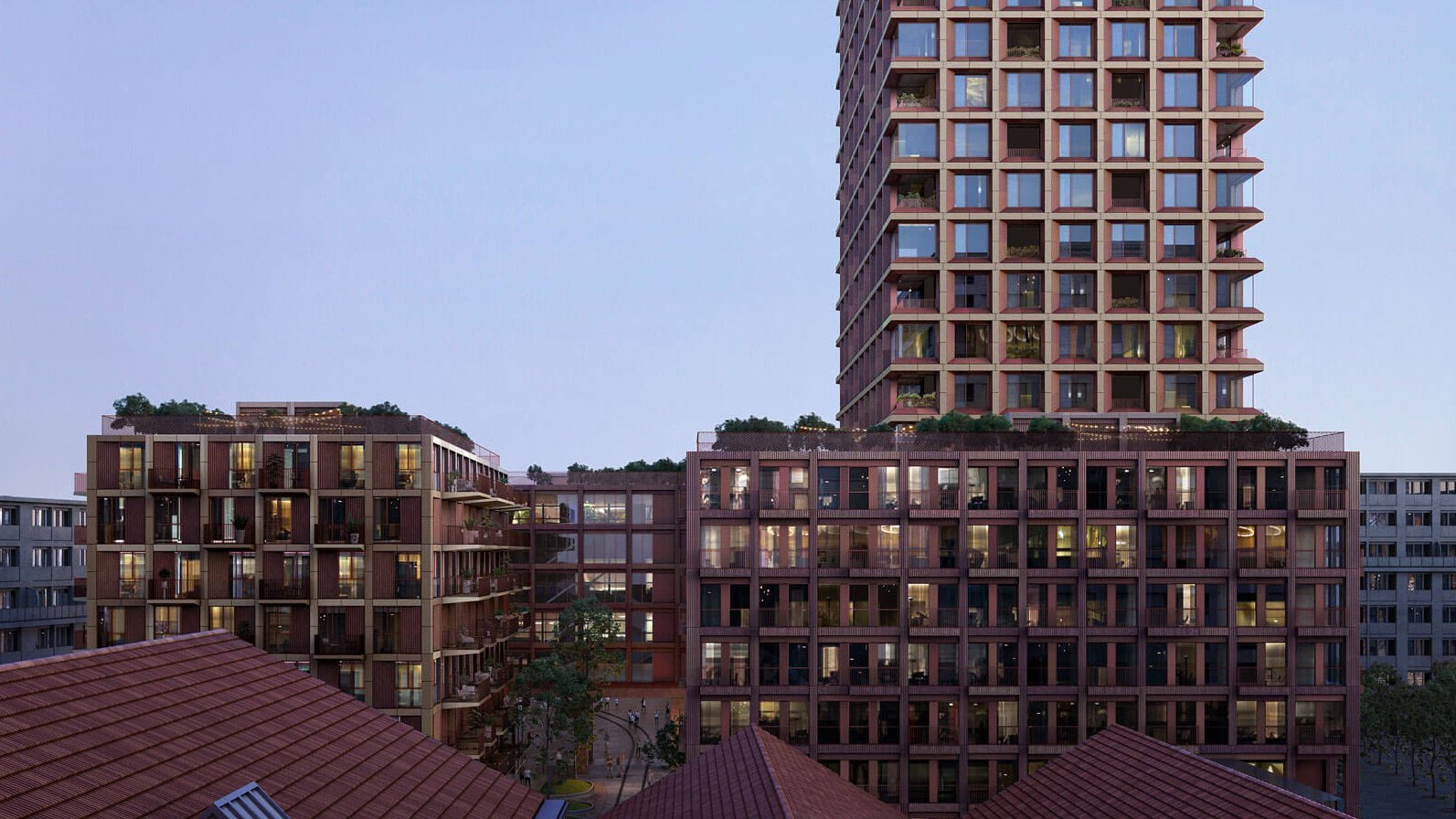
Health & Safety
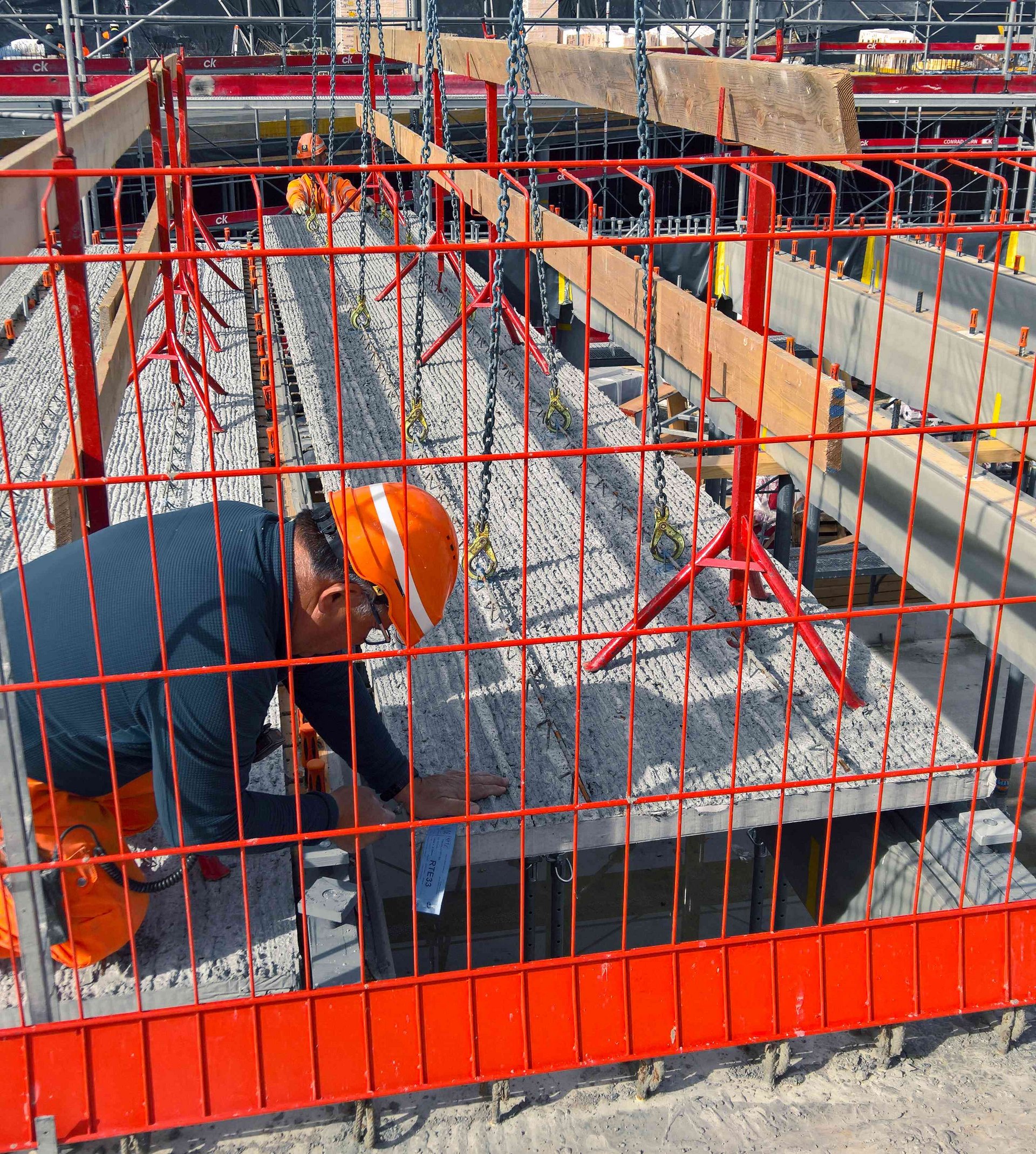
Pre-mounted fall protection
These pre-mounted railings mean suspended ceilings can be installed more safely.
Working on a construction site is inherently risky. The risks involved are the reason why health and safety is our highest priority – and why safety is a management issue for everyone from members of the Executive Committee to foremen on site. Implenia’s aim is to avoid situations that endanger people’s physical well-being and health. We are trying to create the safest possible working environment, as set out in our “Code of Conduct”, and to define the relevant rules and guidelines as clearly as possible. Together with regular and meticulous safety inspections on construction sites, intensive training courses and open communication, this is the basis for a dedicated safety culture that involves both managers and employees. Another important component is the regular reporting that gives managers of the relevant operational units an overview of the latest accident statistics and allows them to make forecasts. We can then recognise problems quickly and take the necessary corrective measures.
This year, our consistent focus on safety has helped us keep accident and absenteeism figures stable at 60 accidents per 1,000 full-time positions (2018: 60 accidents per 1,000 full-time positions). However, the fact that there are any accidents at all shows that we must keep up our efforts to make Implenia even safer and to reduce accident and absenteeism rates. Because even one accident or absence is one too many.
Projects and initiatives: Safety can be learned
Can you learn to be safe? Implenia believes that you absolutely can, which is why we carried out various programmes and campaigns in 2019, most of them at local level and in the operational units. We have also taken several initiatives that have a single goal: embedding safety awareness and the safety culture even more strongly throughout the Group. This begins when people first join Implenia: health and safety is a key focus of the induction programme for new trainees in Switzerland. Regular Health & Safety meetings and workshops were also held during the year under review as part of our internal H & S processes. At management level we used leadership workshops to create an even greater awareness of health and safety issues and of our Group-wide safety culture.
