![[Translate to en-CH:] [Translate to en-CH:]](/fileadmin/gb/images/IMP_GB2020_KIM_Winterthur_High_Res_3683_spa.jpg)
[Translate to en-CH:]
[Translate to en-CH:]
Insight: Sustainably into the future
For over ten years, Implenia has been following a holistic sustainability strategy that addresses environmental, social and economic aspects. The construction services provider has now set itself ambitious new goals.
Sustainability is one of the most crucial challenges of our time. It is particularly significant for real estate and construction services companies because of their use of scarce raw materials and because the industry accounts for such a high proportion of global greenhouse gas emissions. It is also important because of the demand for housing and infrastructure in densely populated urban regions: 84.6 per cent of people in Western Europe will live in urban areas by 2040.
Implenia was early to decide that sustainability should be a leadership issue and the subject of strategic expansion. As well as being a Member of the Implenia Executive Committee, as Head Division Specialties, Anita Eckardt is also Head of Implenia’s Sustainability Committee: “It was more than ten years ago that Implenia became a pioneer in the industry by embedding sustainability firmly in its strategy. We have continued to build on this leading position: we have just given our sustainability goals a major overhaul and set ourselves twelve ambitious objectives for 2025. Reaching them is going to take a lot of hard work.” (See info box)
2025 sustainability goals
In 2020, Implenia formulated a series of ambitious sustainability goals for the next five years. Progress towards these is regularly assessed against measurable targets and documented.
1. Sustainable development & construction We develop and build according to the highest sustainability standards and contribute to their further development.
2. Sustainable supply chain We work with sustainable partners and continuously improve together.
3. Eco construction site We convince and support our clients by offering project-specific sustainability concepts and implementing outstanding sustainable solutions during construction.
4. CO2 reduction We aim for net zero CO2 emissions by 2050 and a reduction in our group-wide CO2 emissions by 15% by 2025.
5. Environmental protection We carry out professional environmental management in all projects to prevent environmental incidents.
6. Circular economy We develop new circular business models and promote the closing of material cycles.
7. Sustainability in our DNA We live up to sustainability in our daily actions and transparently communicate our learning and our results.
8. Engaged employees We aim for zero accidents, unconditionally stand for safety at work, modern working conditions, high employee satisfaction and a low fluctuation.
9. Implenia without borders We engage in social partnerships and collaborate with our stakeholders beyond the construction site.
10. Ethical governance We live a zero-tolerance policy towards compliance violations, always do business in a responsible and ethical manner and demand the same from our partners.
11. Sustainable finance We integrate ESG criteria into our business and investment decisions for clients, investors and society at large.
12. Digital & integrated processes We consolidate our reputation for operational excellence and high quality standards.
In this way we want to make sustainability an even more integral part of our day-to-day work, and root it firmly in the company’s DNA. To put our holistic understanding of sustainability into practice, we always define it in three dimensions: environmental, social and economic. Rolf Wagenbach, Global Head Sustainability: “When we are developing a service or a product, we ask ourselves three questions: what are the environmental, the social and the economic impacts? We’ll only start talking about sustainability if we achieve a positive effect in all three areas.” This can happen most consistently in projects that Implenia has developed itself; but the company wants to make sustainability transparent and measurable in all projects – by utilising sustainability labels and certification, for example. MSCI ESG has given Implenia an AA rating. And Sustainalytics, the world’s leading provider of research and ratings on environmental, social and governance (ESG) issues, currently has Implenia on an outstanding 79 points. This makes us a recognised leader in the industry. It is no coincidence that sustainability is one of our five corporate values.
Triple focus
We believe that three of our goals could deliver particularly significant effects:
3. Sustainable development and construction with a focus on wooden structures
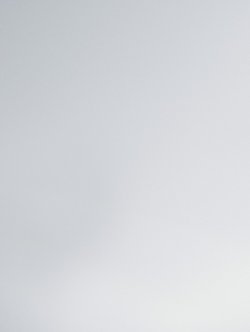
“We always ask ourselves three questions: What are the environmental, the social and the economic impacts of a project?”
Rolf Wagenbach
Global Head Sustainability
1. Circular economy
You can’t make an omelette without breaking eggs, and you can’t build without creating waste. We want to use closed-cycle models to reuse valuable raw materials rather than destroy them or send them to landfill. It’s high time the construction industry embraced the circular approach properly (see chart). Rolf Wagenbach: “This is how we address a very specific problem: the fact that often nobody knows what exactly was used to build a building, where precisely it was used and in what quality. The first step is to take an inventory of all the materials involved. We use BIM for this.”
