![[Translate to en-CH:] [Translate to en-CH:]](/fileadmin/_processed_/4/8/csm_IMP_GB2020_Green_Village__Genf_High_Res_3186_spa_70a3788a27.jpg)
[Translate to en-CH:]
[Translate to en-CH:]
Insight: Space for future generations
Implenia develops, designs and builds sustainable properties for future generations, and it will keep doing this even more efficiently – and more digitally – in future.
It often starts with nothing more than a site and two basic questions: What could be built here? And for whom? You have to answer these questions before you can ask the next: How can we best implement the idea? In terms of design, planning and construction? “Property development is always about breaking fresh ground. You can bring all your experience with you, but you still have to start from scratch every time,” says Adrian Wyss, Head Division Real Estate. “Our aim is to create competitive, profitable, but also socially and environmentally sustainable places to live for future generations.”
The Green Village project in Geneva is a good example. Seven buildings set amongst landscaped gardens are being created here in the middle of the city’s international quarter, all built according to the sustainability principles formulated by the Swiss organisation One Planet Living. Implenia won the tender and started developing the site in 2012. The first building will be completed in 2022. Adrian Wyss: “Periods of ten years are quite normal when developing complex projects. In our business you need a clear vision and plenty of stamina.” You also need transparent processes that ensure maximum efficiency in every phase of the project.
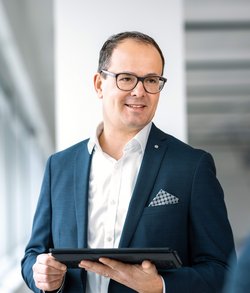
«During the planning phase, we start with an idea of how the site could be used, develop this into a concrete project, and ensure everything is based on sound commercial logic.»
Adrian Wyss
Head Division Real Estate
From idea to finished product
The first step is to carry out comprehensive analyses in order to obtain a precise, data-based picture of future users. Adrian Wyss: “Our job in the planning phase is to formulate a concrete project based on a usage proposal, and then test its commercial feasibility. Because ultimately it’s quite simple: We can only sell things that people need and want.”
The Green Village development includes 43,000 m2 of office space, 48 apartments, a hotel and a children’s day-care centre, so this first phase was fairly complicated. Implenia ensured that the coordination between the authorities and all the other stakeholders involved ran smoothly. This is another of our competencies: bringing all the various parties on board as partners and working out alternative approaches whenever the concept needs adjusting. Once the idea has negotiated the first hurdles, it needs a name and a face. Adrian Wyss: “In a pitch with several agencies we developed strong branding for the site; this noticeably speeded up sales.”
The “Green Village” brand name will give the site an identity even after it is completed. As a way of encouraging a sense of community while simultaneously signalling the site’s commitment to sustainability, each building is named after one of the cities that have hosted major climate conferences.
Project development, as we can see, requires thorough planning, professional branding and marketing, as well as a successful sales strategy. Adrian Wyss: “Because we have all these skills in-house, we can coordinate them all perfectly with each other. And, of course, we take care of the technical side. From building technology to construction management, to cost calculations, Implenia offers everything from a single source. This is a huge advantage for customers.”
The earlier you get the right specialists involved in the planning, the better you can exploit internal synergies and organise the implementation phase. You can apply 3D virtual prototyping with BIM, for example, and optimise costs by making targeted use of Lean methods during the actual construction. This is what happened at the Alto Pont-Rouge development in Le Grand-Lancy near Geneva, which Implenia manages as main contractor. Implenia produced a comprehensive set of studies to explore options and optimisations so the client’s wishes could be met at the target price. Costs were reduced and the order was won. Laurent Jarlégant, Project Manager: “BIM played an important role here, because it enabled us to identify possibilities for optimisation more quickly. During the construction phase, our internal BIM experts coordinated all the different parties involved in the project so the customer ultimately has all the information for the operation of the building bundled up together digitally.” In addition, the construction schedule was formulated entirely using Lean methods. Implenia will start building the office block in 2021. It has 35,000 m2 of usable space, including smaller areas for grocery stores and restaurants.
Designing processes efficiently
Stadiums, hospitals, housing developments, hotels, entire neighbourhoods: Implenia is also a genuine generalist in the execution phase, i.e. the actual construction work. “Our real core competence lies in bringing together a network of subcontractors, specialist designers and architects with the necessary skills and expertise,” says Jens Vollmar, Head Division Buildings. “We cover all the areas needed for turnkey construction by integrating specialist external experts from each trade into our teams and coordinating them all professionally.”
No wonder a contract for the development phase is often followed by a contract for the construction itself. This is true of private and public sector jobs. Implenia’s strong track record means that customers can have full confidence. The multi-national construction services provider has established itself as a leader in the realisation of complex real estate projects in Switzerland and Germany. And it is always working on ways to do things even more efficiently.
