thousands of tonnes of CO2 and francs saved
However, the Pi project is not only unique because of its height of 28 storeys and 80 metres, which has never before been achieved in wood in our country. The project partners Duplex Architekten, WaltGalmarini Bauingenieure and Implenia are also breaking new ground in terms of construction technologies. All in all, they make it possible to reduce the weight of the supporting structure by 34 per cent compared to steel frame constructions. Even the hybrid timber high-rise buildings commonly used to date, in which a concrete core takes over a large part of the load-bearing functions, are 17 per cent heavier. Correspondingly less foundation work has to be done. And this has a direct impact on the grey energy that is generated during construction. The Pi project directly saves the equivalent of 1700 tonnes of CO2. Added to this are 3333 tonnes of CO2 that remain stored in the wood as a building material.
With two wooden frames and minimal foundation
These striking improvements are achieved by a supporting structure consisting of an inner and an outer timber frame as well as special timber-concrete composite slabs. The outer of the two supporting frames of the so-called tube-in-tube system forms the framework for the windows and facade elements and sits directly on the diaphragm wall that closes off the excavation. A special foundation thus only has to be built for the masses that the inner wooden frame supports. "In a conventional reinforced concrete high-rise of this size, around 30 per cent of the total reinforcement is used in the foundation, and that costs a correspondingly high amount," says Tobias Hohermuth. Implenia's Head of timber construction emphasises that in the high-rise project, the advantages of timber construction practically add up floor by floor.
Advantages of timber and concrete ceilings combined
Significant additional weight savings are achieved above all by the novel ceiling system that WaltGalmarini's civil engineers developed with Implenia's timber construction department and the ETH as part of an Innosuisse project (see accompanying interview with Wolfram Kübler). It combines the advantages of a concrete flat slab – such as the biaxial load-bearing capacity, robustness and flexibility in the installation of building services – with the weight and visual qualities of wood. The composite construction is not only extremely light. It is also thinner than all previous constructions. This made it possible to accommodate an additional storey within the maximum height of 80 metres specified by the city of Zug. This also means hard cash for the builder.
Two-storey mockup for realistic tests
Implenia and its project partners are breaking new ground with the timber tower. The technologies used are therefore being tested intensively in experiments. The ceiling system has already been extensively tested for stability and vibration and sound behaviour as part of the Innosuisse project, in which it was developed independently of the Pi project together with the ETH. In order to have the concrete application in Project Pi completely under control, a mock-up of a building corner over two floors is now also being created. The measurements on the 1:1 model are not only intended to give the building owner security, but also to ensure that the complex logistics are not slowed down by unforeseen complications.
Demanding logistics as a special incentive
Managing the construction of Pi will be a particular challenge and Hohermuth is looking forward to it: "That is why working at Implenia timber construction is particularly exciting. We implement extremely demanding projects that represent the technological cutting edge in building construction." For example, new production facilities have to be built for the manufacture of the ceiling elements, in which the modules can be concreted directly. Pre-production and assembly must also be precisely timed. This is where Implenia's extensive digitalisation and BIM expertise comes in handy for the timber constructors. In order to also reduce transport costs, Hohermuth is currently investigating whether it would be worth setting up a temporary factory near Zug. Either way, the Pi project will write Swiss construction history and also give new impetus to high-rise timber construction worldwide.
Picture credits: Hochhaus Pi, competition stand, architecture: Duplex Architekten, Zurich / visualisation: Filippo Bolognese