Industrialisation has a significant role to play here too. If we can produce modular construction elements in a way that makes it possible to sort and separate the materials at the end of their life, they can be returned to the production cycle as secondary raw materials. So there is less waste. Anita Eckardt emphasises: “The more care we take in the development phase when we’re planning a building, the more efficiently it can be built, and then operated, and then at some point dismantled and integrated into the cycle for a future building. Digitalization is crucial here as an enabler for sustainability.”
Closed cycles
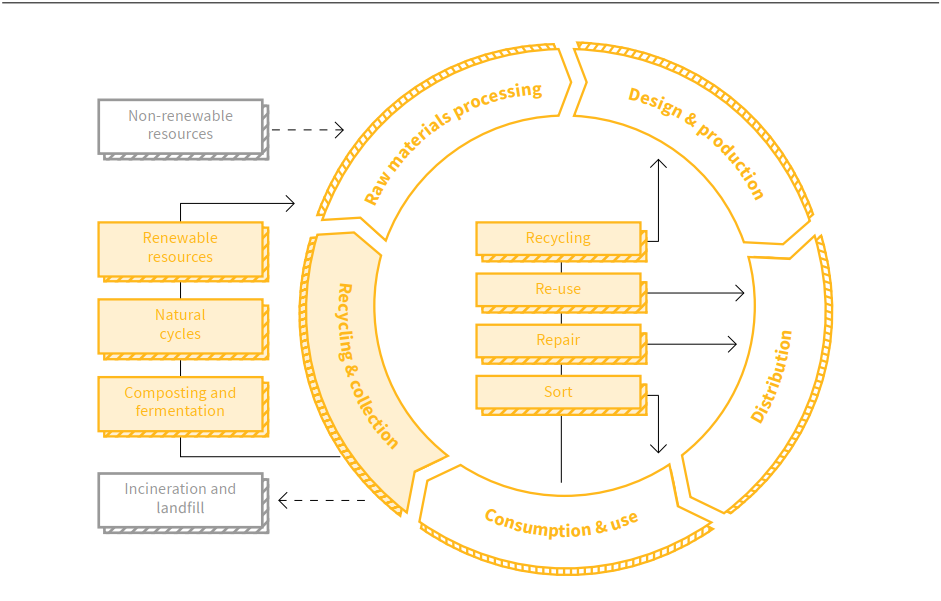
For example, on its own development projects Implenia uses at least 50% recycled concrete, made in a concrete works situated no more than 25 kilometres from the construction site. If gravel is produced as a result of excavation work, this will be recycled as close to the site as possible and used to make concrete.
Source: Federal Office for the Environment FOEN
2. Sustainable supply chain
Like any integrated provider of construction services, Implenia buys many of its materials and services – carpentry and plumbing, for example – from external suppliers. Our target for 2025 is that at least 75% of these materials and services are purchased from suppliers that we have assessed against transparent sustainability criteria and that meet our higher-level requirements. For some years now we have systematically checked the social, environmental and economic standards of our subcontractors and suppliers. We distinguish here between two things: minimum standards that everyone has to meet if they want to do any kind of business with us; and the additional higher-level requirements that allow our partners to set themselves apart. Rolf Wagenbach: “We have already assessed around 40 per cent of suppliers, and we continue to work on this as a high priority. The fact is that nobody in the construction industry can yet claim to have properly assessed all suppliers down to the individual trades. We want to change this.”
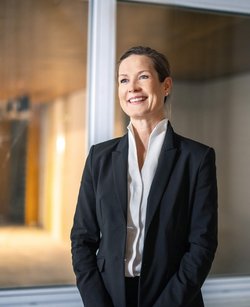
“Digitalization is an essential enabler for sustainability.”
Anita Eckardt
Head Division Specialties and Head of the Implenia Sustainability Committee
3. Sustainable development and construction with a focus on timber structures
“40 per cent of the energy used when building a building is accounted for by the load-bearing structure, so you can improve the energy balance significantly if you use wood for this,” says Anita Eckardt. With 90 years of experience in timber construction, Implenia is a pioneer with a long tradition behind it – just like the material itself. Technological progress means that wood has long been able to meet all the requirements relating to things like strength and fire resistance. And its qualities as a renewable raw material and store for CO2 make it much better than concrete from the environmental perspective. No wonder, then, that Implenia uses 50,000 cubic metres of wood a year – and rising – in Switzerland alone. And no wonder that Implenia is developing an increasing number of complex timber buildings. Like the Haus Furrer in Winterthur’s KIM neighbourhood: 5,500 cubic meters of wood are being used to build this residential and commercial complex, which includes a total of 208 apartments. Anita Eckardt: “We now check every project at a very early stage to see if timber construction is an option. If it is, we take it to the next stage.” Wood is also extremely well suited to the development and prefabrication of modular elements, so it is a very natural fit for a circular economy.
You can read more about Implenia’s holistic sustainability goals in the latest Sustainability Report.