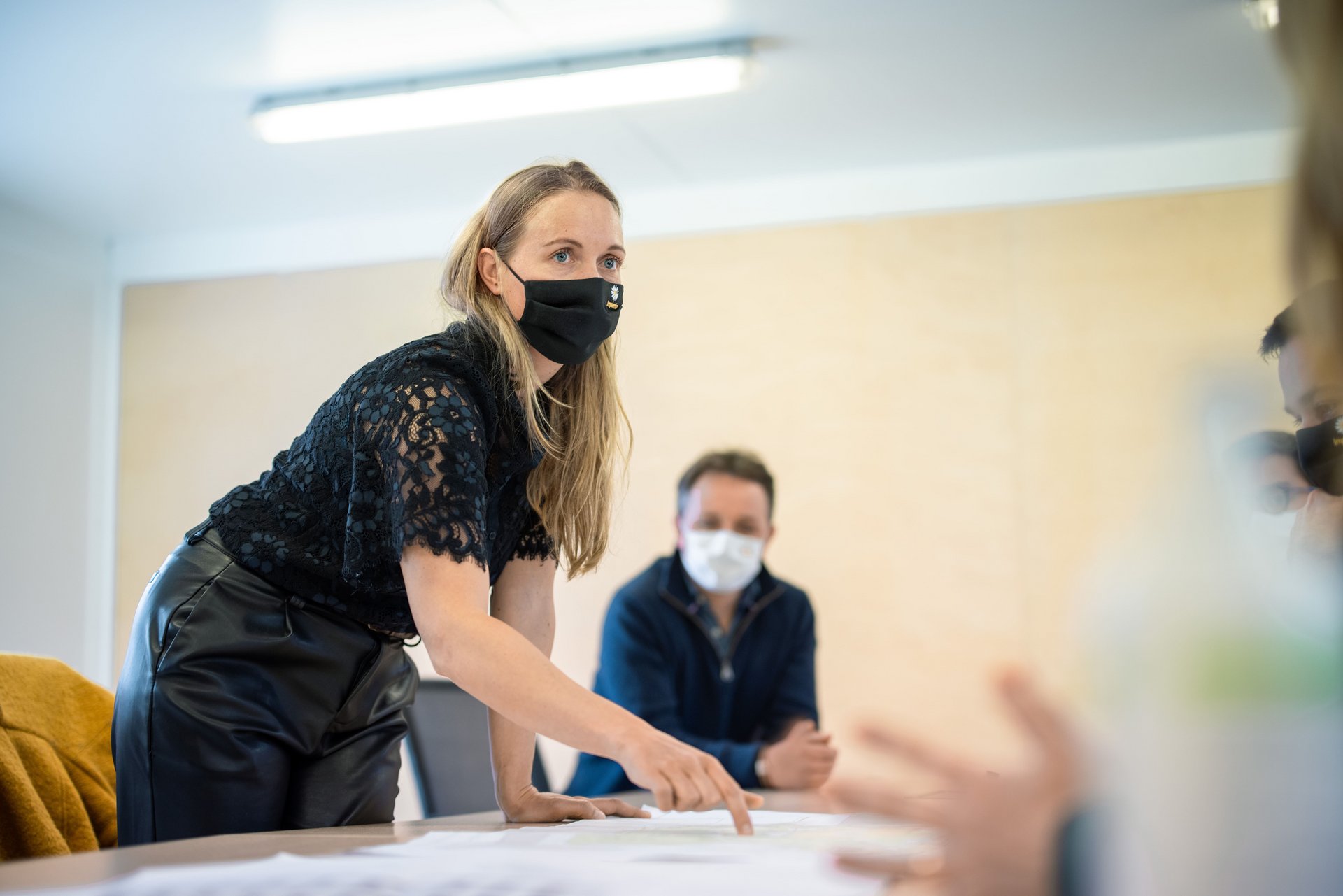
Continuous, close coordination with the design and execution teams guarantees that all the processes run together smoothly from development to implementation.
It is, for example, exploring new business models that take account of the fact that digitalization is blurring the traditional separation of planning and execution. Jens Vollmar: “Even if we are supporting and improving more and more parts of the job with BIM, we’re still building in the real world. But some things will change on construction sites, which is why we will be concentrating more in future on efficient construction logistics.” The industrialisation of construction means that significantly more elements are being prefabricated, which makes precise logistical planning and punctual delivery even more important. These things can be optimised with Lean Construction Management.
The Berswordt-Carrée in Dortmund, where 222 rental apartments and 365 micro-apartments have been created on a 10,900 m 2 site, is a good example of this. Between 2018 and the end of 2020, Implenia, working as a general contractor, built Dortmund’s largest inner city housing project, for which it won the Lean Construction Award from the GLCI (German Lean Construction Institute). Marco Sparman, Project Manager: “We were working conventionally to start with but very quickly realised that to do the preliminary planning properly we needed to structure our processes more effectively. We switched to Lean during the shell construction phase, which allowed us to make up the time we lost at the start.”
One of the big challenges was that there was virtually no storage space on the construction site, so all deliveries had to be organised on a “just-in-time” basis. Baris Kilic, Head Lean Construction in Germany: “A Lean Management method called ‘takt-time planning’, was particularly important: working closely with the on-site team, we developed a model that set out the sequence of construction. Then we worked back from this to calculate which materials would have to be delivered when.” Most of the work used prefabricated elements, so even things like how items should be stacked on the delivery truck had to be thought through in the minutest detail. Kilic: “The uppermost item on the truck had to be the thing we were working with first, otherwise we would have tied up crane capacities and wasted time. And anyway, there was no place to store anything temporarily.” Minimising friction while optimising punctuality, quality and costs: the first major project that Implenia executed in Germany using Lean Methods was a resounding success. Jens Vollmar: “If we can use digital solutions to implement Lean Construction with our subcontractors throughout all aspects of the project, we have a very powerful tool with which to improve our efficiency for customers and position ourselves in the market.”
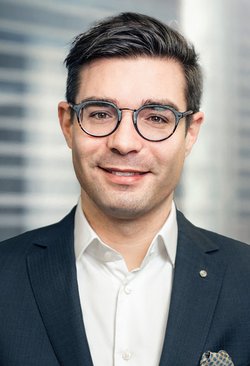
«If we can use digital solutions to implement Lean Construction throughout all aspects of the project, we have a very powerful tool with which to position ourselves in the market.»
Jens Vollmar
Head Division Buildings