Cooperation on health and safety was expanded at international level. By talking to colleagues in different operational units and countries, we are learning from each other. The issues discussed include weekly updates of accident figures, best practices, new opportunities to introduce safety measures and potential for improvements.
A new, expanded safety programme is planned for 2020. We are intensifying and further improving campaigns and programmes that are already running, and our motto “Health and Safety is a Management Issue” will be made an even more central part of the safety awareness of employees at all levels of the hierarchy.
Prevention: every accident is avoidable
We believe that every accident can be avoided. The key to this is prevention. Our aim is to make accident prevention even more consistent at Implenia, and to put our safety culture even more to the forefront of our actions and our discussions with each other. Our internal safety officers play a central role here. They give direct support to line managers on our construction sites, helping them implement and monitor safety processes and sensitise employees to these processes. Meanwhile, “15-Minute Safety” training sessions take place each month at every Implenia project, providing an opportunity to discuss risks and analyse the causes of accidents together. This sharpens awareness of the relevant dangers and so helps to prevent accidents. It is equally important for us to record and evaluate accidents centrally so we can see where improvements are required and initiate the right measures in response. In concrete terms, our clearly defined prevention objectives and activities include safety inspections by managers as well as discussions between line managers, accident victims and HR officers. It goes without saying that causes of accidents are thoroughly analysed, and each incident is comprehensively documented.
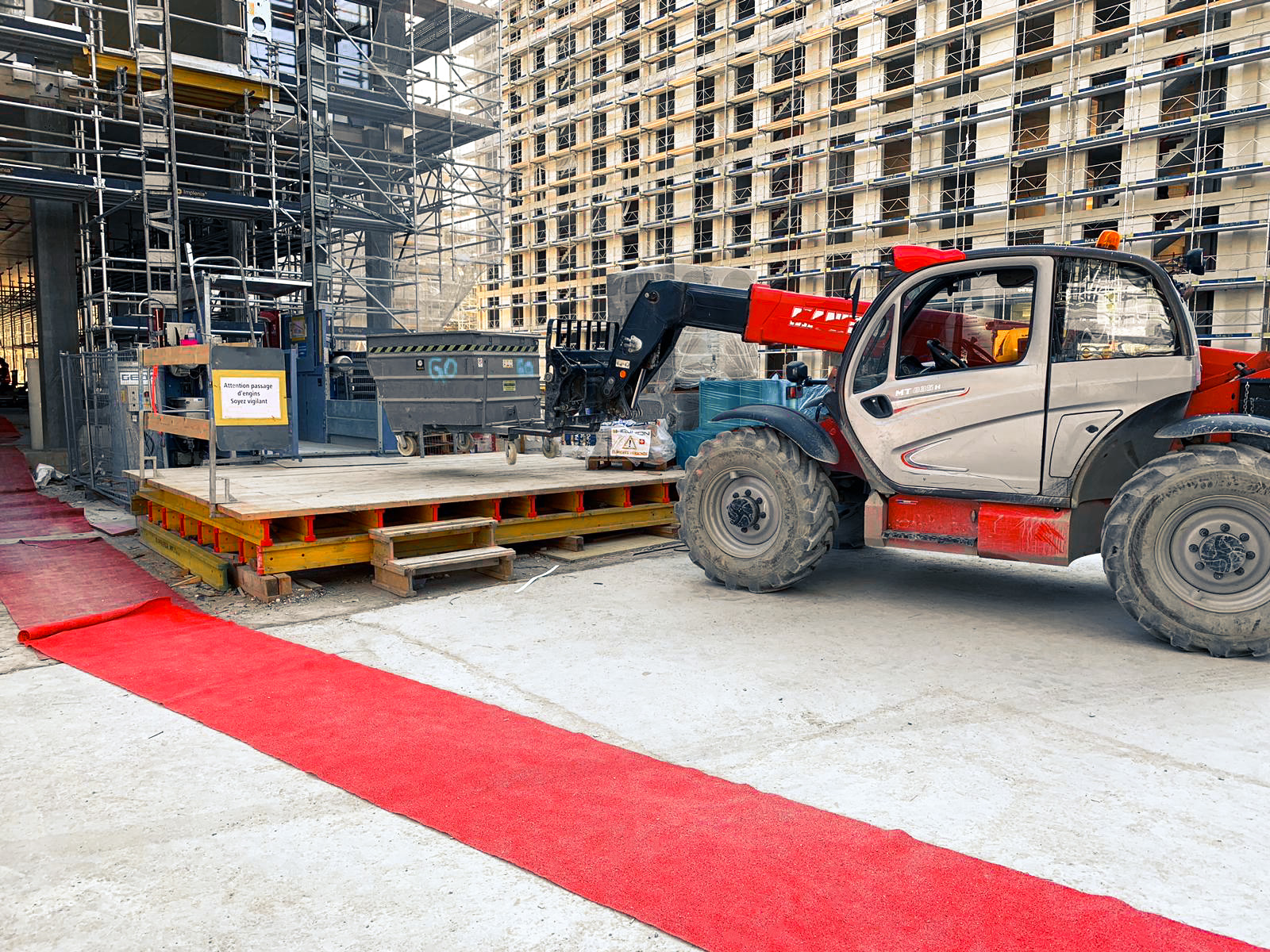
Red carpet rolled out
Red carpeting is used at the Pont Rouge project in Lancy to guide people safely through the construction site.