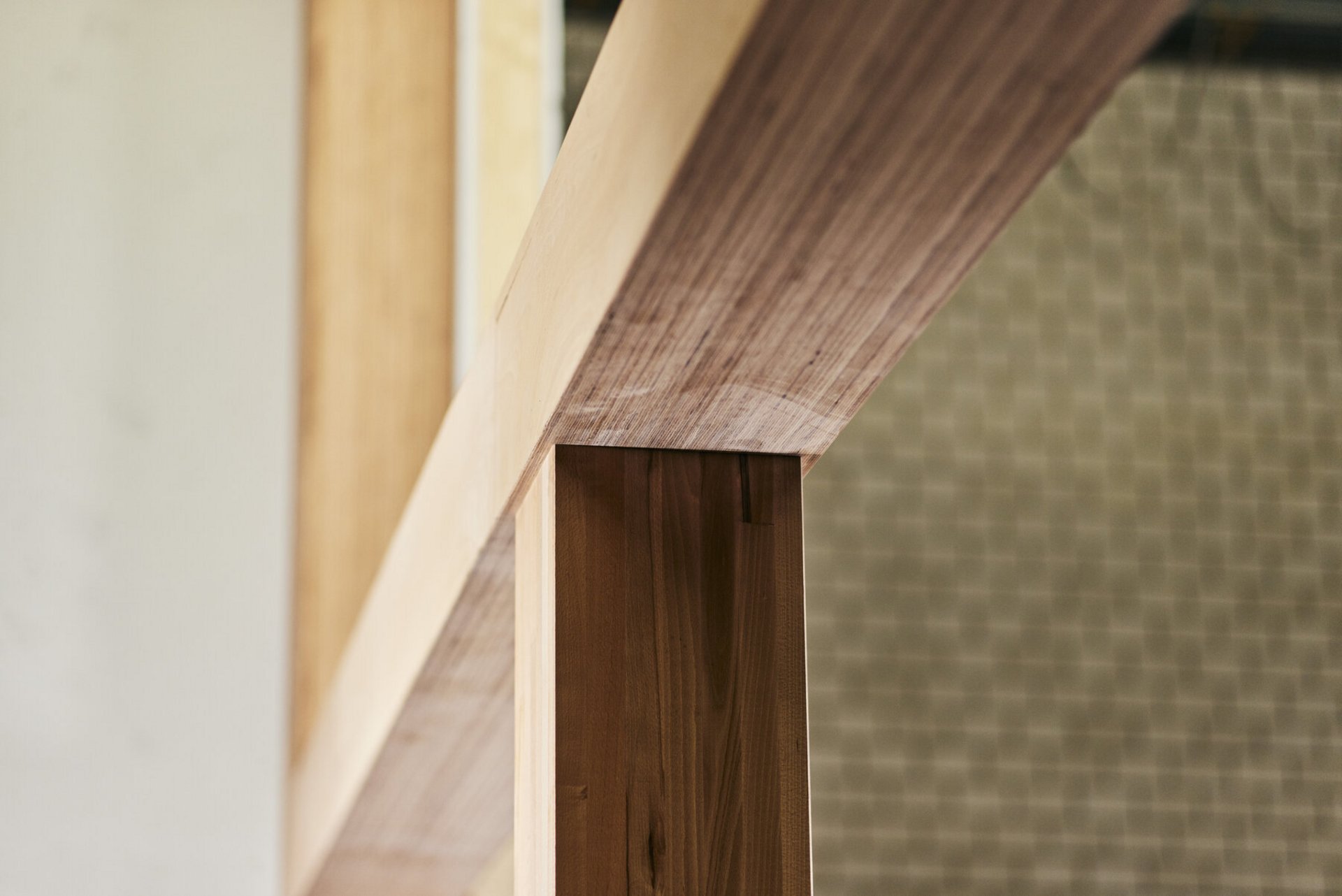
Use of wood in construction
Selected reference projects for timber construction:
- Implenia has built the country’s biggest ever timber-built housing project in Winterthur: 8,100 cubic metres of wood were used for the “sue&til” development and its 307 apartments. 80% of the timber came from Swiss woodland.
- Implenia is currently working as main contractor within the Zug Tech Cluster on what will be the tallest timber-built high-rise in Switzerland. Around 80 metres tall, the tower will be a beacon of environmental and social sustainability. The ten “vertical neighbourhoods” within the building, each with 22 residential units on three floors, have been designed for new forms of living together.
- At the Lokstadt site in Winterthur, Implenia has built a high-rise residential building known as “Krokodil”. Containing 254 apartments, some of them cooperatively owned, this building used 7,700 cubic metres of wood.
- In the new KIM neighbourhood, also in Winterthur, another timber construction project is due for completion in 2021. Haus Furrer, a mixed-use residential and commercial building with a total of 208 apartments, is being built with 5,500 cubic metres of wood.