Finally we also make use of ideas and suggestions that our employees give us about the concrete, pragmatic things that can be done to prevent accidents. One good example is the “red carpet” used at our major Pont Rouge construction site in Lancy, which helps guide people safely around the site. Another is the simple pre-mounted railing system we’re using to improve safety for workers installing suspended ceilings at the office complex we’re building for the United Nations in Geneva. Shafts always present a possible danger of falling, so at our “Espace Tourbillon” project in Geneva we are using “Aestuver® boards” to completely cover shaft openings during construction – and afterwards too if required. Tailor-made holes for the necessary pipes and cabling can then easily be made as required. Another example is the adoption of full-face masks with integrated fans. Implenia Maintenance, for example, uses these on concrete spraying jobs to protect workers’ eyes and skin.
Health management: prevent, heal, help
We were able to keep the number of accidents at work stable during the year under review, and were even able to reduce the number of non-occupational accidents slightly (– 3.2 %). Most of the non-occupational accidents happened when playing ball sports, on the roads outside work hours, or as a result of slips and trips in the home or garden. The ratio between absences due to accidents at work and those due to non-occupational accidents was virtually the same as in 2018. Roughly 68 % of total absences were the result of illness, with another 18 % down to accidents at work and 14 % caused by non-work-related accidents. A total of 471 employees were off work for more than 30 days as a result of illness or accident in 2019. 1
The job of our internal occupational health management (OHM) team is to support our employees during recovery and as they reintegrate themselves into working life. Affected employees are put into a special reintegration programme that gradually reintroduces them to an appropriate independent activity, with external experts brought in if needed. The OHM team in Switzerland supported 168 people in this way during the year under review.
We at Implenia also know that prevention is better than cure, so we offer various preventive measures and training courses to help our employees stay healthy. The focus here is on workplace ergonomics and safety, and cardiovascular disease. We organised a special health day in Aarau in 2019 with a varied programme centring on these issues. Employees learned about how to set up their workplace ergonomically, for example. A yoga teacher taught exercises designed to relax the back, and there was an opportunity to practice using a defibrillator. We also carried out a series of health campaigns in Germany during the year under review, as well as taking part in various running events and a “Cycle to Work” campaign. Our employees in Germany also benefited from the “qualitrain” company fitness programme and a bike leasing offer.
Health & Safety Award: Implenia recognises safety efforts
Implenia has presented a Health & Safety Award every year since 2015. The idea of the award is twofold: firstly to emphasise how important the issue is to our company, and secondly to motivate our employees and increase their sense of ownership of the issue. The winner is chosen from submitted suggestions in an employee vote. The 2019 prize was won by the CERN Team at Implenia Civil Engineering France for their simple but effective initiative: all the workers at the CERN site have Vital-ID cards attached to their helmets, so that all the important information about the person is readily available in an emergency or accident situation.
1 Data from Switzerland
Accidents by type 2019
in %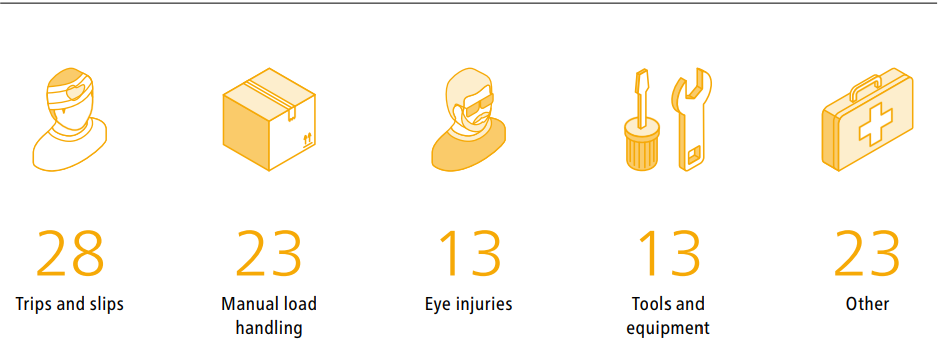